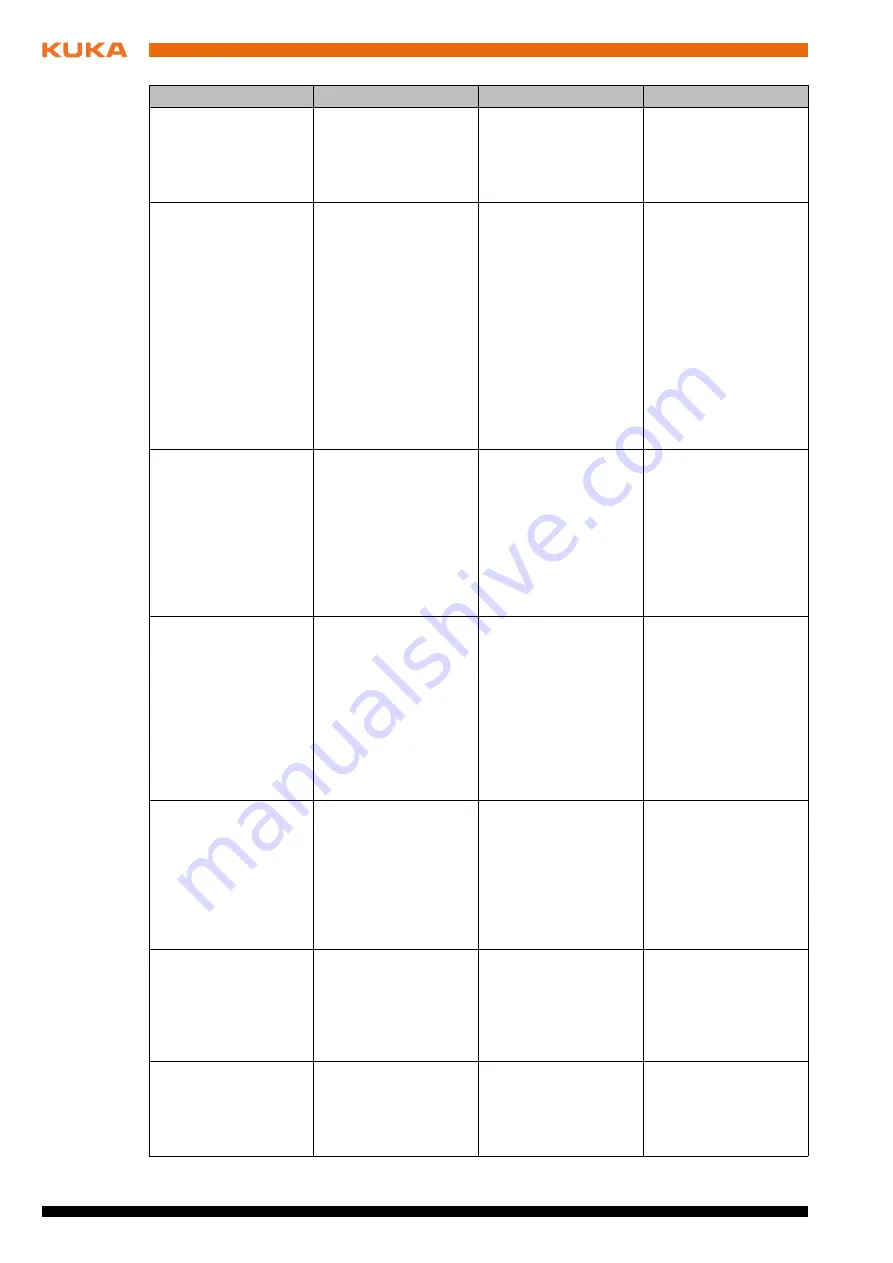
52 / 65
Issued: 29.11.2012 Version: KR C4 Interbus 1.1 V2 en (PDF)
%1 Restart already in
progress.
A restart is being car-
ried out (possibly
automatically).
No input and outputs
data are exchanged
with the controller
board.
If the automatic
restart has been acti-
vated in the XML file
of the driver, deacti-
vate it again.
%1 Error accessing
controller board.
Possible causes:
Controller board is
defective and
must be ex-
changed.
or
The board number
in the XML file
does not match
the board number
set on the control-
ler board.
The driver cannot ini-
tialize the controller
board. Communica-
tion with the controller
board is not possible.
Depending on the
cause, either the con-
troller board must be
exchanged or the
board number in the
XML file must be
adapted.
%1 waiting for exter-
nal start of Interbus.
The Interbus driver
has been set to true
with the
“EXTERN_START”
flag and is now wait-
ing for the Interbus to
be started externally,
e.g. using the CMD
tool.
No I/O data are exe-
cuted with the Inter-
bus.
Either set
“EXTERN_START”
flag to false, start the
Interbus via a tool or
use a boot project.
%1 Caution! Bus
mode is not 'Asyn-
chronous with syn-
chronization pulse'.
Notification message
that the Interbus is not
in “Asynchronous with
synchronization
pulse” mode.
Correct functioning of
the Interbus driver is
only assured in
“Asynchronous with
synchronization
pulse” mode. In the
other modes, it is pos-
sible, for example,
that data may not be
written to the outputs.
Switch the bus mode
back to “Asynchro-
nous with synchroni-
zation pulse”.
%1 slave address
unknown.
The driver was unable
to determine the
address of the con-
troller board slave.
Either it has not been
configured, or the
slave could not be
started.
The driver is not
started, as it is not
possible to access the
I/O data of the slave.
Configure the address
of the slave, e.g. in
the CMD tool.
%1 slave ID on card
(%2) is different from
that in XML file (%3).
The slave ID on the
card is configured dif-
ferently from that
specified in the XML
file of the driver.
If the higher-level
master expects a dif-
ferent slave ID, a bus
error will be gener-
ated in the higher-
level ring.
Either the ID in the
XML file is incorrect,
or the slave has been
incorrectly configured
(e.g. via the DIP
switches).
%1 Version mis-
match in the file %2,
required version is
%3.
The file that has been
read has a different
identifier from that
required by the cur-
rent software.
The data from the file
cannot be used.
Use the correspond-
ing version of the file
and adapt the data in
the new file if neces-
sary.
Message
Reason
Effect
Remedy
Summary of Contents for Interbus 1.1
Page 8: ...8 65 Issued 29 11 2012 Version KR C4 Interbus 1 1 V2 en PDF Interbus 1 1...
Page 12: ...12 65 Issued 29 11 2012 Version KR C4 Interbus 1 1 V2 en PDF Interbus 1 1...
Page 20: ...20 65 Issued 29 11 2012 Version KR C4 Interbus 1 1 V2 en PDF Interbus 1 1...
Page 62: ...62 65 Issued 29 11 2012 Version KR C4 Interbus 1 1 V2 en PDF Interbus 1 1...
Page 64: ...64 65 Issued 29 11 2012 Version KR C4 Interbus 1 1 V2 en PDF Interbus 1 1...
Page 65: ...65 65 Issued 29 11 2012 Version KR C4 Interbus 1 1 V2 en PDF Interbus 1 1...