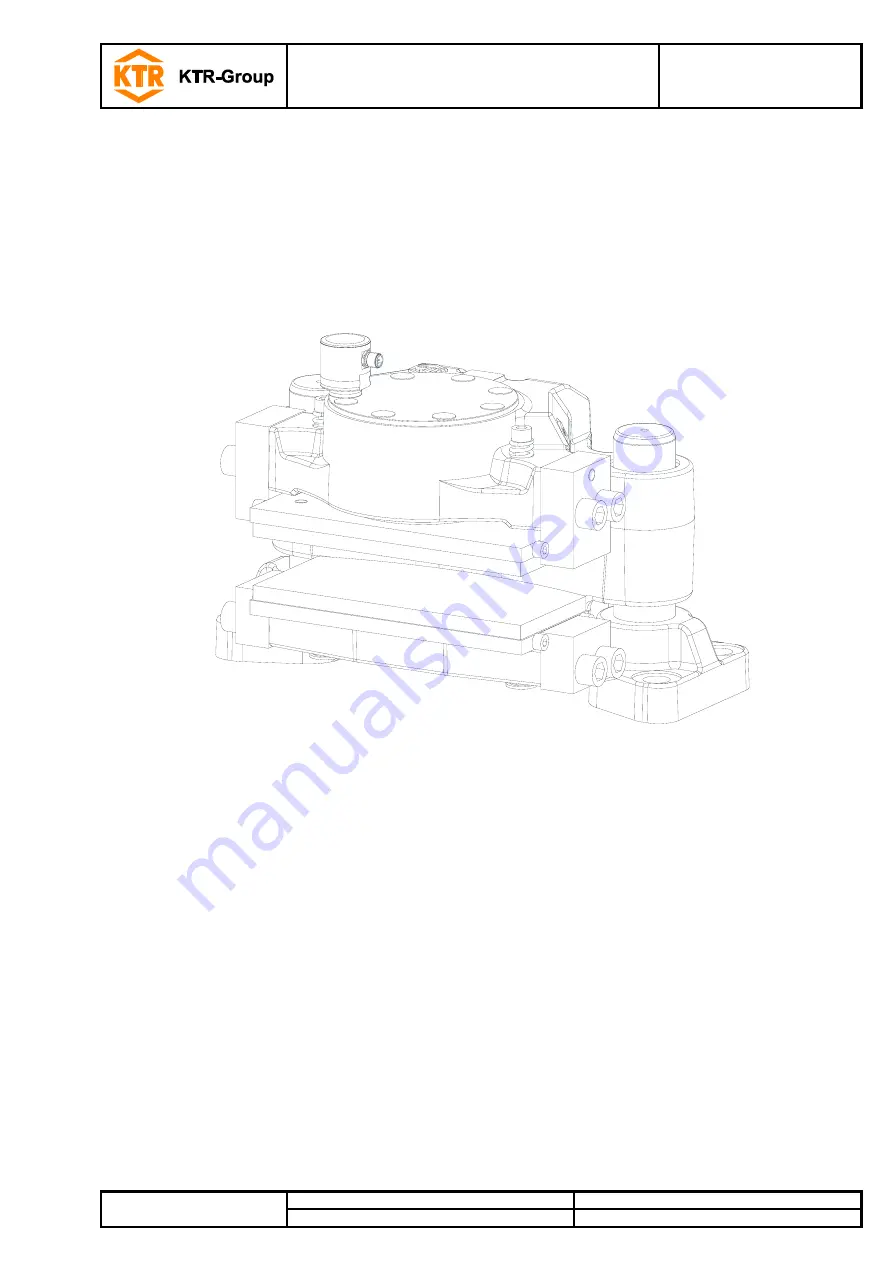
KTR-STOP
®
S-A-F B-xx
Operating/Assembly instructions
KTR-N
Sheet:
Edition:
44591 EN
1 of 24
5
Please observe protection
note ISO 16016.
Drawn:
2019-08-13 Pz/Mro
Replacing:
KTR-N dated 2018-12-04
Verified:
2019-08-13 Pz
Replaced by:
KTR-STOP
®
S-A-F B-xx
S-A-F B-xx is a brake actuated hydraulically in a floating caliper design serving to
generate a brake force on a brake disk in order to decelerate a machine's
movement or stop it, respectively, or keep it at standstill.