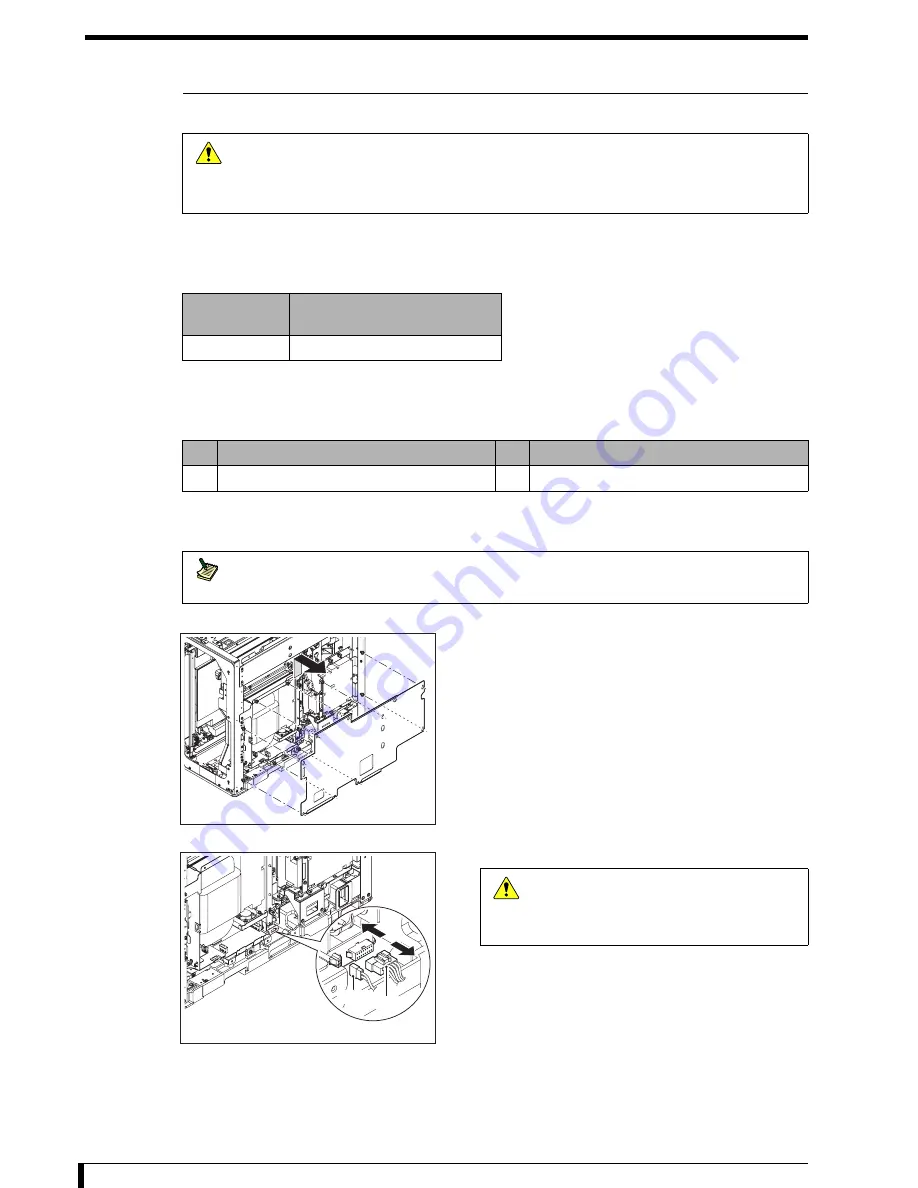
Chapter 5 Disassembly and Assembly
5-74
5.5.5 Replacing the Cable Bear
This section describes the instructions on how to replace the cable bear.
Work outline
Listed below are the number of people and the rough standard of work hours required for performing the
works described in this section.
Requirements
Shown below are the tools requiring to be prepared in addition to the standard tools before performing the
works in this section.
1
Removal Procedures (Page 5-6)"
"5.2.3 Removing/Installing the Exterior Panel and
to remove the exterior panel and insertion unit.
2
Remove the electric component mount panel.
•
8 hex/Phillips-head screws (M4 x 8)
Loosen all screws.
3
Remove the connectors (JP13, JJ14).
Caution
•
Be sure to turn off the power supply circuit breaker and unplug the power cable from the
equipment whenever you disassemble/assemble the equipment.
•
Be careful when handling the optical unit not to send a shock wave to it, that is composed
of precision parts.
Personnel
Number
Work Hours (steps 2 to 20)
1
No.
Tool
No.
Tool
1
Wiring band
2
Snap ties
Note
It is recommended the insertion unit be removed to let in light in order to work with the inner
part of the equipment, though the insertion unit can be replaced without removing it.
First Front Side
First Front Side
JP13 JJ14
Caution
When removing the connector, hold a notch
on the connector without pulling a cable.
Giving a strong pull to the cable may cause
it to be broken.
Summary of Contents for 0902
Page 2: ......
Page 6: ......
Page 12: ......
Page 30: ...2 10...
Page 54: ......
Page 84: ...Chapter 3 Troubleshooting 3 30 3 2 19 Confirm the H sync Signal To be stated...
Page 85: ...Chapter 3 Troubleshooting 3 31 3 2 20 Confirm the LMC Operation To be stated...
Page 120: ......
Page 296: ...8 10...
Page 300: ......
Page 301: ......