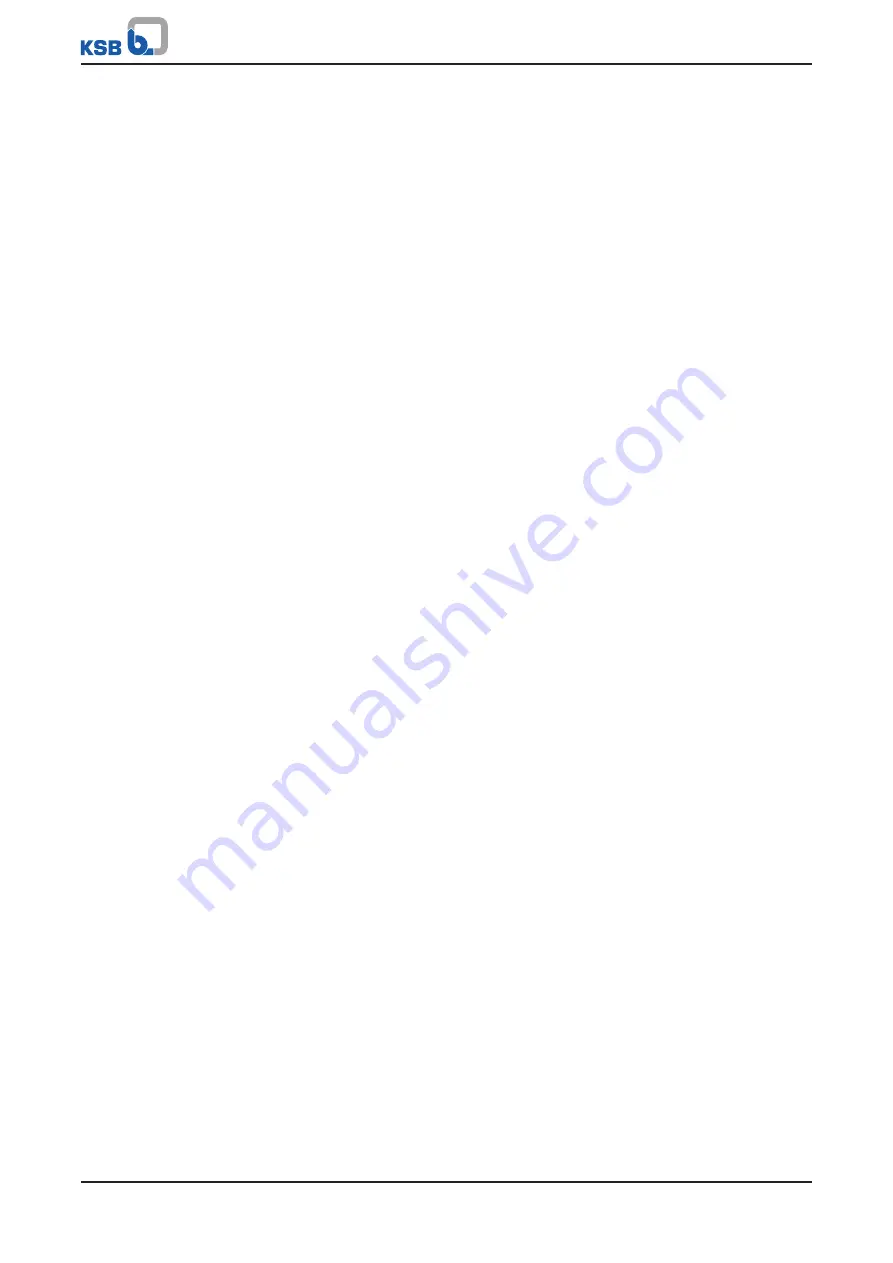
1 Supplementary Operating Manual
8 of 12
Double Mechanical Seals
Large-scale industrial plants
Barrier fluid
▪
Ultrafiltrate (residual solvent content approx. 50% of the solvent in the paint)
▪
Return barrier fluid to ultrafiltration stage.
Monitor the ultrafiltrate for contamination (clouding). In the event of a
malfunction make sure the ultrafiltrate does not reach the barrier fluid vessel.
Barrier fluid pressure
▪
Install a pressure boosting pump to ensure the barrier fluid pressure required.
▪
Fit a by-pass valve in the return line, for instance, to maintain the minimum
pressure. This valve must close tightly during idle periods and be used in
conjunction with a sufficiently sized bladder accumulator to maintain the
pressure in the system (e.g. in the event of a power failure or operating errors).
▪
To ensure equal distribution of the barrier fluid, install orifice plates in the lines
downstream of the mechanical seals. Use downstream valves for fine-tuning only.
▪
Secure the barrier fluid system against barrier pressure failure (e.g. due to power
failure), as the absence of barrier pressure will result in mechanical seal failure.
Barrier fluid temperature
▪
The temperature of the barrier fluid should be within the processing range of
the paint (normally 25 to +30 °C).
Circulation flow
▪
To prevent the formation of paint deposits in the seal supply system and to
stabilise the temperature in the sealing gap, we recommend a circulation flow of
2.5 - 5 l/min per seal.
Small systems
Barrier fluid
▪
Ultrafiltrate
▪
DI water with a slightly increased solvent content, e.g. 5 – 10 % butyl glycol
Barrier fluid pressure
Ensure sufficient barrier fluid pressure by means of a continuous nitrogen supply or
compressed air supply via a suitable pressure regulating valve.
Thermosyphon system
▪
The thermosyphon vessel should be located approximately 1 metre above the
centreline of the pump and connected with pipework.
▪
Install pipes made of chrome nickel molybdenum cast steel with an inside
diameter ≥ 9 mm and a steady rise, in order to avoid air pockets and consequent
dry running of the mechanical seals.
▪
Each pump must be provided with its own thermosyphon system so that the
mechanical seals can be monitored individually and failure of one mechanical
seal will not pose a risk to the others.
▪
The pipe bend radius must be as large as possible to keep pipe friction losses as
low as possible.
▪
In order to stabilise the temperature, a circulating pump must be installed in the
system. (Contact operator about explosion protection requirements.)
▪
Monitor the barrier fluid level by means of a level switch (contact operator about
explosion protection requirements).
▪
Barrier fluid refill is by means of a manual refill pump.
▪
When a closed thermosyphon system is used, we recommend to use a SiC/SiC
combination on the outboard mechanical seal as well, to avoid wear or damage
to the seal faces caused by paint deposits or sticking.
Cooling
Cooling of the thermosyphon system is required if the following limits are exceeded:
▪
Speeds > 1450 rpm
▪
Seal diameter > 60 mm
▪
Barrier fluid pressure > 6 bar
▪
Ambient temperature > 30
℃