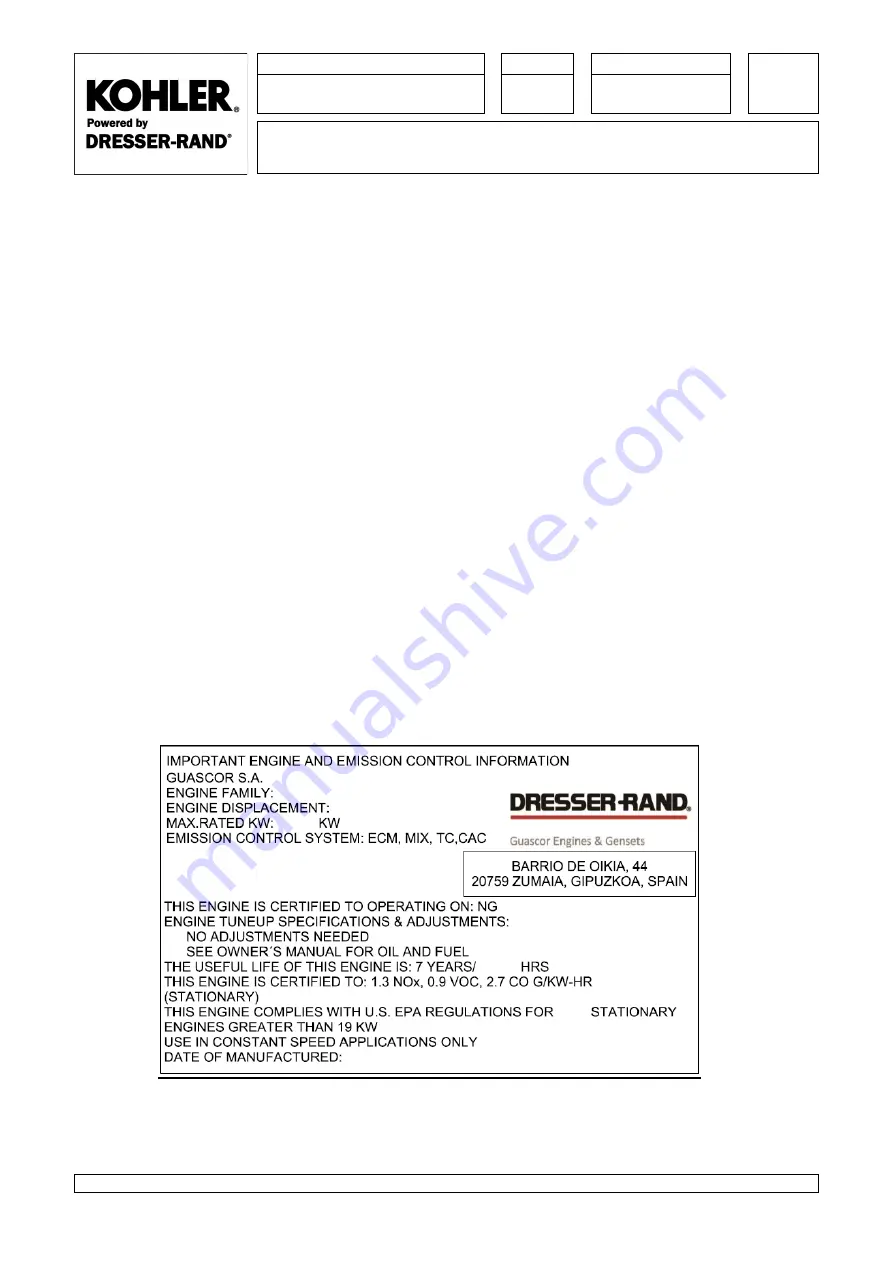
PRODUCT INFORMATION
INDEX
DATE
Dep. 2
IC-G-D-00-253e
April 2016
EMISSIONS PLATE OF EPA CERTIFIED ENGINES
1/2
1. ENGINE IDENTIFICATION PLATE
The emissions plate of the engines with EPA certification under 40 CFR part 60 subpart JJJJ includes the
following information:
- ENGINE FAMILY: EPA certification code corresponding to the engine model
- ENGINE DISPLACEMENT: in litres
- MAX.RATED KW: maximum engine power (the nominal engine power except for Prime applications
where a 10% of overload is allowed, see conditions in IC-C-D-00-002e or in the engine thermal balance)
- EMISSION CONTROL SYSTEM: related to the engine configuration:
o
ECM Electronic Control Module for the electronic control of the carburation
o
MIX for the mixture of air and fuel by a carburetor
o
TC with turbocharger
o
CAC with Chargecooler.
- THIS ENGINE IS CERTIFIED TO OPERATING ON: indicates the fuel which the certification is valid for
o
NG (gas natural)
- THE USEFUL LIFE: running hours/years (which occurs firts) of the engine emissions certifications
warranty.
- THIS ENGINE IS CERTIFIED TO: certified emissions values of pollutants.
- EPA certification year and manufacture year.
On the 180/240 in-line engines it is located on the right-hand side of the crankcase; on the 360/480 and
SFGLD/SFGM 560 V engines, the plate is on the front right-hand side of the crankcase, and on the HGM
420/560 on the bottom right front panel of the water distribution box.
Fig. 1 - EPA emissions Plate
2.1.9
O&M_2.002211.810_A_10_2016