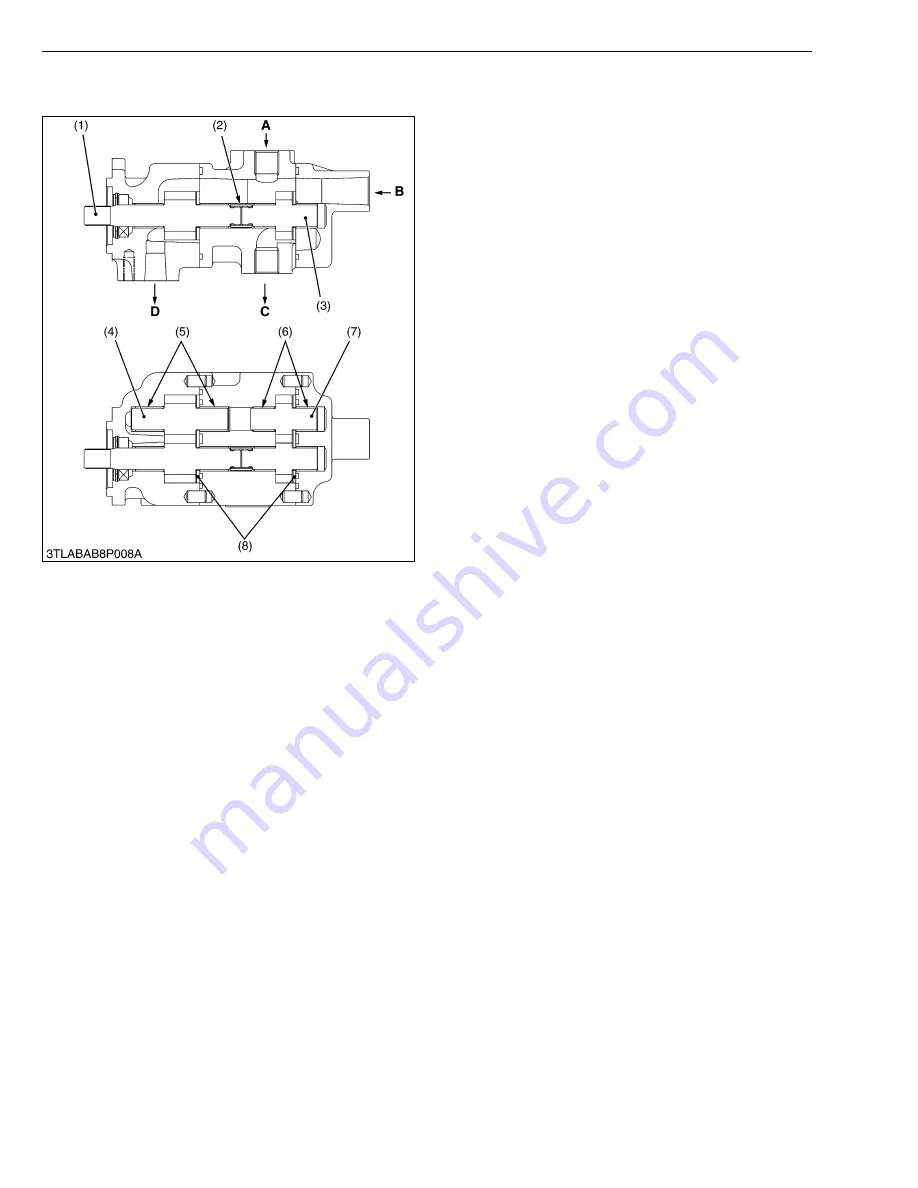
8-M6
L3540, L4240, L5040, L5240, L5740, WSM
HYDRAULIC SYSTEM
3. HYDRAULIC PUMP
The gear type hydraulic pump is adopted for these
tractor. This pump is tandem type and it is composed
two pair of gears, side plates, bushings and other
components as shown in the figure.
The hydraulic pump pressure-fed the oil drawn from
the transmission case through oil filter to power steering
circuit and main hydraulic circuit.
W1013488
(1) Drive Gear 1
(2) Coupling
(3) Drive Gear 2
(4) Driven Gear 1
(5) Bushing
(6) Bushing
(7) Driven Gear 2
(8) Side Plate
A : From Power Steering
Controller
B : From Transmission Case
C : To Power Steering
Controller
D : To Main Hydraulic Circuit
KiSC issued 04, 2010 A
Summary of Contents for L3540
Page 1: ...L3540 L4240 L5040 L5240 L5740 WORKSHOP MANUAL TRACTOR KiSC issued 04 2010 A ...
Page 8: ...6 L3540 L4240 L5040 L5240 L5740 WSM SAFETY INSTRUCTIONS KiSC issued 04 2010 A ...
Page 9: ...7 L3540 L4240 L5040 L5240 L5740 WSM SAFETY INSTRUCTIONS KiSC issued 04 2010 A ...
Page 21: ...G GENERAL KiSC issued 04 2010 A ...
Page 95: ...1 ENGINE KiSC issued 04 2010 A ...
Page 176: ...2 CLUTCH KiSC issued 04 2010 A ...
Page 177: ...CONTENTS MECHANISM 1 FEATURE 2 M1 KiSC issued 04 2010 A ...
Page 189: ...3 TRANSMISSION KiSC issued 04 2010 A ...
Page 363: ...4 REAR AXLE KiSC issued 04 2010 A ...
Page 364: ...CONTENTS MECHANISM 1 STRUCTURE 4 M1 KiSC issued 04 2010 A ...
Page 374: ...5 BRAKES KiSC issued 04 2010 A ...
Page 375: ...CONTENTS MECHANISM 1 STRUCTURE 5 M1 2 OPERATION 5 M2 KiSC issued 04 2010 A ...
Page 390: ...6 FRONT AXLE KiSC issued 04 2010 A ...
Page 391: ...CONTENTS MECHANISM 1 STRUCTURE 6 M1 KiSC issued 04 2010 A ...
Page 417: ...7 STEERING KiSC issued 04 2010 A ...
Page 434: ...8 HYDRAULIC SYSTEM KiSC issued 04 2010 A ...
Page 488: ...9 ELECTRICAL SYSTEM KiSC issued 04 2010 A ...
Page 604: ...10 CABIN KiSC issued 04 2010 A ...