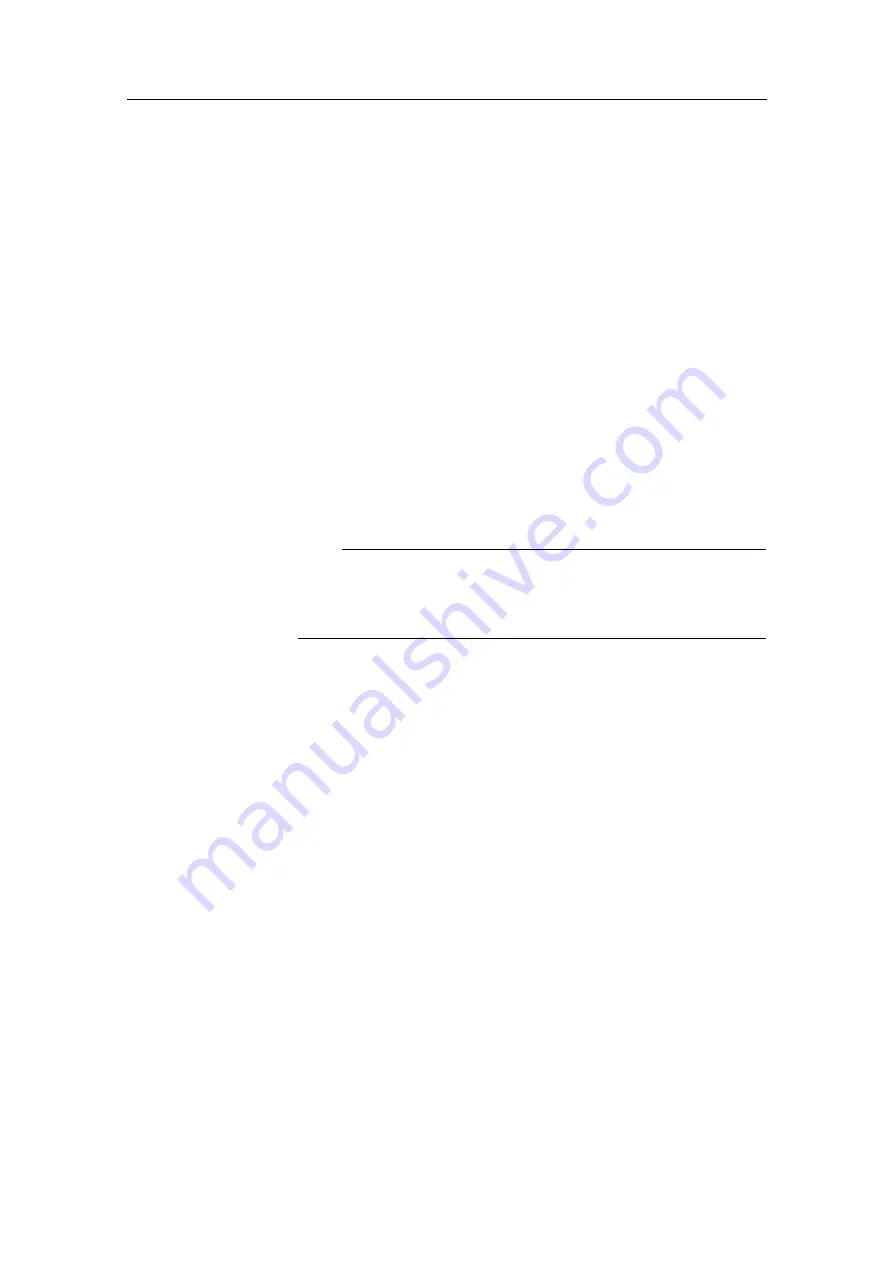
System test
9 SYSTEM TEST
Topics
•
on page 104
•
on page 106
•
on page 107
After the installation has been performed and before the EM 710
system is brought into operation for the first time, a series of test
procedures must be carried out to confirm a correct installation.
