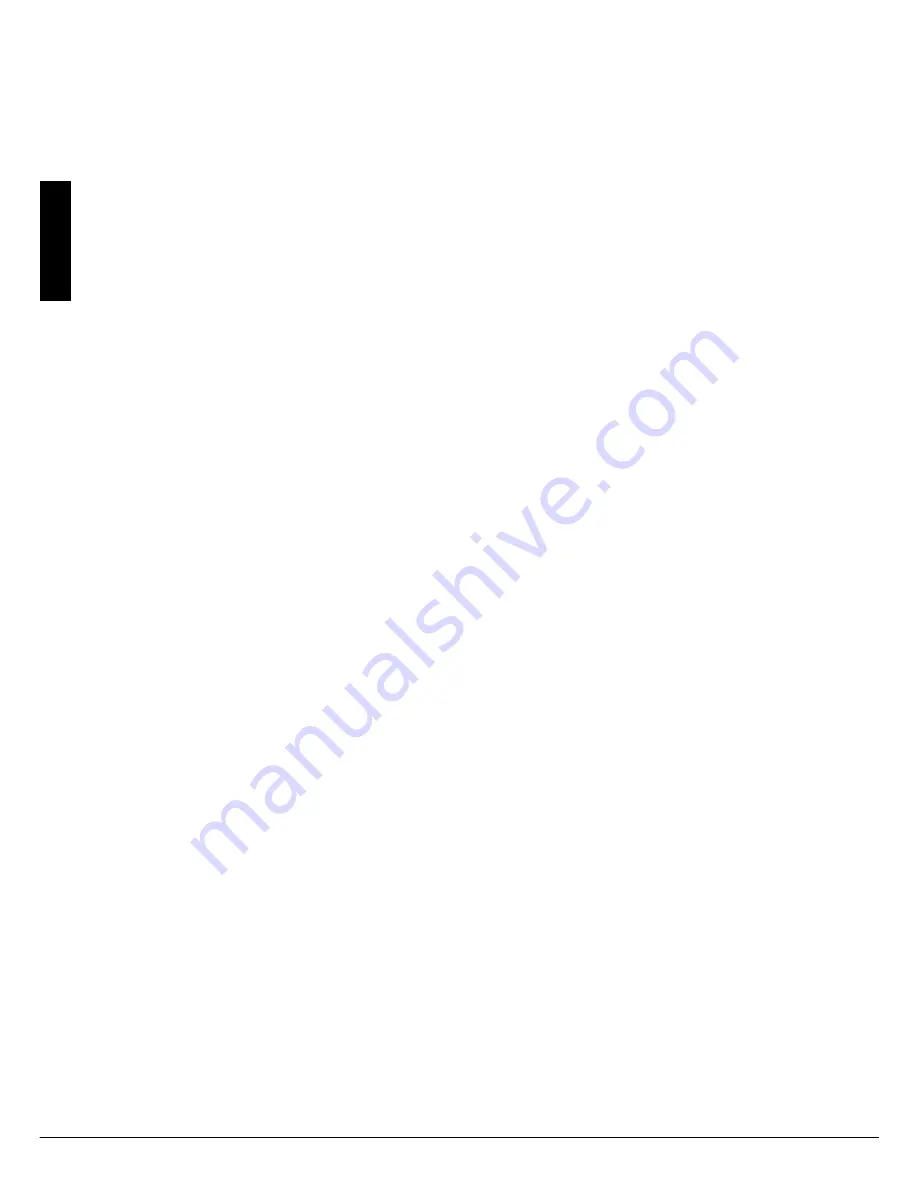
degree in order to adapt it to the optimal temperature,
depending on the type of coffee mix being used.
The brewing groups, cast in brass and weighing 3 Kg
each approximately, work like thermal “flywheels”. They
are connected directly to the boiler by means of a large
manifold and are thus an integral part of the boiler itself.
