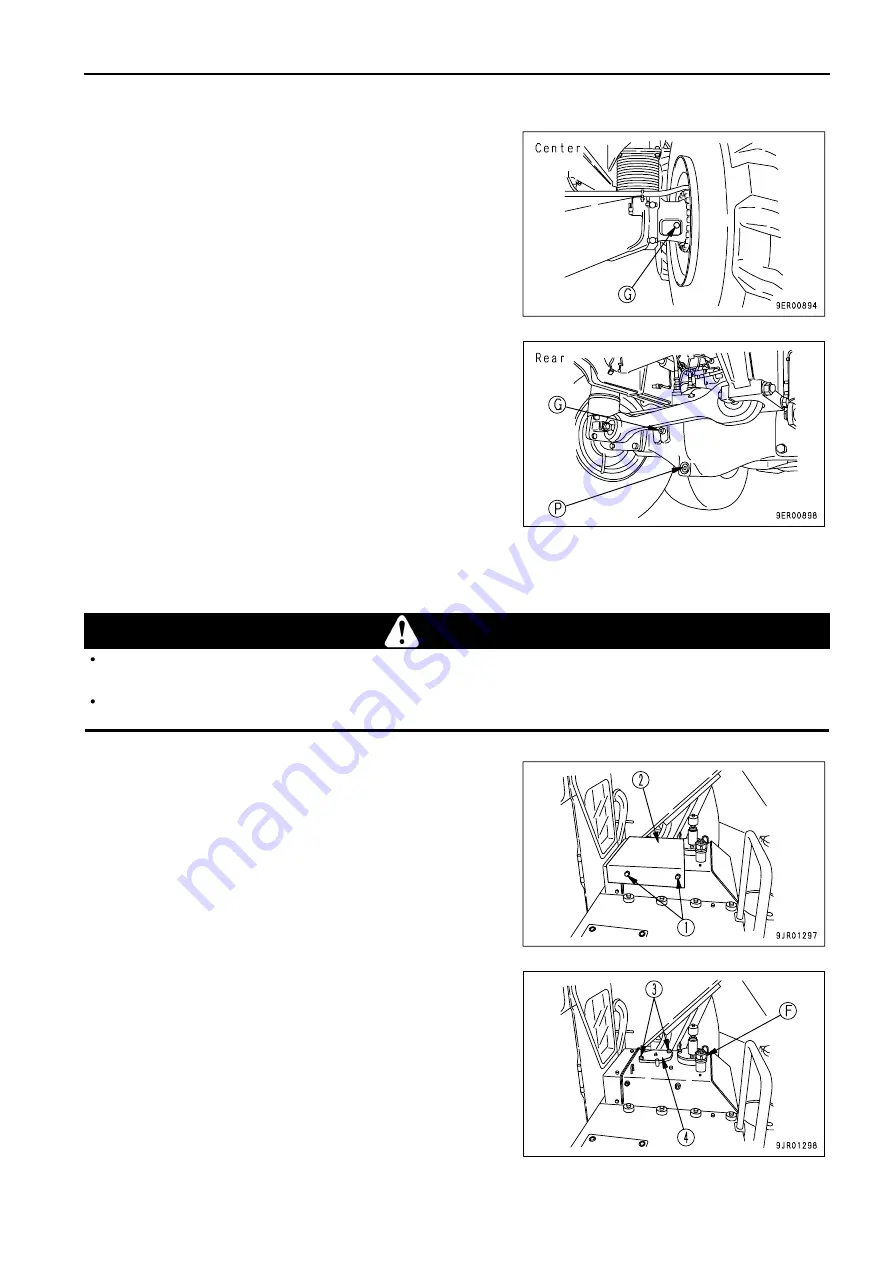
.
MAINTENANCE
SERVICE PROCEDURE
REPLACE HYDRAULIC FILTER ELEMENT
WARNING
The parts and oil are at high temperature after the engine is stopped, and may cause burns. Wait for the temperature to go down
before starting the work.
When removing the oil filler cap, turn it slowly to release the internal pressure, then remove it.
1. Remove bolt (1), then remove cover (2).
2. Turn the cap of oil filler (F) slowly to release the internal
pressure, then remove the cap.
3. Remove bolts (3), then remove cover (4).
4. Take out the element, then wash the inside of the case and the
removed parts.
5. Install the new element, then install cover (4) with bolts (3).
6. Install cover (2) with bolts (1).
4 - 65
Summary of Contents for HM400-1
Page 1: ... 1 1 ...
Page 3: ... FOREWORD FOREWORD 1 3 ...
Page 4: ... FOREWORD FOREWORD 1 4 ...
Page 13: ... 2 1 ...
Page 48: ... ...
Page 49: ... 3 1 ...
Page 179: ... 4 1 ...
Page 252: ... ...
Page 253: ... 5 1 ...
Page 257: ... ...