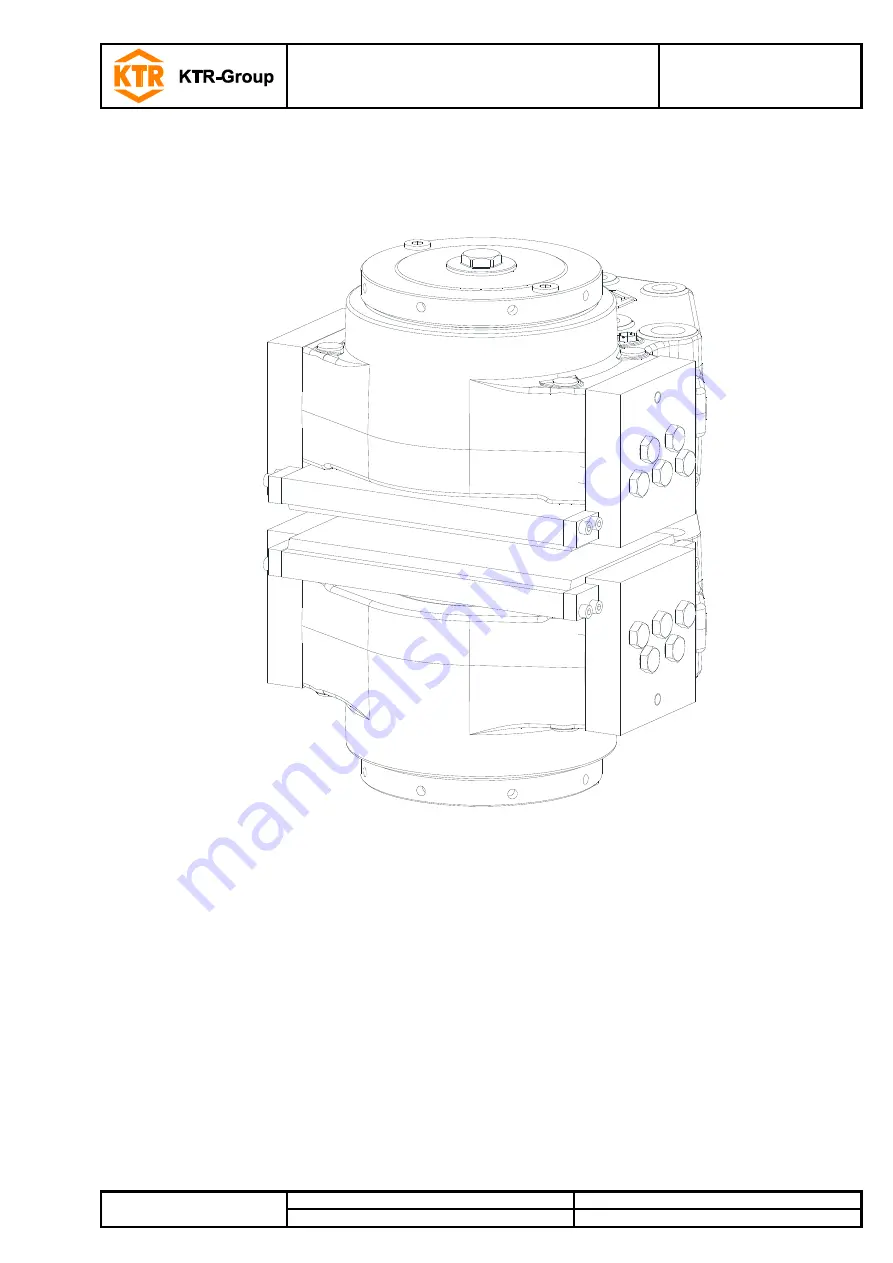
KTR-STOP
®
L light-xxx A-xx-xx
Operating/Assembly instructions
KTR-N
Sheet:
Edition:
445123 EN
1 of 21
2
Please observe protection
note ISO 16016.
Drawn:
2020-09-25 Shg/Wie
Replacing:
KTR-N dated 2019-11-21
Verified:
2020-11-05 Shg
Replaced by:
KTR-STOP
®
L light-xxx A-xx-xx
L light-xxx A-xx-xx is a spring-actuated brake in a fixed calliper design serving to
generate a brake force onto a brake disk in order to decelerate a plant’s move-
ment or stop it, respectively, or keep it at standstill.