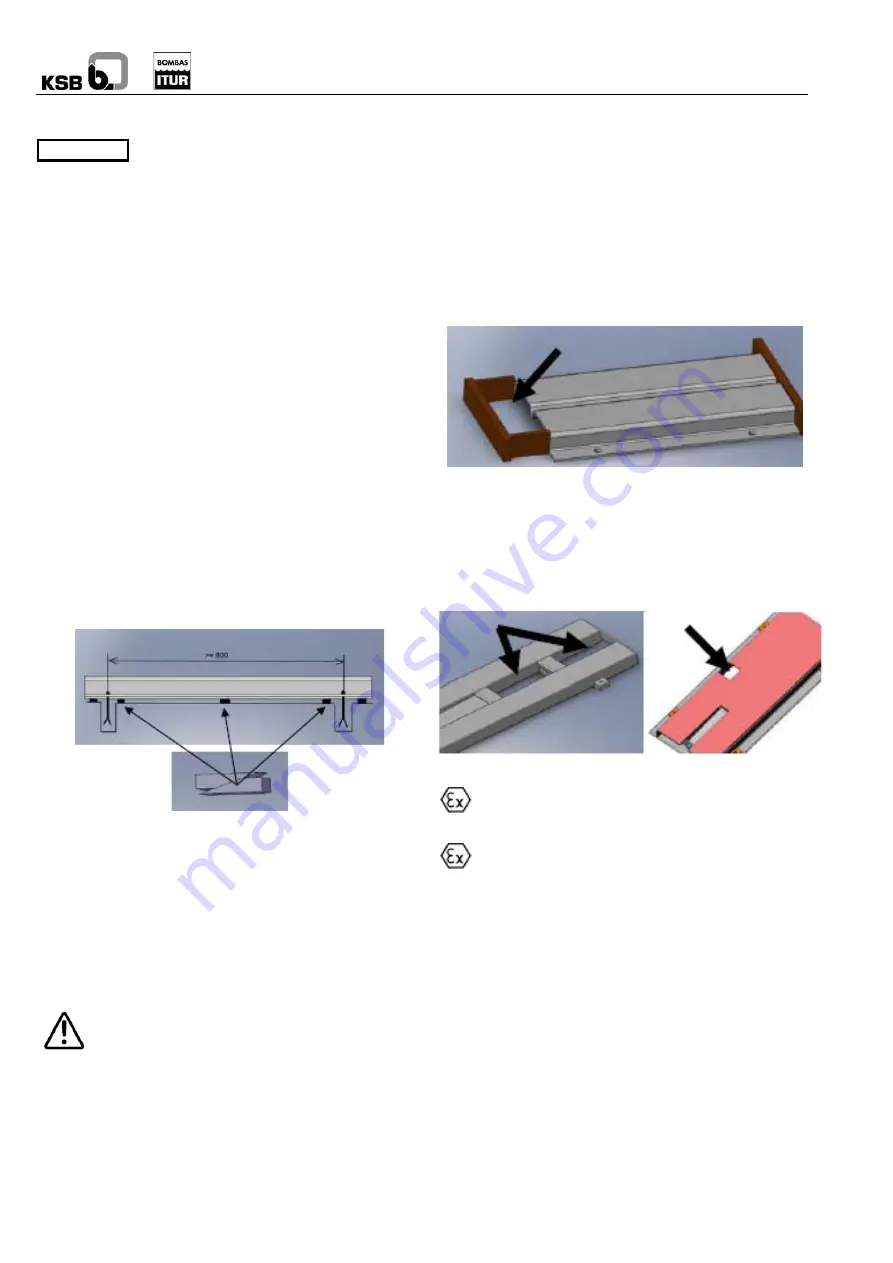
AU
6
5 Installation
The design of the pipe systems, anchorings
and other installation areas corresponds to
other parties. KSB ITUR only offers details and comments as
a help, but does not assume any responsibility with regards to
the design, assembly and operation of any installation. We
recommend that customers should check with a specialist in
the design of castings, pipes, wells, etc, to supplement and
interpret the information provided by KSB ITUR and to ensure
proper operation.
5.1
Check before assembly
Before positioning, check that the assembly base is in line with
the dimensional plan of the equipment.
The slab upon which the equipment is to be positioned must
have completely set.
The concrete used must be of sufficient resistance (minimum
X0) to allow functional assembly in line with DIN-1045.
The upper surface of the base must be horizontal and flat.
If the anchor pins are to be placed in existing holes, place the
anchor pins in their orifices suspended from the pump.
Do not connect the suction and impulsion nozzles until the
equipment is completely installed on its base and the cement
has completely set.
5.2 Group
positioning
5.2.1
Groups with horizontal base frame
Levelling
Place wedges on both sides of the anchor pins if the base
frame does not include levelling screws.
When the distance between anchor pins is over 800 mm, use
levelling wedges in the middle, both on the sides and at the
front.
Use a spirit level to level the equipment. Use wedges to alter
the height at different points. The maximum deviation
permitted is 0.2 mm/m.
The separation between the two coupling halves must be
maintained.
All equipment supplied on a transport bench (forklift
truck, carriage, etc) should be secured using the
envisaged attachment device or brake. Ask KSB
ITUR for the specific instructions manual for your transport
bench if you do not have one already. (See annex 9.20)
Cementing
Pour an initial layer of mortar cement into the orifices of the
bolts, contacting throughout the periphery with the base of the
base frame. Once the mortar cement has set, tighten the
anchor pins in a balanced manner.
Note
Connect the suction and impulsion nozzles to the installation
and proceed with an initial alignment of the equipment.
Proceed to fill the lower part, or the cavities between the base
frame profiles, with concrete.
When using folded steel base frames, make a small mould in
the front and rear part.
The concrete must be of minimum contraction, normal
granulometry, with a water/cement ratio (W/C Ratio) of
≤
0.5. It
is necessary to use additives which improve fluidity for correct
filling.
We recommend treating the concrete in line with DIN-1045.
In order to carry out the final alignment, wait until the
installation is ready and at operation temperature.
Pump-motor alignment
In order to prevent misalignment between the axes, it
is necessary to correctly install, check and maintain
the coupling. See the instructions manual for the coupling.
The coupling may produce a source of ignition or high
temperature in the event of incorrect operation. The
coupling must be classified as non-electric equipment with at
least the same type of area and temperature as the pump. It is
necessary to follow the instructions in the coupling manual
which is included with the pump.
When the supply includes the complete group (pump – motor),
the equipment has been aligned at factory, although, due to
transport and to the anchoring to the casting, the equipment
should be realigned before proceeding with start-up.
The correct alignment of the standard KSB ITUR coupling
involves correcting any possible errors of parallelism and
concentricity using metal wedges in the motor.
Use appropriate instruments to carry out the following
measurements in 4 positions offset 90º between the faces of
the coupling: