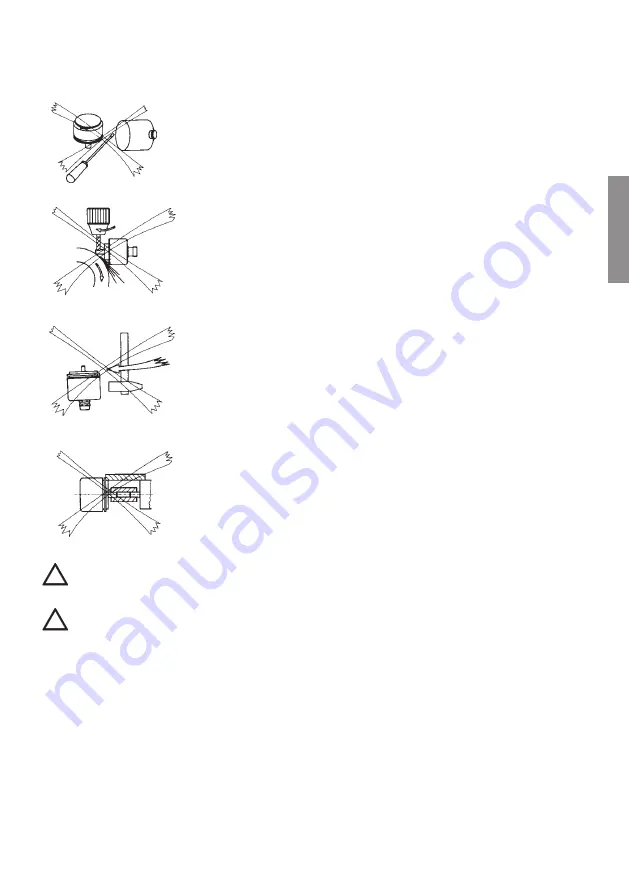
english
6. Mechanical installation of the encoder
6.1 General mounting information
The encoder must not be disassembled or modified, either in total or in
part.
No subsequent machining should be carried out on the shaft (grinding,
sawing, drilling, etc.). This would impair the accuracy of the encoder and
damage the bearings and shaft seals. We will be happy to accommodate
your wishes.
Never try to align the encoder using a hammer and never subject the en-
coder to impact shocks. - Do not subject the encoder shaft to loads (axial
or radial) that are higher than the values given in the data sheet.
Do not rigidly connect the shafts and flanges of the encoder and driving
device. Always use a coupling (between the drive shaft and the encoder
shaft, or between the flange of the hollow shaft encoder and the flange of
the drive).
Couplings are to be designed and dimensioned, so that they meet the requirements of
EN ISO 13849 or so that any possible breakage of the connection can be ruled out.
Depending on the specific use, the stator coupling/torque stop is subject to reduced wear.
Please refer to chapter “Maintenance and Servicing”.
Unless otherwise specified, a friction coefficient of 0.14 is assumed for all screw connections.
Unless otherwise specified, a strength class of 8.8 is assumed for the screws.
The encoder cable must be routed free from any traction, so that no additional torque is applied
to the encoder. The minimum bending radii of the cable are to be complied with.
For the assembly, use only inspected/calibrated tooling that is subject to the quality system.
!
!
Buy: www.ValinOnline.com | Phone 844-385-3099 | Email: [email protected]