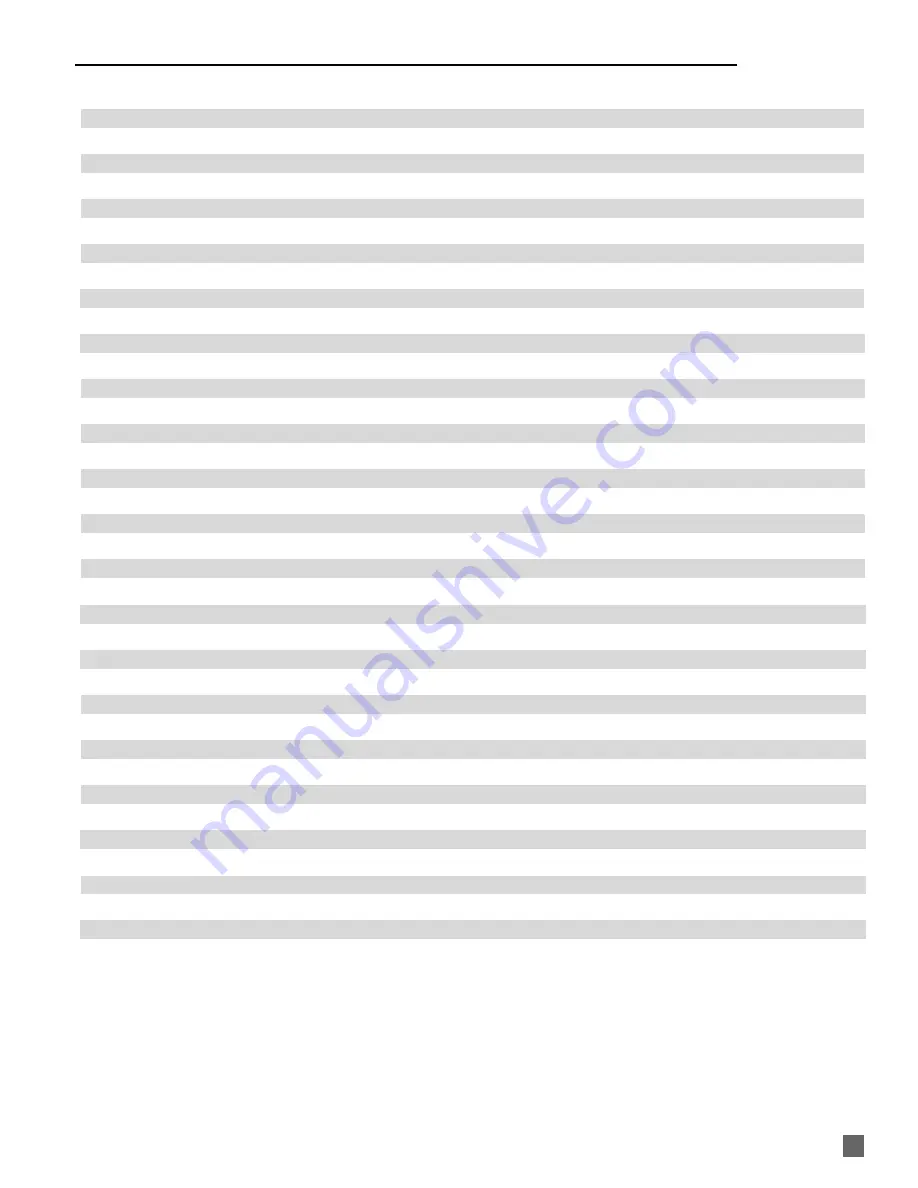
PARTS LIST
29
Item
Description
Part No.
6
Kit, Sediment Trap
00815
7
Base
21051
8
Cover, Gas Control Valve
09287
9
Bracket, Gas Control Valve
09506
10
Valve, Gas Control (L.P. Gas)
22219
Valve, Gas Control (Natural Gas)
22221
11
Nipple
07148
12
Elbow
01426
13
Manifold
09291
14
Orifice, Burner (L.P. Gas)
20049
Orifice, Burner (Natural Gas)
21113
15
Gasket, Pilot (Natural Gas)
06974
16
Thermocouple, 750 mm
21196
17
Tubing, Pilot with Nuts
21126
18.
Orifice, Pilot (L.P. Gas)
07829
Orifice, Pilot (Natural Gas)
06968
19.
Bracket, Pilot Burner
07831
20.
Shield, Pilot Barrel Assembly
21128
21.
Terminal Block (5 position)
08253
22.
Transformer, 240/24 VAC
20045
23.
Enclosure, Electrical
20028
24.
Cover, Electrical
20027
25.
Burner
03453
26.
Spacer
02687
27.
Switch, High Limit
05566
28.
Chamber, Heat
20024
29.
Door, Right or Left
20757
30.
Cord, Power
20359
31.
Latch Assembly
20959
32.
Case, Assembly with Doors and Latches
21129
33.
Hinge
05868
34.
Motor, 187 Watts
20668
35.
Mount, Motor
08647
36.
Fan, Wheel
09050
37.
Switch, Air Flow with Screws and Nuts
02680
38.
Sail, Air Flow
21035
39.
Housing Fan, with Sail, Air Flow Switch and Motor Mount
20250