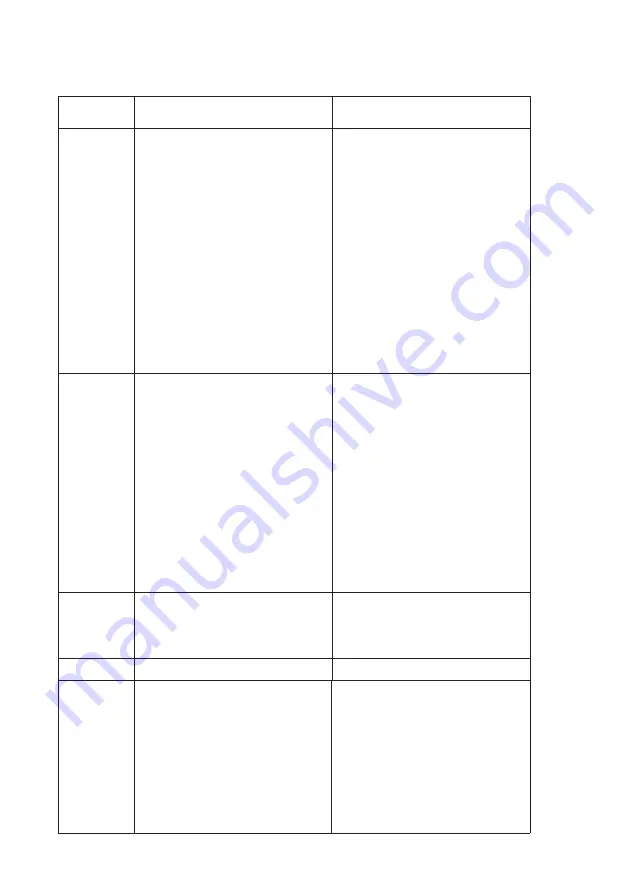
current
h
igh
or
low
or c
an
not
ad
just
2
.
AVR
issue
3
.
Sample
mutual
inductor
winding
fall
of
f
or
loose
4
.
Short
circuit
,
open
circuit
or
grounded
winding
5
.
MDS
or
rectifier
diode
sho
rt
circuit
or
gr
ounded
2
.
Replace
AVR
Replace
mut
ual
inductor
winding
or
connect
3
.
Check
and re
pair
,
or
repl
ac
e
alternator
winding
4
.
Replace
MDS
module
or
rectifier
diode
voltage
high
or
low
2
.
AVR
issue
3
.
sample
wire
fall
off
or
lo
ose
2
.
Replace
AVR
3
.
reconnect
output
1
.
Rotate
speed
hi
gh
or
low
1
.
Adjust
rotate
speed
output
1
.
High
or
low
rot
ate pee
d
1.
Adjust
rotate
speed
genset
no
output
1
.
voltage
meter
broken
2
.
Alternator
leading
wire
and
control
panel
wire
fa
ll
off
or
not
c
onnect
well
.
3
.
Brush
and
slip
ring
do
n
ot co
nnect
well
or di
sconnection
4
.
AVR
cont
rol
p
anel
broken
5
.
Short
ci
rcuit
,
o
p
en
circuit
or
grounded
w
i
r
e
6
.
Circuit
breaker
not open
1.
After
confirm
,
stop
mac
hine an
d
replace
2
.
Check
and
repair
3
.
Clean
slip
ring
or
replace
brush
or
connect
w
i
r
e
4
.
replace
5
.
Inspect
and
repair
,
or
repl
ace
alternator
winding
.
6
.
open
circuit
breaker
(
only
limited
to
assistant
power
)
fault
phenomenon
fault
c
ause
failure
process
Could
not
start
1
.
battery
low
voltage
2
.
fuel
cock
not
open
3
.
Chock
valve
not
open
4
.
Low
oil
level
5
.
Oil
warning
system
problem
6
.
Bad
fuel
oil
quality
7
.
Oil
circuit
block
8
.
Ignition
system
problem
9
.
Carburetor
problem
1.
charge
battery
(
only
for
e
lec
tric
start
)
2.
Open
fuel
cock
3.
Refer
st
ep
3
4.
Check
oil
level
,
add
to
the
level
5.
Pull
up
w
arni
ng
w
ire
,
restart
to
confirm
(
after
c
on
firm
should
s
top
machine
)
6.
Change
fuel
oil
7.
Clean
oil
circuit
8.
Check
and
clean
spark
pl
ug
,
check
ignition
co
il
.
9
.
Clean
or
repair
carburetor
9.Common fault and processing methods
23
Summary of Contents for VOLT VK4X1E
Page 1: ...Owners Manual MODEL VK4X1E OPERATOR S MANUAL 4 In 1...
Page 29: ...10 Schematic diagram 26...
Page 31: ......
Page 32: ......