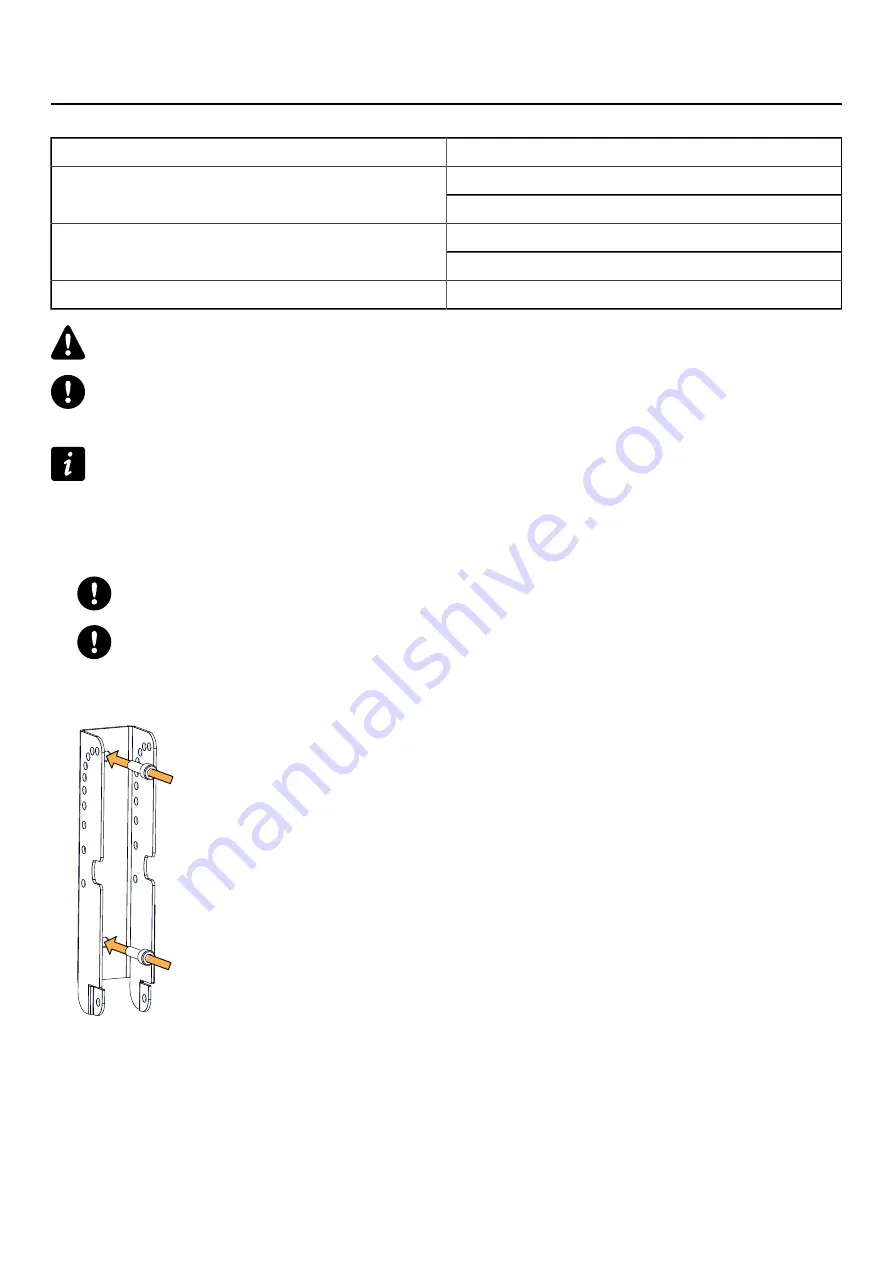
Rigging procedures
Using a U-bracket with X-UTILT
type of deployment
wall-mounting
X-US1215 or X-UL12
rigging accessories
X-UTILT
2 x M10 screws
additional material
electric screwdriver
min number of operators
1
Additional safety for own arrays
When ying an enclosure or an array, use the M8 DIN580 threaded insert to implement a secondary safety.
Fasteners for wall-mounting
Secure the X-UTILT with two M10 screws.
Select screw length and anchors applicable to the wall properties.
The procedure is shown with X-UL12
The same procedure applies for X-US1215.
Assembly
Procedure
X-UTILT shall only be used vertically.
Fasteners for wall-mounting
Secure the X-UTILT with two M10 screws.
Select screw length and anchors applicable to the wall properties.
1.
Secure X-UTILT to the wall using M10 screws.
50
X12 owner's manual (EN) version 1.0