Some of the tests can be carried out on individual units once
that particular unit has been installed. However, in the interests
of safety and to avoid possible mistakes, it is recommended to
set aside a period of time at the end of the installation phase
specifically for the checks and tests. The entire set of tests can
then be performed in sequence to ensure the entire system is
comprehensively checked.
Note
If the test engineer is not satisfied with the quality of any part of
the installation, he/she must contact the customer to have the
work rectified and brought up to the required quality standards.
Which specific tests that are to be conducted are normally
specified in the contract. In most cases, the following tests are
performed
• Installation tests
– These tests are performed during the installation work. The
general procedures are given in this chapter. These tests
take place before power is applied to the system.
• Setting To Work (STW)
– This work is performed by the installation personnel from
Kongsberg Maritime. All specific hardware and software
units are checked, and the cabling is controlled.
• Harbour Acceptance Test (HAT)
– This test is performed by the installation personnel from
Kongsberg Maritime together with representatives from the
customer and in some cases the installation shipyard.
• Sea Acceptance Test (SAT)
– This test takes place with the vessel in open sea. It is
performed by the installation personnel from Kongsberg
Maritime together with representatives from the customer
and in some cases the installation shipyard. The purpose
of the test is to check the functional specifications of the
system during normal working conditions.
164851/C
103
Summary of Contents for EM 710
Page 1: ...Installation Manual EM 710 Multibeam echo sounder ...
Page 2: ......
Page 44: ...Kongsberg EM 710 Figure 10 Transducer mounting principles 42 164851 C ...
Page 63: ...Cable layout Figure 20 Transceiver Unit front view 0 5 x 1 degree 164851 C 61 ...
Page 88: ...Kongsberg EM 710 Figure 42 Cable clamp Transceiver Unit cable clamp on page 133 86 164851 C ...
Page 113: ...Installation drawings 164851 C 111 ...
Page 114: ...Kongsberg EM 710 10 1 2 1 mounting frame assembly RX module 112 164851 C ...
Page 115: ...Installation drawings 164851 C 113 ...
Page 116: ...Kongsberg EM 710 10 1 3 2 mounting frame assembly TX RX module 114 164851 C ...
Page 117: ...Installation drawings 164851 C 115 ...
Page 118: ...Kongsberg EM 710 10 1 4 0 5 x 1 gondola 116 164851 C ...
Page 119: ...Installation drawings 164851 C 117 ...
Page 120: ...Kongsberg EM 710 10 1 5 Transducer TX1 Outline dimensions 118 164851 C ...
Page 121: ...Installation drawings 164851 C 119 ...
Page 122: ...Kongsberg EM 710 10 1 6 Transducer TX2 Outline dimensions 120 164851 C ...
Page 123: ...Installation drawings 164851 C 121 ...
Page 124: ...Kongsberg EM 710 10 1 7 Transducer RX1 Outline dimensions 122 164851 C ...
Page 125: ...Installation drawings 164851 C 123 ...
Page 126: ...Kongsberg EM 710 10 1 8 Transducer RX2 Outline dimensions 124 164851 C ...
Page 127: ...Installation drawings 164851 C 125 ...
Page 128: ...Kongsberg EM 710 10 1 9 HWS Operator Station Outline dimensions 126 164851 C ...
Page 129: ...Installation drawings 10 1 10 Transceiver Unit Outline dimensions 164851 C 127 ...
Page 130: ...Kongsberg EM 710 128 164851 C ...
Page 132: ...Kongsberg EM 710 130 164851 C ...
Page 133: ...Installation drawings 10 1 12 Transceiver Unit mounting bracket 164851 C 131 ...
Page 134: ...Kongsberg EM 710 10 1 13 Junction Box outline dimensions 132 164851 C ...
Page 135: ...Installation drawings 10 1 14 Transceiver Unit cable clamp 164851 C 133 ...