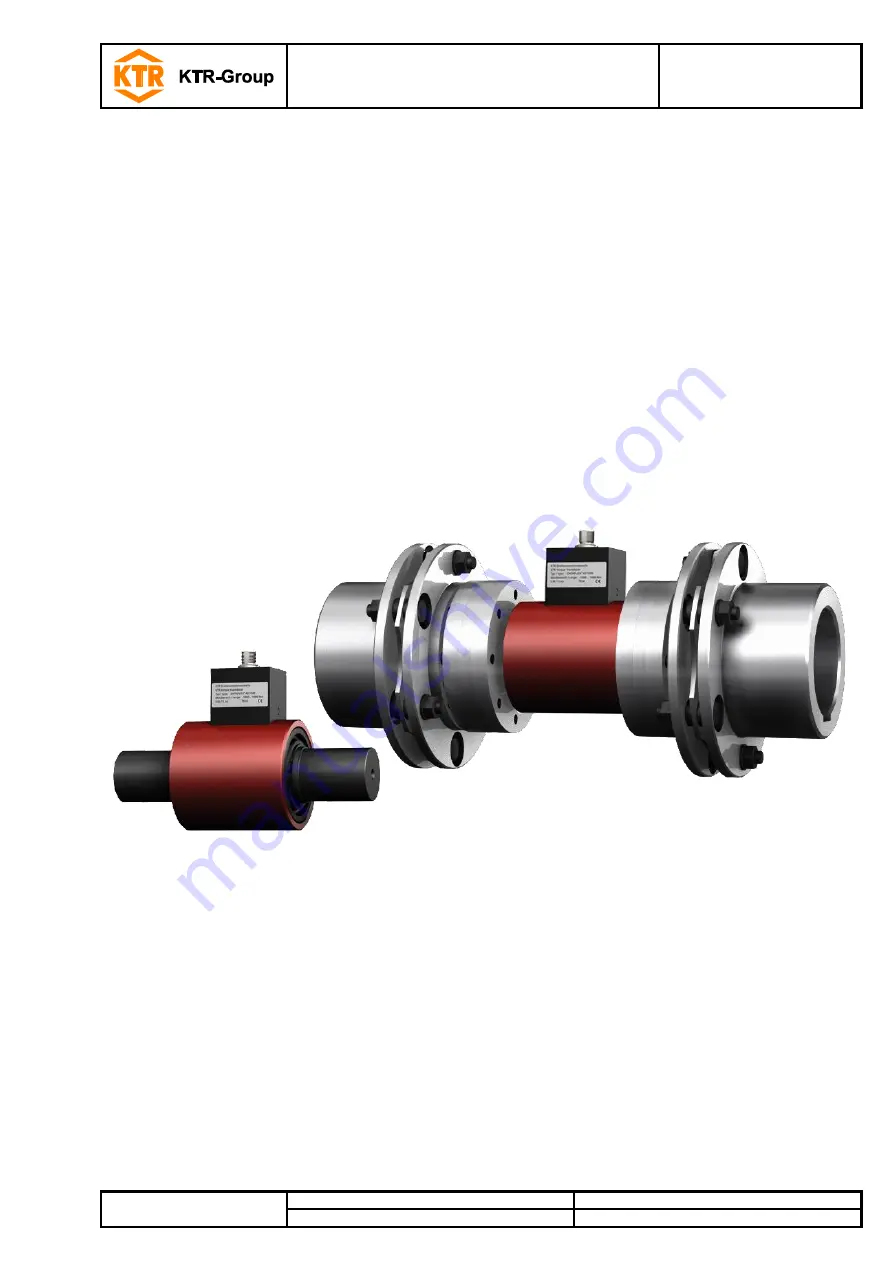
DATAFLEX
®
42/1000
Torque Measuring Shaft
Operating/Assembly instructions
KTR-N
Sheet:
Edition:
49016 EN
1 of 21
2
Please observe protection
note ISO 16016.
Drawn:
2017-01-02 Shg/Koe
Replaced for:
KTR-N dated 2015-04-13
Verified:
2017-01-02 Shg
Replaced by:
DATAFLEX
®
Torque measuring shaft type 42/1000