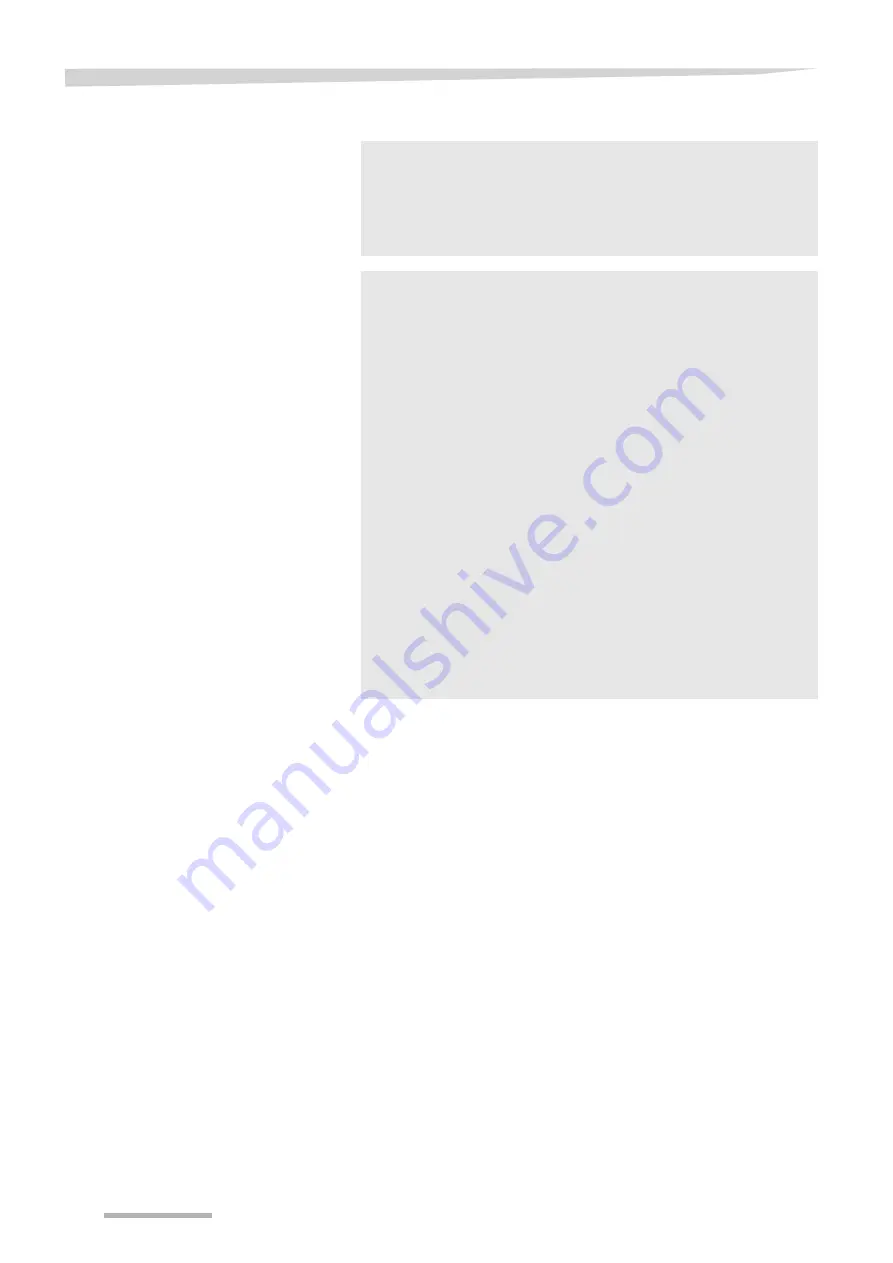
Maintenance
82
Replacement of the
hydraulic system parts
Ensure that the tractor and machine hydraulic systems are not
pressurized.
Identify the connectors using the color code to avoid incorrect
connections (inverting the functions could cause accidents).
\
DANGER
Work on the hydraulic system must only be carried out by a
trained and authorized technician
.
\
DANGER
The hydraulic system is pressurized.
Before any intervention on the hydraulic system:
Lock the folding extension and all the hydraulically controlled
accessories in rest position.
Reduce the pressure between the tractor and the machine.
Reduce the pressure between the hydraulic accumulators and
the cylinders, even when the accumulators are located on the
cylinders.
Failure to carry out these actions could result in serious
injury or death.
The accumulators contain pressurized gas even when the
hydraulic pressure has dropped.
The hydraulic circuits may be equipped with blocking components.
Consequently, even if you think that the pressure has dropped, be
careful.
Summary of Contents for CLC Evo
Page 8: ...Safety 8 ...
Page 9: ...Safety 9 Folding machines ...
Page 10: ...Safety 10 ...
Page 72: ...Maintenance 72 5 00 folding chassis Double tube roller bar ...