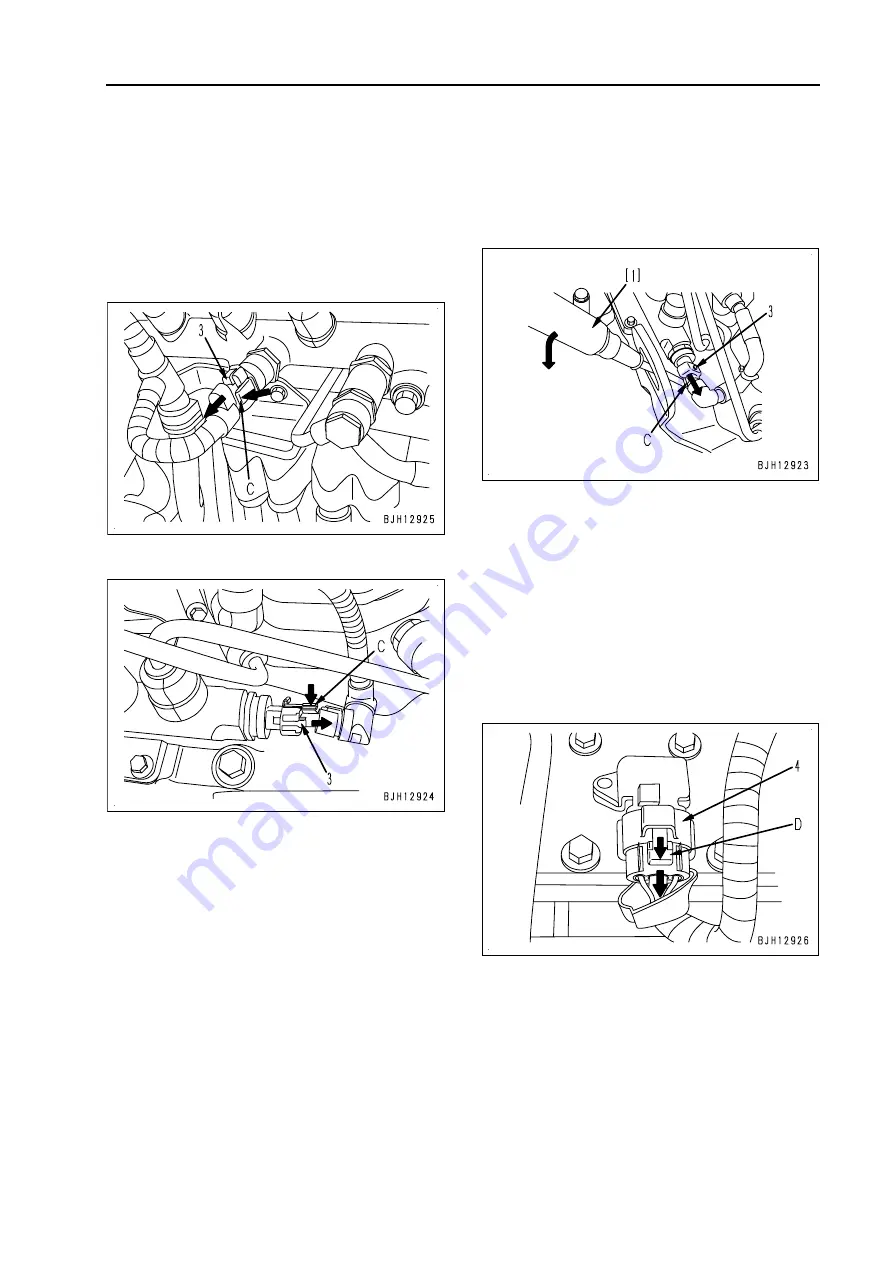
Foreword and general information
Handling of electric equipment
HB205-1, HB215LC-1
2 5
3) Push lock type (1)
q
95/107/114 series
Example) Fuel pressure sensor in
common rail
(BOSCH-03)
Disconnection
While pressing lock (C), pull out connector
(3) in the direction of the arrow.
q
114 series
q
107 series
a
If the lock is located on the underside, use
flat-head screwdriver [1] since you cannot
insert your fingers.
While pressing up lock (C) of the
connector with flat-head screwdriver [1],
pull out connector (3) in the direction of
the arrow.
Connection
Insert the connector straight until it "clicks".
4) Push lock type (2)
q
107/114 series
Example) Intake air pressure/tempera-
ture sensor in intake manifold
(SUMI-
TOMO-04)
Disconnection
While pressing lock (D), pull out connector
(4) in the direction of the arrow.
Connection
Insert the connector straight until it "clicks".
00-25