The manifold is shaped in such a way that each group is
located at a greater height than the boiler, so that, just
like in the elements of a thermosiphon, a natural circula-
tion of hot water takes place within each group, at the
same temperature of the boiler and kept constant by the
thermostatic system described previously. The use of
these small boilers, completely independent from one
another, the special manifold and fastening system of the
groups to the boiler as well as the “thermostatic” tem-
perature control, have allowed us to:
1) achieve an excellent thermal equilibrium between the
brewing groups, both at times of discontinuous opera-
tion and during peak times;
2) be able to control the temperature of the water run-
ning through the brewing groups, independently of the
“pressure” and the level in the small steam boiler, and
therefore to optimize the water temperature itself in
order to obtain the best possible coffee with whatever
coffee mixes are available commercially;
3) save on electrical energy by more than 30%, in many
cases, when compared to other machines.
The “LINEA” series machines are produced in the 1, 2, 3
and 4 group versions, the model “EE” having continuous
brewing operation and the “AV” model positive-displa-
cement automatic brewing.
CONTROL SYSTEMS AND SAFETY DEVICES BUILT INTO
“LA MARZOCCO” COFFEE MACHINES
All models are equipped with:
- automatic level regulator;
- automatic pressure regulator;
- automatic temperature regulator;
- safety devices
Spring operated safety valve;
Manual thermostats.
In both models, coffee is brewed by opening a solenoid
valve, one for each group. For the “EE” model, the quan-
tity of coffee brewed is regulated manually by the ope-
rator through a switch, while in the “AV” model the
quantity is regulated automatically in 4 different doses,
which may be programmed at will for each brewing
group. This last model is equipped with control panels,
one located above each group, with 4 buttons which
may be programmed in such a way that by pressing the
1st button you get 1 regular coffee, pressing the 2nd one
you get one tall coffee, pressing the 3rd you get 2 regu-
lar coffees and by pressing the 4th one you get 2 tall cof-
fees. The fifth button, which has a spiral sign, allows con-
tinuous brewing operation which can be interrupted by
pressing the very same button again.
CONSTRUCTION DETAILS
They consist essentially of 2 small boilers, of which:
1. “C.C.” hot water generator for brewing coffee.
2. “C.V.” steam generator for producing steam and hot
water for making tea and other hot drinks.
1. Description of the Coffee Boiler (C.C.)
Composed of an ASTM A 312 TP 304 ECS stainless steel
tube, with an ext. dia. of 101.6 mm and a thickness of 3 mm.
Heating is accomplished through an immersion-type pla-
ted heating element.
Operating temperature 95° C, controlled automatically
by a thermostatic switch, adjusted to 95° C with a diffe-
rential of ±1° C.
Operating pressure of 9 bar, developed mechanically by
a special positive-displacement pump which is activated
automatically every time coffee is brewed.
Pressure is controlled through a pressure gauge with a
scale from 0 to 15 bar.
Safety device, based on an expansion type mechanical
valve, with counter-acting spring adjusted to 11 bar.
Testing:
a.
hydraulic test at 16 bar performed on the ready-to-use
small boilers, at our factory;
b.
hot water test at 11-12 bar performed on the ready-
to-use small boilers, at our factory.
2. Description of the Hot Water Boiler (C.V.)
Composed of an ASTM A 312 TP 304 ECS stainless steel
tube, with an ext. dia. of 154 mm and a thickness of 2
mm.
Heating is accomplished through an immersion-type pla-
ted heating element.
-Operating pressure of 1.5 bar, controlled automatically
through a manostat, adjusted so as to open the heating
element supply circuit at 1.5 bar and close it at 1.3 bar.
-The pressure is regulated by means of a pressure gauge
with a scale of 0 to 2 bar.
-Safety device, based on an expansion type mechanical
valve, with counter-acting spring adjusted to 1.7 bar.
Testing:
a.
hydraulic test at 3 bar performed on the ready-to-use
small boilers, at our factory;
b.
hot water test at 1,5 bar performed on the ready-to-
use small boilers, at our factory.
Capacity and Power Ratings
1. C.C.
- 1 group
1,8 litres
1.000 Watt
- 2 groups
3,4 litres
1.400 Watt
- 3 groups
5,0 litres
1.600 Watt
- 4 groups
2x3,4 litres
2x1.400 Watt
2. C.V.
- 1 group
3,5 litres
1.300 Watt
- 2 groups
7 litres
2.000 Watt
- 3 groups
11 litres
3.000 Watt
- 4 groups
15 litres
3.800 Watt
16
English