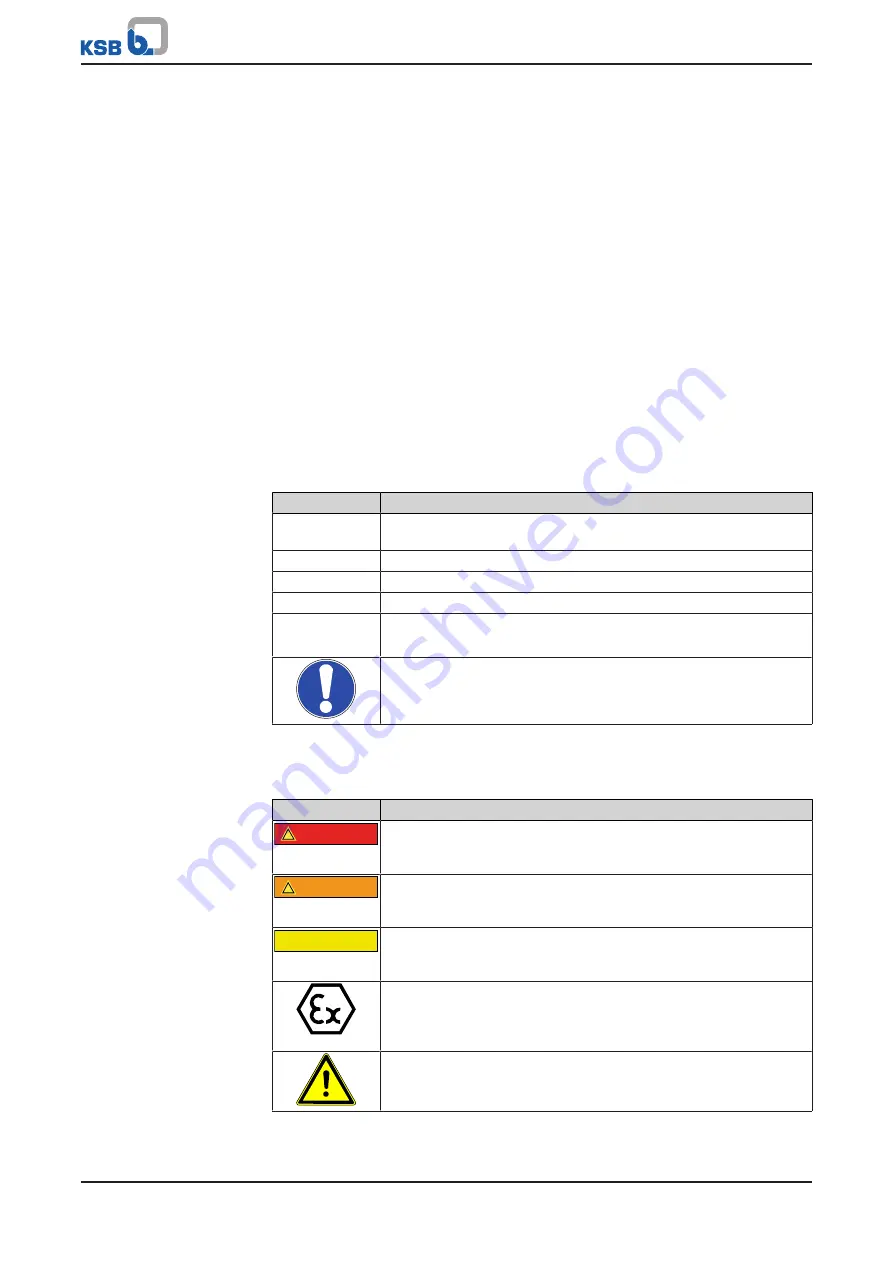
1 General
5 of 54
EMV
7138.82/01-EN
1 General
1.1 Principles
This operating manual is valid for the type series and variants indicated on the front
cover.
The operating manual describes the proper and safe use of this equipment in all
phases of operation.
The name plate indicates the type series and size as well as the main operating data
and the serial number. The serial number uniquely describes the product and is used
as identification in all further business processes.
In the event of damage, immediately contact your nearest KSB service facility to
maintain the right to claim under warranty.
1.2 Target group
This operating manual is aimed at the target group of trained and qualified specialist
technical personnel.
1.3 Symbols
Table 1:
Symbols used in this manual
Symbol
Description
✓
Conditions which need to be fulfilled before proceeding with the
step-by-step instructions
⊳
Safety instructions
⇨
Result of an action
⇨
Cross-references
1.
2.
Step-by-step instructions
Note
Recommendations and important information on how to handle
the product
1.4 Key to safety symbols/markings
Table 2:
Definition of safety symbols/markings
Symbol
Description
!
DANGER
DANGER
This signal word indicates a high-risk hazard which, if not avoided,
will result in death or serious injury.
!
WARNING
WARNING
This signal word indicates a medium-risk hazard which, if not
avoided, could result in death or serious injury.
CAUTION
CAUTION
This signal word indicates a hazard which, if not avoided, could
result in damage to the machine and its functions.
Explosion protection
This symbol identifies information about avoiding explosions in
potentially explosive atmospheres in accordance with EU Directive
2014/34/EU (ATEX).
General hazard
In conjunction with one of the signal words this symbol indicates a
hazard which will or could result in death or serious injury.
Summary of Contents for EMV Series
Page 1: ...Control Valve Actuators EMV For the BOA Control PIC Type Series Installation Operating Manual ...
Page 52: ......
Page 53: ......