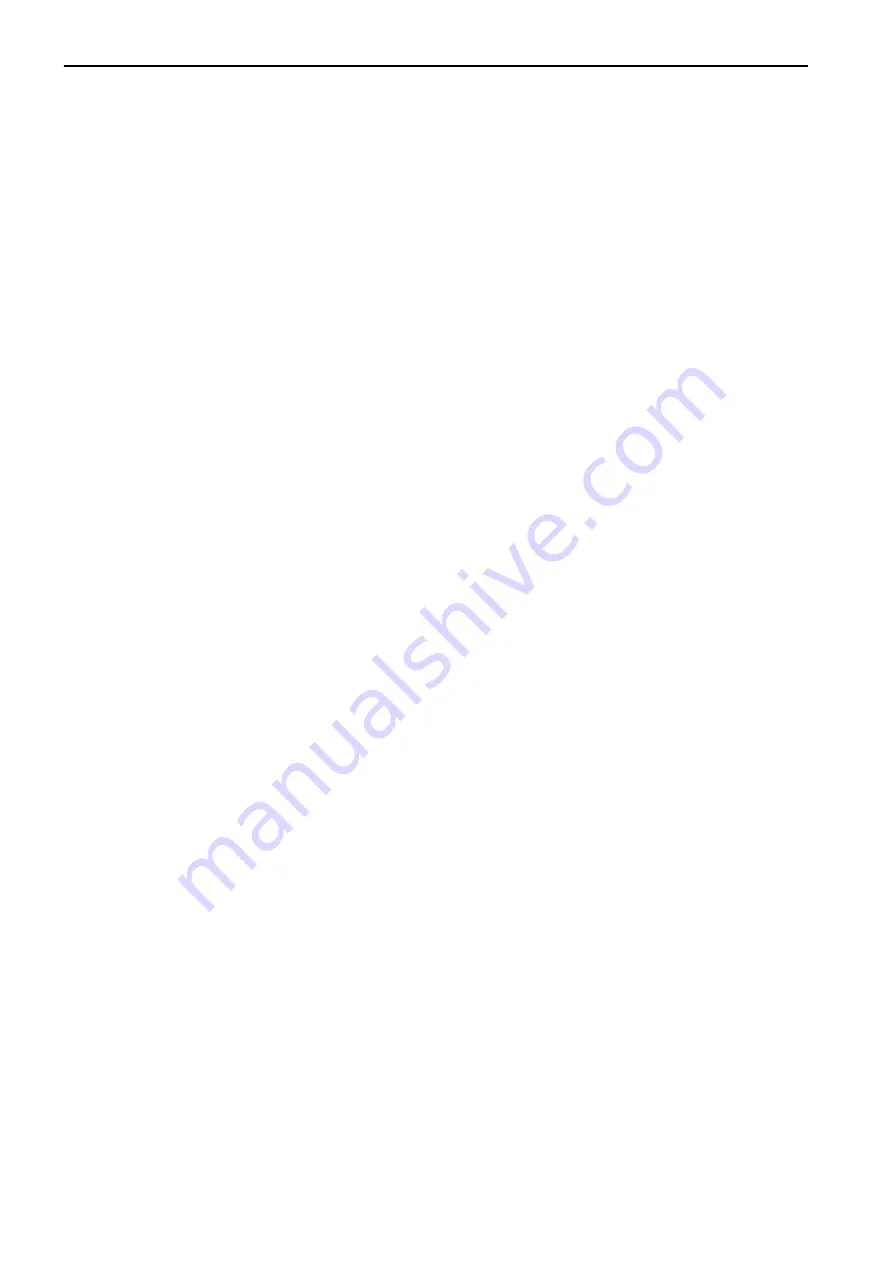
E-83 BLADE EDGE POSITION ON DESIGN SURFACE IS NOT ACCURATE WHEN AUTO GRADE
ASSIST FUNCTION IS ON......................................................................................................40-1348
E-84 BLADE EDGE STOP POSITION IS NOT ACCURATE FOR DESIGN SURFACE WHEN AUTO
STOP CONTROL FUNCTION IS ON ......................................................................................40-1350
E-85 FACING ANGLE COMPASS DOES NOT BECOME PERPENDICULAR TO TARGET .......40-1352
E-86 NG OCCURS VERY OFTEN IN IMU CALIBRATION DIAGNOSIS .....................................40-1353
E-87 CUSHION FOR BOOM RAISE END DOES NOT WORK OR IS WEAK .............................40-1354
E-88 CUSHION FOR ARM IN END DOES NOT WORK OR IS WEAK .......................................40-1355
TROUBLESHOOTING FOR HYDRAULIC AND MECHANICAL SYSTEMS (H MODE) .....................40-1358
INFORMATION MENTIONED IN TROUBLESHOOTING TABLE (H MODE)...............................40-1358
SYSTEM CHART OF HYDRAULIC AND MECHANICAL SYSTEMS ..........................................40-1359
FAILURE MODE AND CAUSE TABLE........................................................................................40-1361
H-1 ALL WORK EQUIPMENT, SWING AND TRAVEL DO NOT WORK......................................40-1373
H-2 ALL WORK EQUIPMENT, SWING AND TRAVEL LACK SPEED AND POWER ..................40-1374
H-3 FINE CONTROL PERFORMANCE OR RESPONSE IS POOR............................................40-1377
H-4 UNUSUAL NOISE IS HEARD FROM AROUND HYDRAULIC PUMP ..................................40-1378
H-5 ENGINE SPEED DROPS LARGELY OR ENGINE STOPS ..................................................40-1379
H-6 SPEED OR POWER OF BOOM IS LOW .............................................................................40-1381
H-7 ARM SPEED OR POWER IS LOW ......................................................................................40-1385
H-8 BUCKET SPEED OR POWER IS LOW................................................................................40-1390
H-9 BUCKET DOES NOT MOVE IN SINGLE OPERATION WITH AUTO TILT FUNCTION ........40-1393
H-10 WORK EQUIPMENT DOES NOT MOVE IN SINGLE OPERATION ...................................40-1394
H-11 HYDRAULIC DRIFT OF BOOM IS LARGE ........................................................................40-1395
H-12 HYDRAULIC DRIFT OF ARM IS LARGE ...........................................................................40-1397
H-13 HYDRAULIC DRIFT OF BUCKET IS LARGE.....................................................................40-1399
H-14 WHEN SINGLE WORK EQUIPMENT IS RELIEVED HYDRAULICALLY, OTHER WORK EQUIP-
MENT MOVES ........................................................................................................................40-1400
H-15 TIME LAG OF WORK EQUIPMENT IS LARGE .................................................................40-1401
H-16 ONE-TOUCH POWER MAXIMIZING FUNCTION DOES NOT OPERATE .........................40-1402
H-17 ATTACHMENT CIRCUIT CANNOT BE CHANGED............................................................40-1403
H-18 OIL FLOW IN ATTACHMENT CIRCUIT CANNOT BE CHANGED .....................................40-1404
