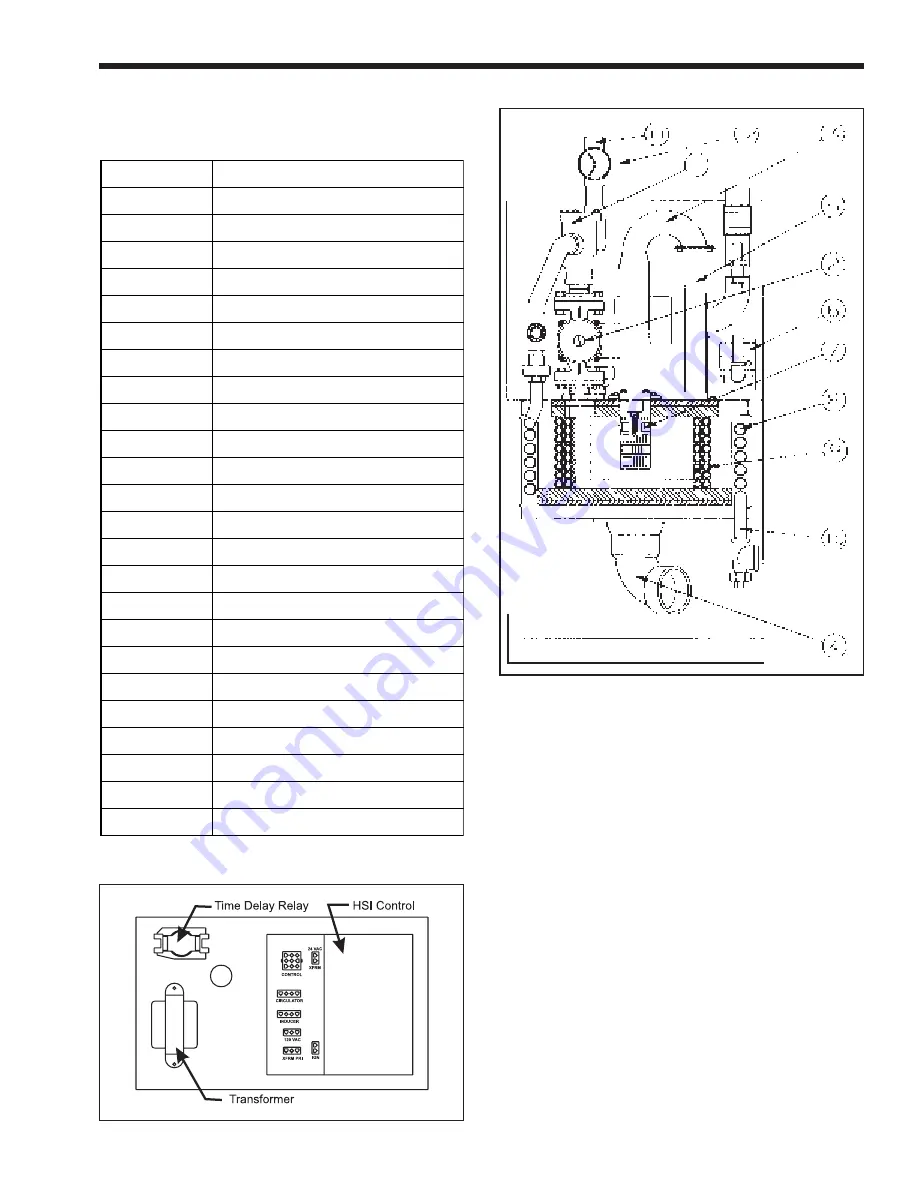
9600 HWG Water Heater
Page 17
SECTION 7.
Replacement Parts List
Note: Reference page 15 for electrical components
Figure 19. Control box.
(1) Thermostatic Valve
(2) Circulator
(3) Mixer Tube
(4) Exhaust Pipe
(5) Blower
(6) Gas Valve
(7) Burner
(8) Economizer
(9) Combustion Coil
(10) Water Inlet from Tank
(11) Hot Water Outlet to Tank
(12) Air Vent
Figure 20. Assembly view of the unit.
Part Number
Description
2400-322
Gasket Kit
2400-079
Blower Assembly (#5)
2400-310
Blower Assembly (HWG-250)
2400-086
Combustion Coil Assembly (#9)
2400-082
Flame Holder (#7)
2400-308
Flame Holder (HWG-250)
2400-286
Ignitor
2400-088
Capacitor, Motor Starter
2400-224
Control Board
2400-014
Gas Valve, Neg. Pres. (#6)
2400-015
Gas Valve, Neg. Pres. (HWG-250)
2400-106
Pressure Diff. Switch (HWG-250)
2400-058
Intake / Exhaust TCO
2400-057
Operating Limit
2400-054
Safety Limit
2400-062
Time Dealy Relay
2400-130
Thermostat Kit (140°F) (#1)
2400-006
Transformer
2400-094
Pressure Relief Valve (150 psi)
2400-095
P.R. Valve (250 only) (150 psi)
2400-090
Pump, Grundfos Up 26-99BF (#2)
2400-104
Exhaust Terminal
2400-102
Intake Terminal
2400-100
Wall Flange