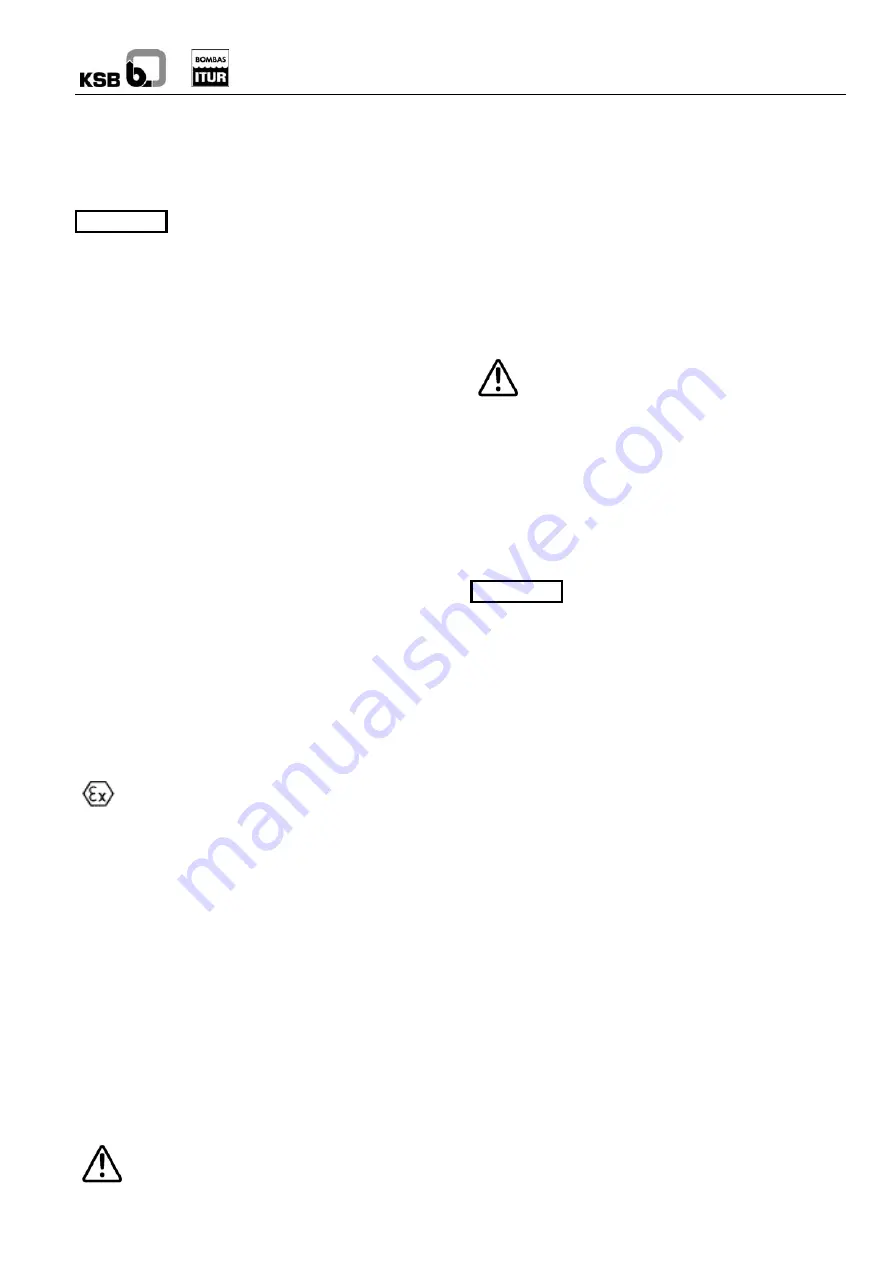
RWCP, RWCN
7
5 Installation
The electropump is dispatched totally mounted and prepared
for installation and operation (except for the few cases of the
motor being dispatched disassembled, as is the case of large,
heavy motors).
The design of the pipe systems, anchorings
and other installation areas corresponds to
other parties. KSB ITUR only offers details and comments as
a help, but does not assume any responsibility with regards to
the design, assembly and operation of any installation. We
recommend that customers check with a specialist in the
design of castings, pipes, wells, etc in order to interpret and
supplement the information given by KSB ITUR and to ensure
correct operation.
