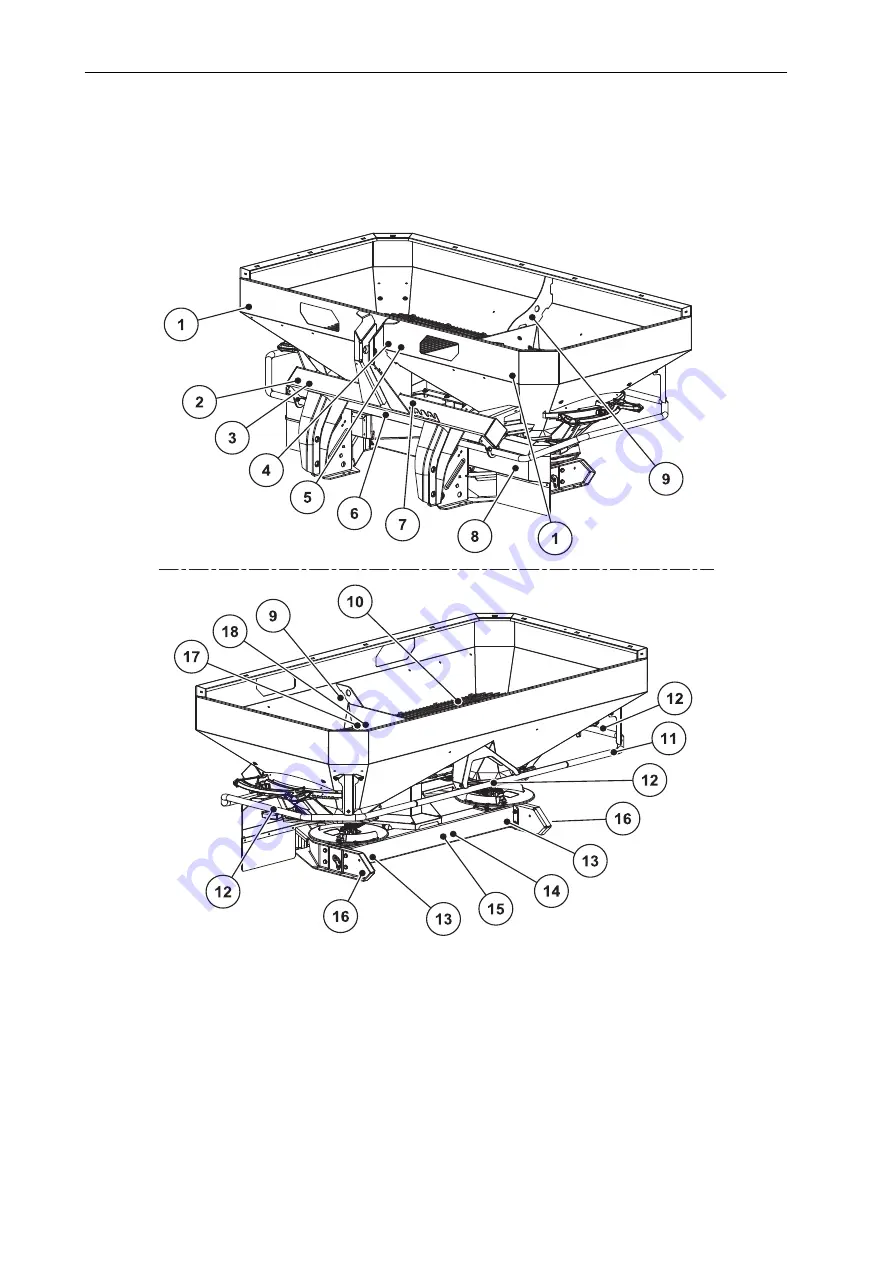
Safety
3
14
3.10
Protective equipment built into the machine
3.10.1
Positioning of the protective equipment
AXIS H 30.1 EMC, AXIS H 30.1 EMC + W
Figure 3.1:
Position of protection devices, warning and instruction notices and reflectors
[1]
White reflector in front
[2]
Nameplate
[3]
Serial number
[4]
Warning: read operator's manual
[5]
Material ejection warning
[6]
KS/LS conversion
[7]
Maximum payload warning
[8]
Spreading disc cover
[9]
Eyelet in hopper notice
[10] Protective screen in hopper
[11] Deflector bracket
[12] No-climbing notice
[13] Red reflector
[14] Warning: remove ignition key
[15] Moving parts warning
[16] Yellow side reflector
[17] Protective screen lock
[18] Instructions for protective screen lock
Summary of Contents for AXIS H 30.1 EMC
Page 2: ......
Page 4: ......
Page 10: ...Intended use 1 2 ...
Page 36: ...Technical data 4 28 ...
Page 40: ...Axle load calculation 5 32 ...