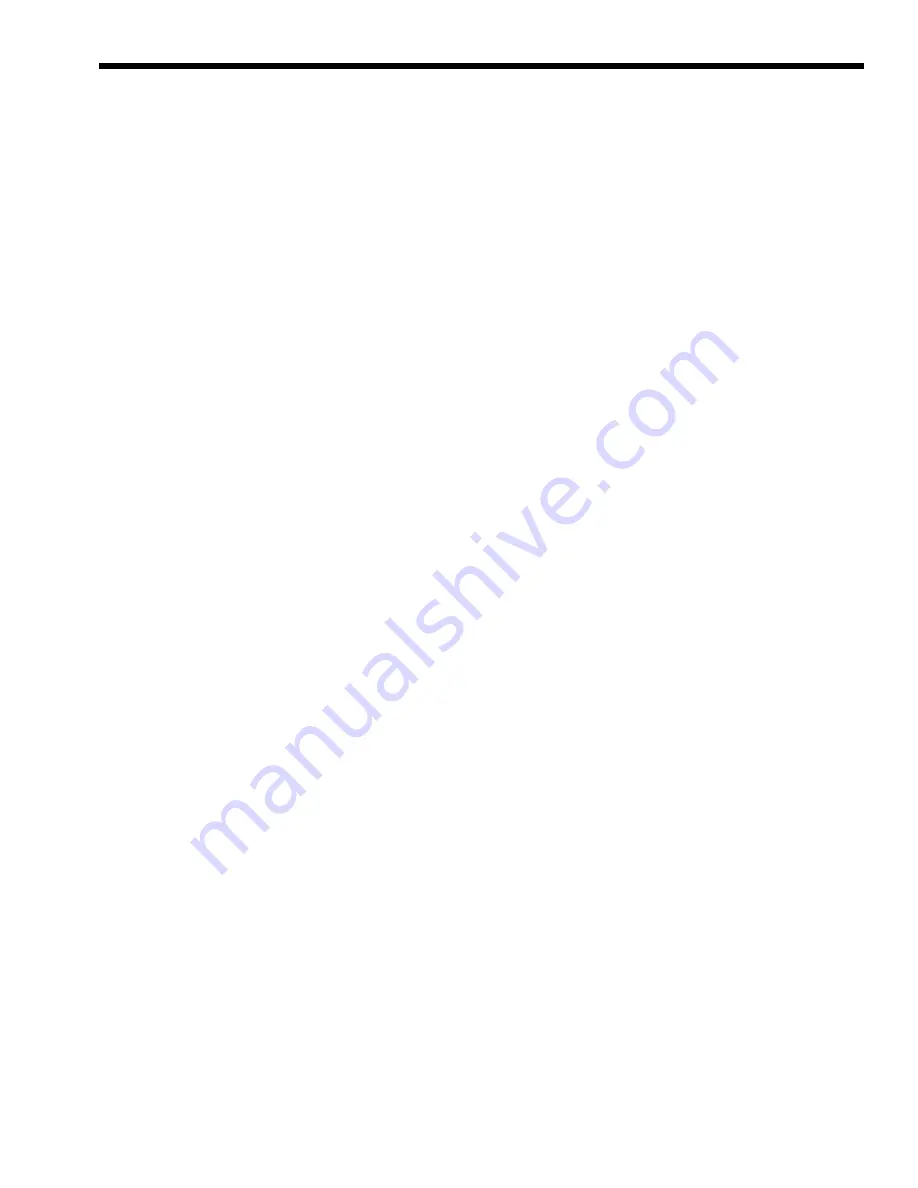
Pennant Pool Heater
Page 23
8.4 High Gas Consumption
Appliances operating with an improper air/fuel
ratio are very inefficient and consequently, have very
high gas consumption. Because efficiency is high
when the CO
2
is high (or O
2
is low), appliances
operating with low CO
2
or high O
2
(especially LP
appliances) consume more gas. Adjust the CO
2
or O
2
for optimum efficiency. If no combustion analyzing
equipment (CO
2
or O
2
) is available then a proper
adjustment of the air/fuel ratio (CO
2
or O
2
) cannot be
accomplished. However, by briefly sniffing the flue
gases it is possible to determine if the CO
2
or O
2
is
within the proper range. No significant flue gas odor
should be detected when combustion is proper. A
strong piercing smell indicates poor combustion and
generally a lean mixture - low CO
2
or high O
2
. The
CO
2
should be 8% (natural gas, 9.2% LP) at high fire.
