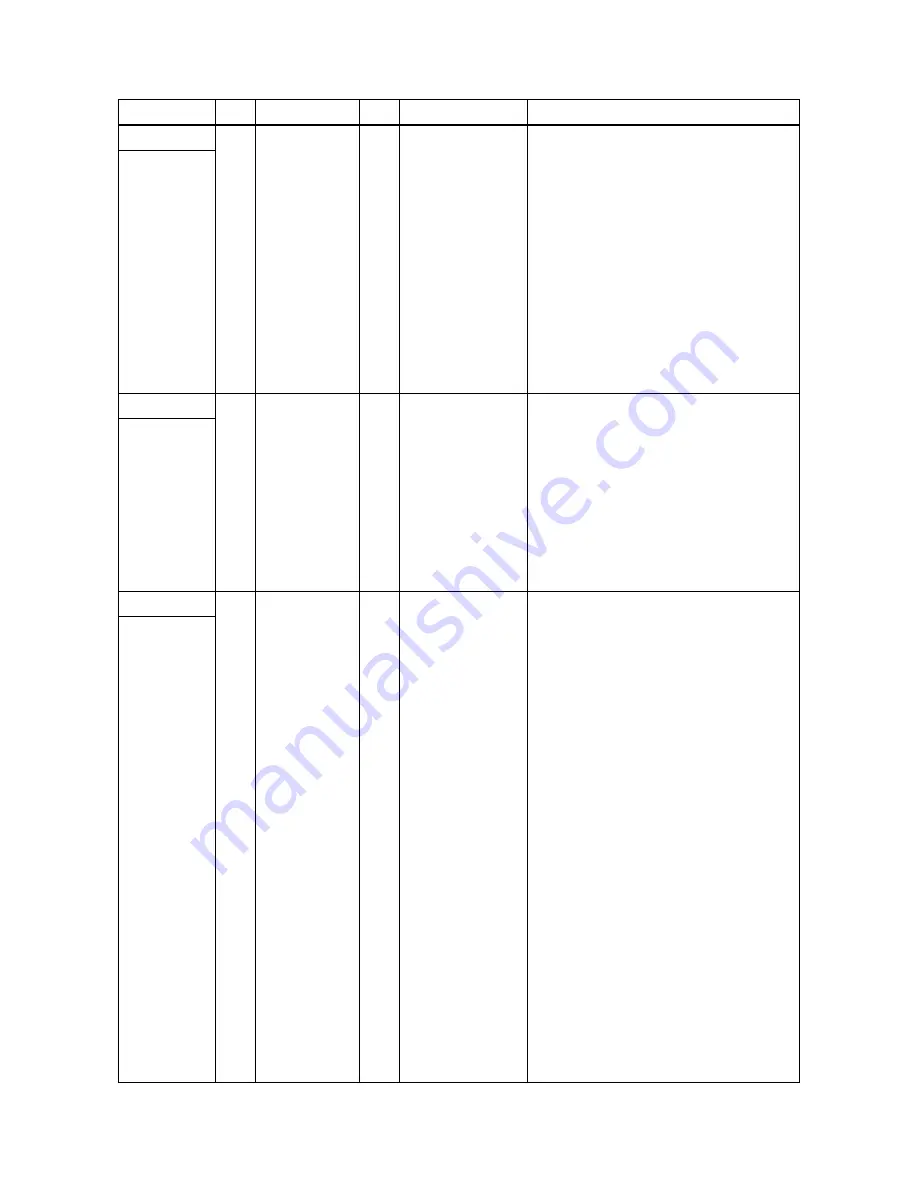
2K3/2L3
2-3-12
YC15
1
3.3V4
O
3.3V DC
3.3V DC power output to DRPWB
Connected to
drum relay
PWB
2
DRUM_SDA
I/O
0/3.3 V DC(pulse)
DRPWB EEPROM data signal
3
DRUM_SCL
O
0/3.3 V DC(pulse)
DRPWB EEPROM clock signal
4
GND
-
-
Ground
5
WT_LED
O
0/3.3 V DC
WTL: On/Off
6
WT_SENS
I
Analog
WTS detection signal
7
3.3VLED
O
3.3V DC
3.3V DC power output to WTS
8
ERASE
O
0/24 V DC
CL: On/Off
9
24V4
O
24 V DC
24 V DC power output to CL
YC16
1
MAIN_DIR
O
0/3.3 V DC
MM drive shift signal
Connected to
main motor
2
MAIN_READY
I
0/3.3 V DC
MM ready signal
3
MAIN_CLK
O
0/3.3 V DC(pulse)
MM clock signal
4
MAIN_REM
O
0/24 V DC
MM: On/Off
5
GND
-
-
Ground
6
24VIL2
O
24 V DC
24V DC power output to MM
YC18
1
GND
-
-
Ground
Connected to
DP main
PWB
2
GND
-
-
Ground
3
24V4
O
24 V DC
24V DC power output to DP
4
24V4
O
24 V DC
24V DC power output to DP
5
DP_CLK
O
0/3.3 V DC(pulse)
DP clock signal
6
DP_SO
O
0/3.3 V DC(pulse)
Serial communication data signal
7
DP_SEL
O
0/3.3 V DC
DP select signal
8
DP_SI
I
0/3.3 V DC(pulse)
Serial communication data signal
9
DP_RDY
I
0/3.3 V DC
DP ready signal
10
DP_TMG
I
0/3.3 V DC
DPTS: On/Off
11
DP_OPEN
I
0/3.3 V DC
DPOCS: On/Off
Connector
Pin
Signal
I/O
Voltage
Description
Summary of Contents for 255b
Page 4: ...This page is intentionally left blank...
Page 10: ...This page is intentionally left blank...
Page 24: ...2K3 2L3 1 1 10 This page is intentionally left blank...
Page 162: ...2K3 2L3 1 4 38 This page is intentionally left blank...
Page 238: ...2K3 2L3 2 2 10 This page is intentionally left blank...
Page 281: ...Installation Guide Paper feeder Installation Guide...
Page 283: ...11 12 13 14 13 14 2010 9 303NN56710 8 9 10...
Page 284: ...Document finisher Installation Guide...
Page 286: ...8 6 7 9 5 8 10 2010 9 305JS56710 G F E Black White MFP 25 30 Color MFP 20 25 D C...
Page 287: ...FAX System U Installation Guide...
Page 288: ......
Page 289: ......
Page 290: ......
Page 291: ......