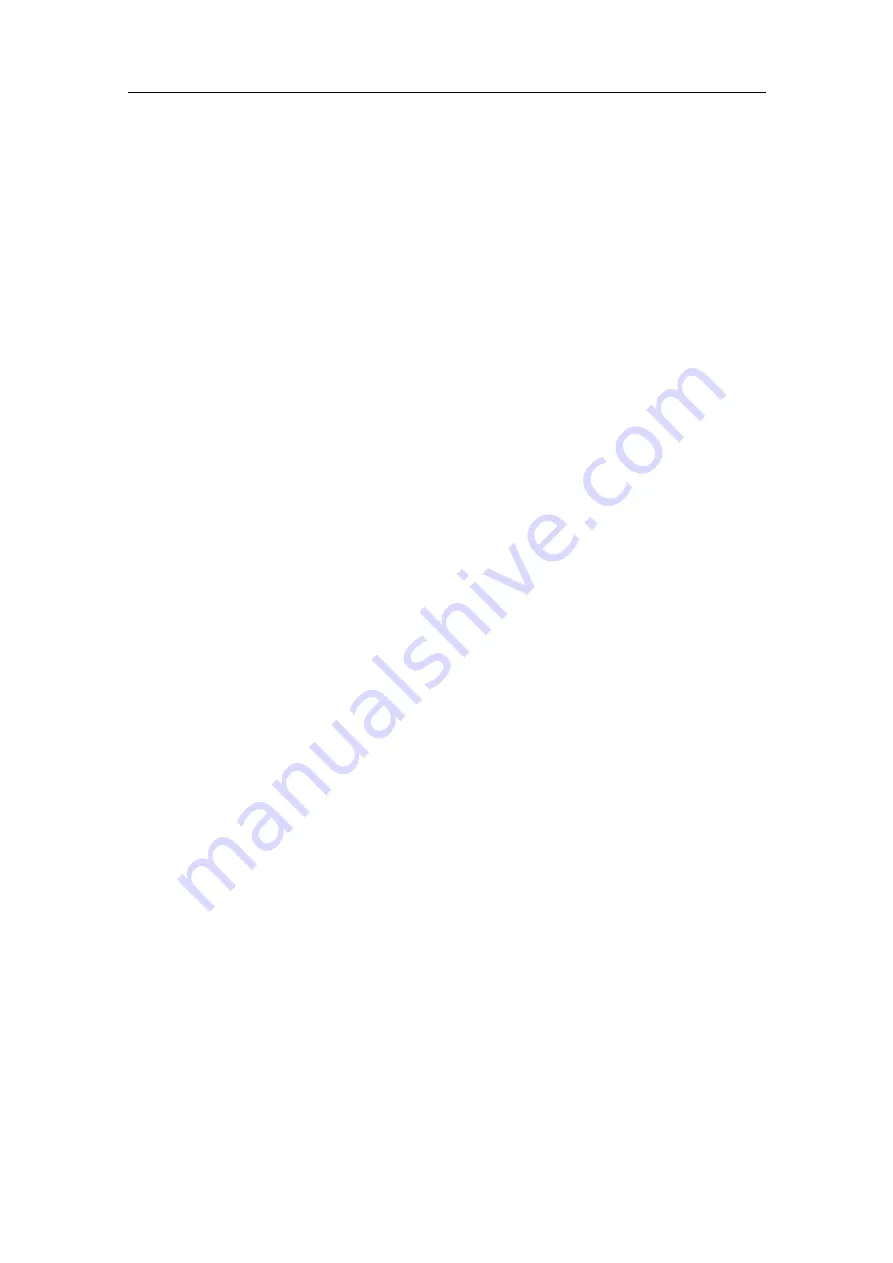
74
472405/A
Installing the Hydrographic Work Station
Follow this procedure to install the Hydrographic Work Station.
The Hydrographic Work Station is based on a commercial design. Due to the constant
development of new computer parts, older parts are no longer manufactured. This means
that the computer type used with the EM 2040 MKII system changes from time to time.
The Hydrographic Work Station is normally mounted near the operator work space.
Topics
Installing the HWS - MC330 - Rack model, page 75
Installing the HWS - MC330 - Desktop model, page 78
KONGSBERG EM 2040 MKII Installation Manual
Summary of Contents for EM 2040 MKII
Page 8: ...8 472405 A KONGSBERG EM 2040 MKII...
Page 92: ...92 472405 A Related topics List of cables page 101 KONGSBERG EM 2040 MKII Installation Manual...
Page 177: ...472405 A 177 338208 RX transducer outline dimensions 0 7 degrees Drawing file...
Page 179: ...472405 A 179 337805 TX transducer outline dimensions 0 4 degrees Drawing file...
Page 181: ...472405 A 181 355913 Transducer mounting plate 0 4 x 0 7 degrees Drawing file...
Page 182: ...182 472405 A 359252 Baffle plate 0 7 x 0 7 degrees KONGSBERG EM 2040 MKII Installation Manual...
Page 183: ...472405 A 183 385422 Processing Unit dimensions Drawing file...
Page 185: ...472405 A 185 464618 HWS dimensions MC330 Rack model Drawing file...
Page 187: ...472405 A 187 370275 Remote Control Unit K REM dimensions Drawing file...
Page 247: ......
Page 248: ...2021 Kongsberg Maritime...