To check the CO
2
, first verify that the supply gas
pressure is within 5" to 13" w.c. (1.2 to 3.2 kPa) With
the Pennant running with both stages firing, set the air
box pressure to 1.5" w.c. (0.37 kPa) (as a starting
point), by adjusting the air shutter(s) at the bottom of
the fan(s). Check the CO
2
, and adjust the air shutters if
further adjustment to the CO
2
is needed. Sizess 1250,
1500, 1750 and 2000 have two blowers and two air
chambers (boxes). The pressure of each air box must
be equal when the final adjustment is made.
8.5 Troubleshooting the Pool Heater
Temperature Control
With a Voltmeter, test for 24 VAC between
terminals 1 & 2 on the 10 pin connector. Check that
the sensor temperature is lower than the setpoint
temperature by at least the differential setting. If this is
true, check that there is 24 VAC at the yellow wire on
the 4 pin connector. If there is not 24 VAC, check that
the high limit is not open. If there is 24 VAC at the
yellow wire on the 4 pin connector and not at the light
blue wire on that connector, replace the control.
8.6 Troubleshooting Pennant Controls
The Pennant series consists of three sizes with
one ignition module (500, 750 & 1000) and four sizess
with two ignition modules (1250, 1500, 1750 and
2000).
A diagnostic panel, that includes test points, as well
as diagnostic lights, is provided in the control module. It
is located on the right side of the module, behind the
display. To access, remove the retaining screws from the
display cover panel and remove it. Grasp the control
module at its base and pull it outward. Ladder diagrams
are shown in Figures 13 and 14.
Figure 13 shows the diagram for the 500, 750 &
1000. These have one blower and one ignition module.
The blower is energized directly through the “inducer”
terminals F1 and F2 of the (Fenwal) ignition module. The
24V power to the T’STAT terminal of the ignition
module(s) are routed through the safety interlocks.
The ladder diagram for sizess 1250, 1500, 1750
and 2000 is shown in Figure 14. These models have
two ignition modules, each with its own blower, and
each controlling part of the input so that startup at
reduced input is provided. The blowers are energized
by the ignition modules indirectly via switching
relays. When either ignition module receives a call for
heat, it switches its blower to high speed and the
blower of the idle ignition module to low speed.
The wiring schematic for the Pennant 500 – 1000
is shown in Figure 15, and the schematic for the 1250
– 2000 models is shown in Figures 16 and 17. All 24V
wiring is routed through the diagnostic PC board.
Wiring harnesses connect between the diagnostic PC
board and the control components, indicator board, or
field wiring terminal strip. The diagnostic board
contains LEDs that indicate open status of the safety
interlocks, and quick-connect terminals that provide
tests points for checking voltage/continuity at various
points in the control circuit.
Certain control elements that may need to be
rewired in the field are connected via the field wiring
terminal strip rather than to the diagnostic PC board.
These include the low-water cutoff (LWCO), external
alarm, and water flow switch.
SECTION 9.
Replacement Parts
Only genuine Laars replacement parts should be used.
9.1 General Information
To order or purchase parts for the Laars Pennant,
contact your nearest Laars dealer or distributor. If they
cannot supply you with what you need, contact
Customer Service (see back cover for address,
telephone and fax numbers).
9.2 Parts List
See next page.
Summary of Contents for PNCP
Page 30: ...LAARS Heating Systems Page 30 Figure 10 Sheet Metal Components...
Page 31: ...Pennant Pool Heater Page 31 Figure 11 Internal Components...
Page 34: ...LAARS Heating Systems Page 34 Figure 14 Pennant 1250 2000 Ladder Diagram...
Page 35: ...Pennant Pool Heater Page 35 Figure 15 Pennant 500 1000 Wiring Schematic...
Page 36: ...LAARS Heating Systems Page 36 Figure 16 Pennant 1250 1500 Wiring Schematic...
Page 37: ...Pennant Pool Heater Page 37 Figure 17 Pennant 1750 2000 Wiring Schematic...
Page 38: ...LAARS Heating Systems Page 38 Figure 18 Field Wiring...
Page 39: ...Pennant Pool Heater Page 39...