H-19 IN COMBINED OPERATION OF WORK EQUIPMENT, EQUIPMENT HAVING HEAVIER LOAD
MOVES SLOWER ...................................................................................................................40-1405
H-20 IN COMBINED OPERATION OF SWING AND TRAVEL, TRAVEL SPEED DROPS LARGELY ......
................................................................................................................................................40-1406
H-21 IN COMBINED OPERATION OF SWING AND BOOM RAISE, BOOM RISING SPEED IS LOW ....
................................................................................................................................................40-1407
H-22 MACHINE DOES NOT TRAVEL STRAIGHT ......................................................................40-1408
H-23 MACHINE IS NOT STEERED WELL OR STEERING POWER IS LOW.............................40-1410
H-24 TRAVEL SPEED IS LOW ...................................................................................................40-1413
H-25 ONE OF TRACKS DOES NOT RUN ..................................................................................40-1415
H-26 TRAVEL SPEED DOES NOT CHANGE, OR TRAVEL SPEED IS TOO SLOW OR FAST ..40-1416
H-27 UPPER STRUCTURE DOES NOT SWING BOTH TO THE RIGHT AND LEFT .................40-1417
H-28 SWINGS ONLY IN ONE DIRECTION.................................................................................40-1418
H-29 SWING ACCELERATION OR SWING SPEED IS LOW IN BOTH DIRECTIONS (RIGHT AND
LEFT) ......................................................................................................................................40-1419
H-30 SWING ACCELERATION PERFORMANCE IS POOR OR SWING SPEED IS SLOW IN ONLY
ONE DIRECTION ....................................................................................................................40-1420
H-31 UPPER STRUCTURE OVERRUNS EXCESSIVELY WHEN IT STOPS SWINGING (BOTH
RIGHT AND LEFT)..................................................................................................................40-1421
H-32 UPPER STRUCTURE OVERRUNS EXCESSIVELY WHEN IT STOPS SWINGING (ONLY ONE
DIRECTION EITHER RIGHT OR LEFT)..................................................................................40-1422
H-33 SHOCK IS LARGE WHEN UPPER STRUCTURE STOPS SWINGING .............................40-1423
H-34 LARGE UNUSUAL NOISE IS HEARD WHEN UPPER STRUCTURE STOPS SWINGING40-1424
H-35 SWING DRIFT ON A SLOPE IS LARGE (WHILE SWING PARKING BRAKE IS APPLIED)40-1425
H-36 SWING DRIFT ON A SLOPE IS LARGE (WHILE SWING PARKING BRAKE IS RELEASED)........
................................................................................................................................................40-1426
H-37 FAN SPEED IS ABNORMAL (TOO HIGH OR LOW, OR STATIONARY) ............................40-1427
INDEX
00 INDEX AND FOREWORD
00-16
PC210LCI-11
Summary of Contents for PC210LCI-11
Page 1: ...HYDRAULIC EXCAVATOR SEN06616 03 PC210LCI 11 SERIAL NUMBERS 500470 and up...
Page 2: ...Find manuals at https best manuals com...
Page 3: ...00 INDEX AND FOREWORD PC210LCI 11 00 1 Find manuals at https best manuals com...
Page 81: ...This as a preview PDF file from best manuals com Download full PDF manual at best manuals com...