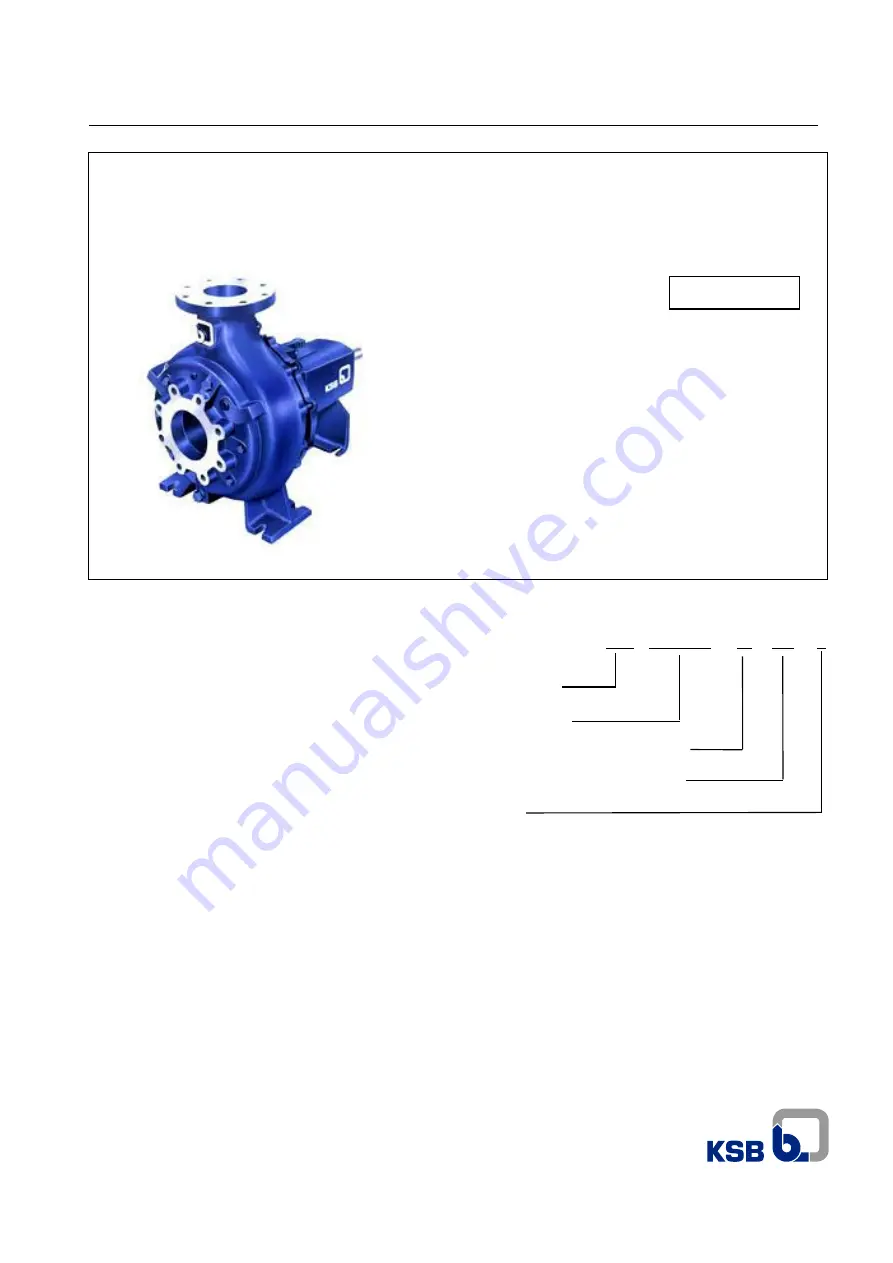
Operating Instructions Manual
NºA2370.8E/2
KSB MEGAFLOW
Pumps for Sewage, Effluents and Mixtures
1. Application
The
KSB
MEGAFLOW
centrifugal
pump
is
recommended for industrial and municipal waste water,
as well as all kinds of pulps not liable to plait, sewage
water, chemical effluents.
-
Municipal and industrial waste-water treatment
-
Drainage
-
Pulp and paper
-
Food processing
-
Sugar and alcohol
-
Mining and manufacturing
-
Civil construction
2. Design
Horizontal, single-stage, simple horizontal suction and
vertical upwards discharge. The “back-pull-out” design
allows maintenance and repair services through the back
side, without dismantling piping and alignment.
The available hydraulics and impeller types allow proper
selection for the handled liquid and required application.
3. Designation
KSB
Megaflow
50
-
160
K
Trade Mark
Model / Type
Discharge Nozzle Diameter (mm)
Nominal Impeller Diameter (mm)
Rotor
4. Operating Data
Sizes
- DN 50 up to 350
(2 ½” to 14” )
Flow
- to 11,000 gpm
(2,500 m
3
/h)
Head
- to 328 ft (100m)
Temperature
- to 221
º
F (105
º
C)
Max. Suction pressure
- to 43 psi (3 bar)
Speed
- to 3,500 rpm
LINE:
Mega
Summary of Contents for MEGAFLOW 100-250
Page 33: ...KSB Megaflow 33 17 3 Execution with K Impeller AK Bearing Bracket Figure 26 ...
Page 34: ...KSB Megaflow 34 17 4 Execution with O Impeller AK Bearing Bracket Figure 27 ...
Page 36: ...KSB Megaflow 36 17 6 Execution with Impeller K O Bearing Bracket P65 160 Figure 27 ...
Page 38: ...KSB Megaflow 38 17 8 Execution with Impeller K and Bearing Bracket P80 200S Figure 28 ...
Page 40: ...KSB Megaflow 40 17 10 Execution with Impeller E Bearing Bracket AK Figure 29 ...
Page 42: ...KSB Megaflow 42 17 12 Execution with Impeller E and Bearing Bracket P65 160X Figure 30 ...