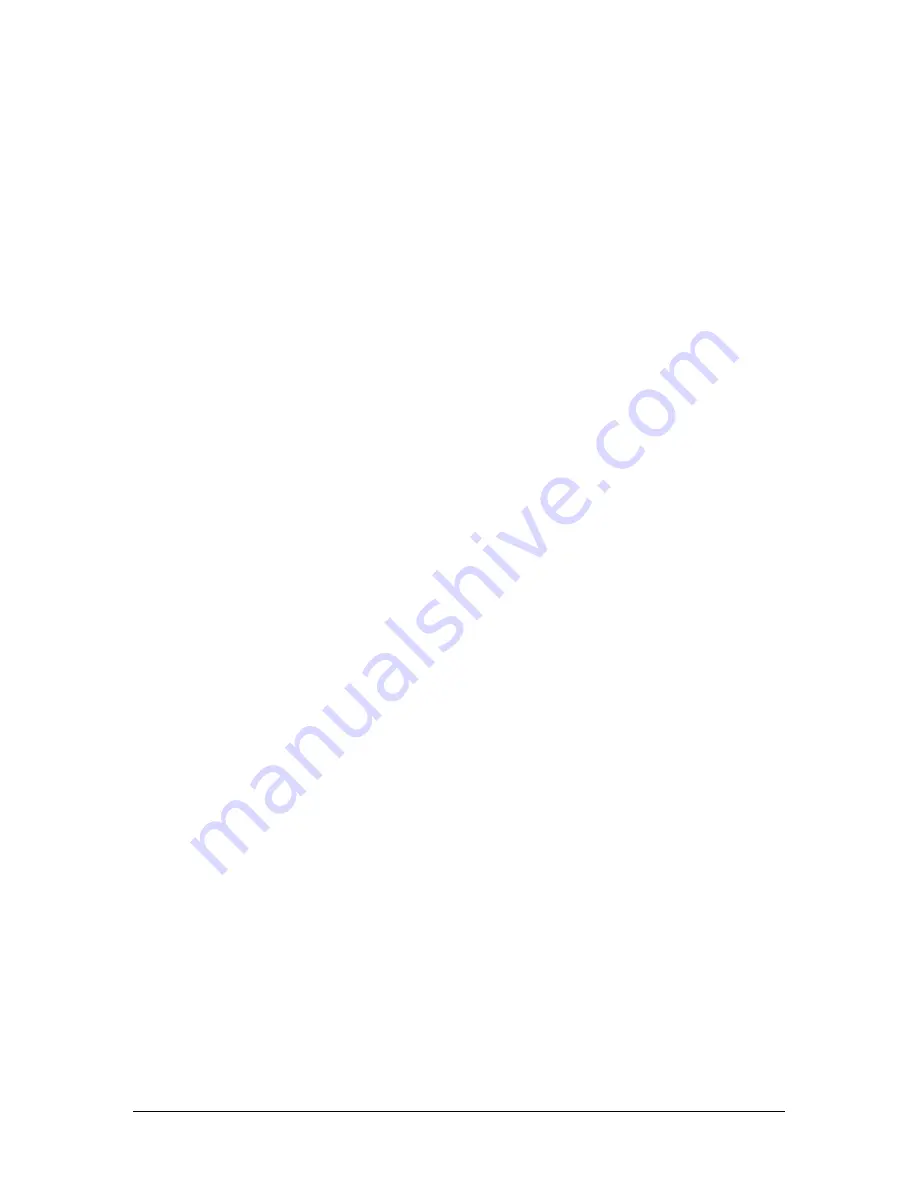
13
LOCK RULES
1.
Use an appropriate “Lock-Out Device”, such as Lock Tongs, or a Lock Tag. Each person must
attach his or her own lock to the Lock-Out Device.
2. Identify
Locks
Each lock will be identified by a number or a name. A lock without a tag is not good enough.
Additional information that identifies the person / persons doing the work must be on the tag. Also
the type of work that is being performed should be on the tag.
3. Sign The Tag
In some instances one tag is enough, however, the tag must be signed by each worker. In some
circumstances a supervisor will also need to sign the tag.
4.
One Key Per Lock
5.
Never give your key to anyone else.
Recheck controls and return to proper setting
P-R-O-P-E-R ELECTRICAL LOCK-OUT
P Process Shut Down
Open disconnect before pulling the plug. Shut down process or equipment.
R Recognize Energy Type
Recognize the correct power source.
O Off! -Shut off all Power Controls
Shut off machine and electrical energy at both machine and main power switch. There may be
more than one source of power and all must be shut off. If necessary, electrical drawings and a
supervisor may need to be involved.
P Place Lock-Out Device, Lock and Tag
Each person working on equipment needs to put his or her lock on the switches and sign the tag.
E Energy - Release Stored Energy
Bleed electrical capacitors if any.
R Recheck Controls and Return To “OFF” Setting
Recheck the start button and properly test that you have zero energy state.