5.1
Check before assembly
Before positioning, check that the assembly base is in line with
the dimensional plan of the equipment.
The upper surface of the base must be horizontal and flat.
If the anchor pins are to be placed in existing holes, place the
anchor pins in their orifices suspended from the pump.
Do not connect the suction and impulsion nozzles until the
equipment is completely installed on its base.
5.2 Group
positioning
5.2.1 Vertical
groups
Levelling
Use a spirit level to level the equipment. Use wedges to alter
the height at different points. The maximum deviation
permitted is 0.2 mm/m.
The correct separation between the two coupling halves must
be maintained.
Pump - motor alignment
In order to prevent misalignment between the shafts, it is
necessary to correctly install, check and maintain the coupling.
See the instructions manual for the coupling.
The coupling may produce a source of ignition or high
temperature in the event of incorrect operation. The
coupling must be classified as non-electric equipment with at
least the same type of area and temperature as the pump. It is
necessary to follow the instructions in the coupling manual
which is included with the pump.
The equipment is aligned at factory, and this alignment will
never be be lost. In case of dismantling of the motor and when
mounting it again following instructions must be followed:
- Check that the flange support surface of the motor
support and of the motor itself are perfectly clean and
smooth.
- Check the correct separation between the two halves of
the coupling.
- Check that the alignment between both shafts is correct
by turning the equipment by hand.
5.3 Pipe
joint
In no case can the pump be used as a fixed point for the
pipes.
The pipe system must at no time exercise force in
excess of the values shown in the chart in point4.4
(due to connection, thermal variation, etc) in the pump.
The short pipes must be of at least the diameter of the pump
connections. The diameter of long pipes is, in some cases,
determined by economic criteria.
Transition pieces at larger diameters must have an extension
angle of around 8°, in order to prevent pressure drops.
Note
The thermal expansions of the pipes must be offset with
suitable measurements, in order not to exceed the maximum
strains permitted on the pump.
The diameters of the pipes, valves and accessories must be
calculated in line with the load losses envisaged in the
installation, so that the fluid impulsion speeds in the pipes will
be from 2 to 3 m/s
Exceeding the admitted strains of the pipes may lead
to leaks in the pump and to the fluid escaping.
Hazard of death with hot liquids!
When designing the suction piping check that the available
NPSH is higher than required NPSH of the pump in order to
avoid cavitation in whole admissible operation range.
The suction and impulsion mouth covers of the pump must be
removed before connecting the pipes.
Before starting up a new installation, it is necessary to
thoroughly clean the tanks, pipes and accessories by brushing
and blowing. Welding material, scales and other impurities are
often cast off some time after.
In order to prevent the rotation of the pumps
in inverse direction (danger of the impeller
breaking out), a retention valve must be placed in the
impulsion pipe.
Note
Wet well. Suction conditions
It is not enough to simply submerge the pump in the well to
make it primed. We need to pay attention to the suction of the
pump, since in this case good suction will depend more on the
environment surrounding the pump (physical conditions of the
well or sump) than on the pump itself.
An insufficient liquid submergence level may lead to dry
operation of the parts of the pump, which in turn leads to the
heating of the parts in contact. This circumstance should be
avoided, with plant operators manually checking or equipment
stop devices ensuring that the liquid level in the suction well is
never lower than the indicated submergence level.
High suction pressure may overload the bearings and lead to
their overheating. This circumstance must be avoided, to
which end the suction pressure must not exceed that shown in
the datasheets, either through manual control by the operators
or through devices which stop the equipment in the event of
excessive pressure.
The pump must not work without liquid under any
circumstance. If this condition may come about, the
installation must be fitted with safety devices which prevent
the operation of the pump without liquid inside, or have
automatic devices to discharge the minimum flow of the pump.
See the section on minimum flow.
As a general rule we can make some observations:
- The minimum liquid level in the well must be at the
distance indicated in the table in annex 0 save for the
particular pump plans or datasheets showing higher or
lower values for minimum submergence.
-
The input of liquid to the well must be carried out gently,
without any fluctuation or turbulence which may harm the