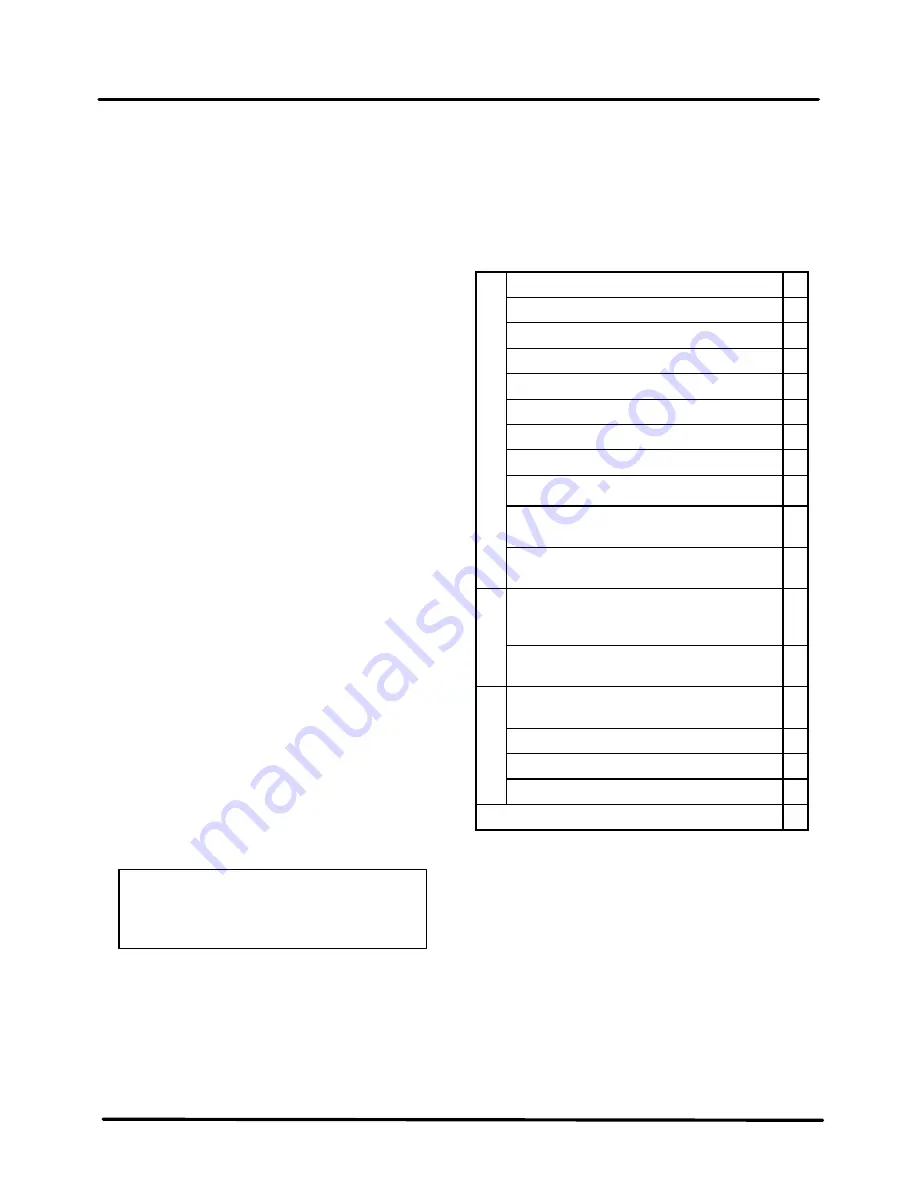
PREFACE
This Service Manual describes the
technical features and servicing
procedures for the KYMCO
MX’er
125/150.
Section 1 contains the precautions for
all operations stated in this manual.
Read them carefully before starting any
operation.
Section 2 is the removal/installation
procedures for the frame covers which
are subject to higher removal/installation
frequency during maintenance and
servicing operations.
Section 3 describes the inspection/
adjustment procedures, safety rules and
service information for each part, starting
from periodic maintenance.
Sections 4 through 17 give instructions
for disassembly, assembly and
inspection of engine, chassis frame and
electrical equipment.
Most sections start with an assembly or
system illustration and troubleshooting
for the section. The subsequent pages
give detailed procedures for the section.
KWANG YANG MOTOR CO., LTD.
OVERSEAS SALES DEPARTMENT
OVERSEAS SERVICE SECTION
TABLE OF CONTENTS
GENERAL INFORMATION
1
FRAME COVERS/EXHAUST MUFFLER
2
INSPECTION/ADJUSTMENT
3
LUBRICATION SYSTEM
4
FUEL SYSTEM
5
ENGINE REMOVAL/INSTALLATION
6
CYLINDER HEAD/VALVES
7
CYLINDER/PISTON
8
DRIVE AND DRIVEN PULLEYS
9
FINAL REDUCTION/TRANSMISSION
SYSTEM
10
CRANKCASE/CRANKSHAFT/
BALANCE SHAFT
11
FRONT WHEEL/FRONT BRAKE/
FRONT SUSPENSION/STEERING
SYSTEM
12
REAR WHEEL /SWING
ARM/HYDRAULIC BRAKE
13
BATTERY/CHARGING SYSTEM/A.C.
GENERATOR
14
IGNITION SYSTEM
15
STARTING SYSTEM
16
LIGHTS/SWITCHES
17
ONLY ATV ON ROAD AVAILABLE
18
The information and contents included
in this manual may be different from
the motorcycle in case specifications
are changed.
CHASSIS
ELECTRICAL
EQUIPMENT
ENGINE
Summary of Contents for LA30AA
Page 24: ...1 GENERAL INFORMATION 1 22 MX er SYSTEM WIRING DIAGRAM...
Page 32: ...2 FRAME COVERS EXHAUST MUFFLER 2 1 MX er SYSTEM...
Page 63: ...5 FUEL SYSTEM 5 1 MX er SYSTEM...
Page 79: ...7 CYLINDER HEAD VALVES 7 1 MX er SYSTEM...
Page 92: ...8 CYLINDER PISTON 8 1 MX er SYSTEM...
Page 101: ...9 DRIVE AND DRIVEN PULLEYS 9 1 MX er SYSTEM 5 5kg m 5 5kg m 5 5kg m...
Page 111: ...9 DRIVE AND DRIVEN PULLEYS 9 11 MX er SYSTEM CLUTCH DRIVENPULLEYASSEMBLY Circlip Clutch Lining...
Page 115: ...9 DRIVE AND DRIVEN PULLEYS 9 15 MX er SYSTEM...
Page 117: ...10 FINAL REDUCTION TRANSMISSION SYSTEM 10 1 MX er SYSTEM...
Page 127: ...11 CRANKCASE CRANKSHAFT BALANCE SHAFT 11 1 MX er SYSTEM...
Page 133: ...11 CRANKCASE CRANKSHAFT BALANCE SHAFT 11 7 MX er SYSTEM...
Page 135: ...12 FRONT WHEEL FRONT BRAKE FRONT SUSPENSION STEERING SYSTEM 12 1 MX er SYSTEM...
Page 155: ...13 REAR WHEEL SWING ARM HYDRAULIC BRAKE 13 1 MX er SYSTEM...
Page 210: ...18 ONLY ATV ON ROAD AVAILABLE 18 1 MX er SYSTEM WIRING DIAGRAM...