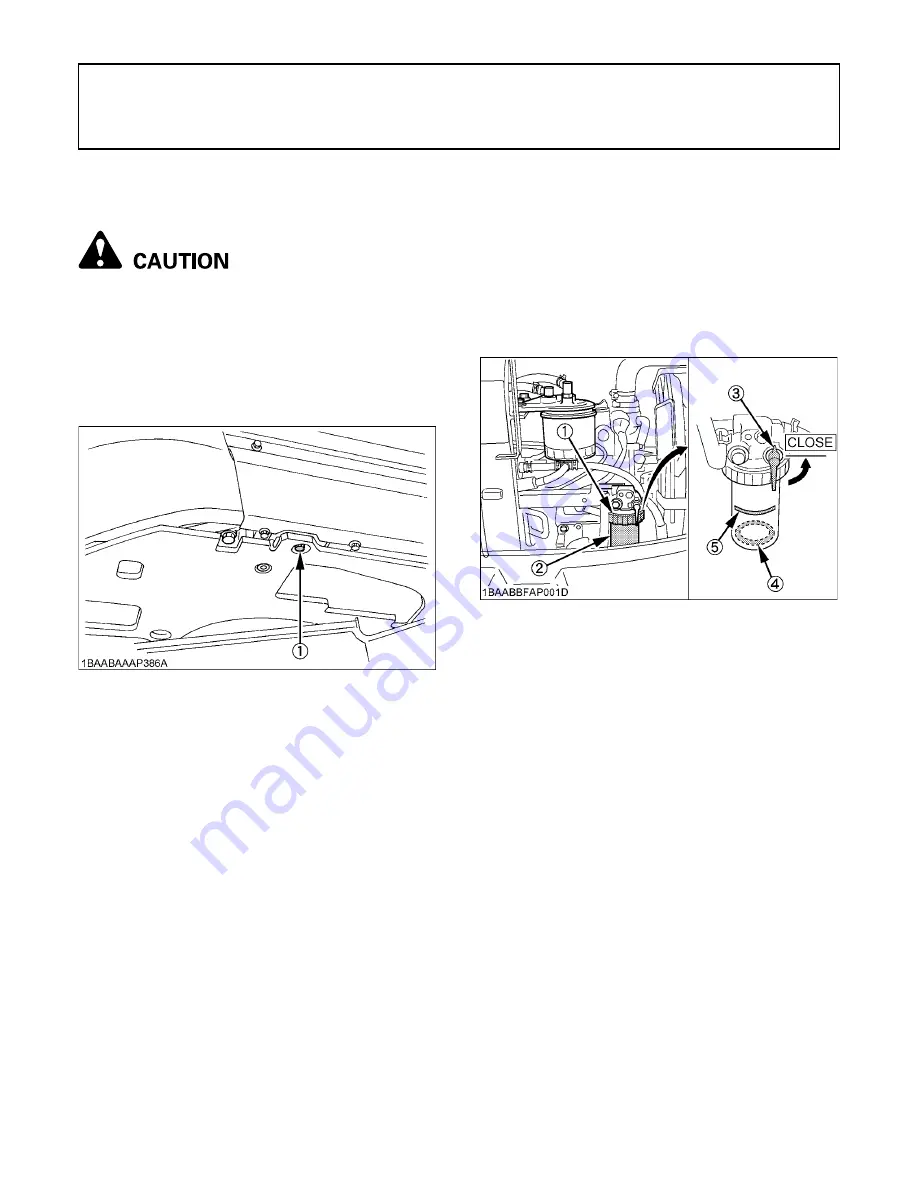
41
REGULAR CHECKS AND MAINTENANCE WORK
REGULAR CHECKS AND MAINTENANCE WORK
EVERY 50 SERVICE HOURS
B
Draining the Water from the Fuel Tank
To avoid personal injury:
A
Before draining the water from the fuel tank, be
sure to stop the engine and remove the key.
A
Do not smoke during inspection.
1. Remove the drain plug on the underside of the body
and drain water.
2. Re-tighten the drain plug.
B
Draining Water Separator
1. Open the hood.
2. When the separated water is being drained, the red
float moves upwards.
When the float reaches the line, close the shutoff-
valve so that no fuel can run out. Now loosen the ring
nut, and remove the cup and empty completely.
3. Finally, do not forget to open the shutoff-valve and
close the hood.
(1) Drain plug
(1) Ring nut
(2) Cup
(3) Shutoff-valve
(4) Float
(5) Line
Summary of Contents for u25
Page 8: ......
Page 15: ... 7 SAFE OPERATION ...
Page 16: ...SAFE OPERATION 8 ...
Page 17: ... 9 SAFE OPERATION ...
Page 18: ...SAFE OPERATION 10 ...
Page 20: ......
Page 90: ...70 LIFTING CAPACITY ...