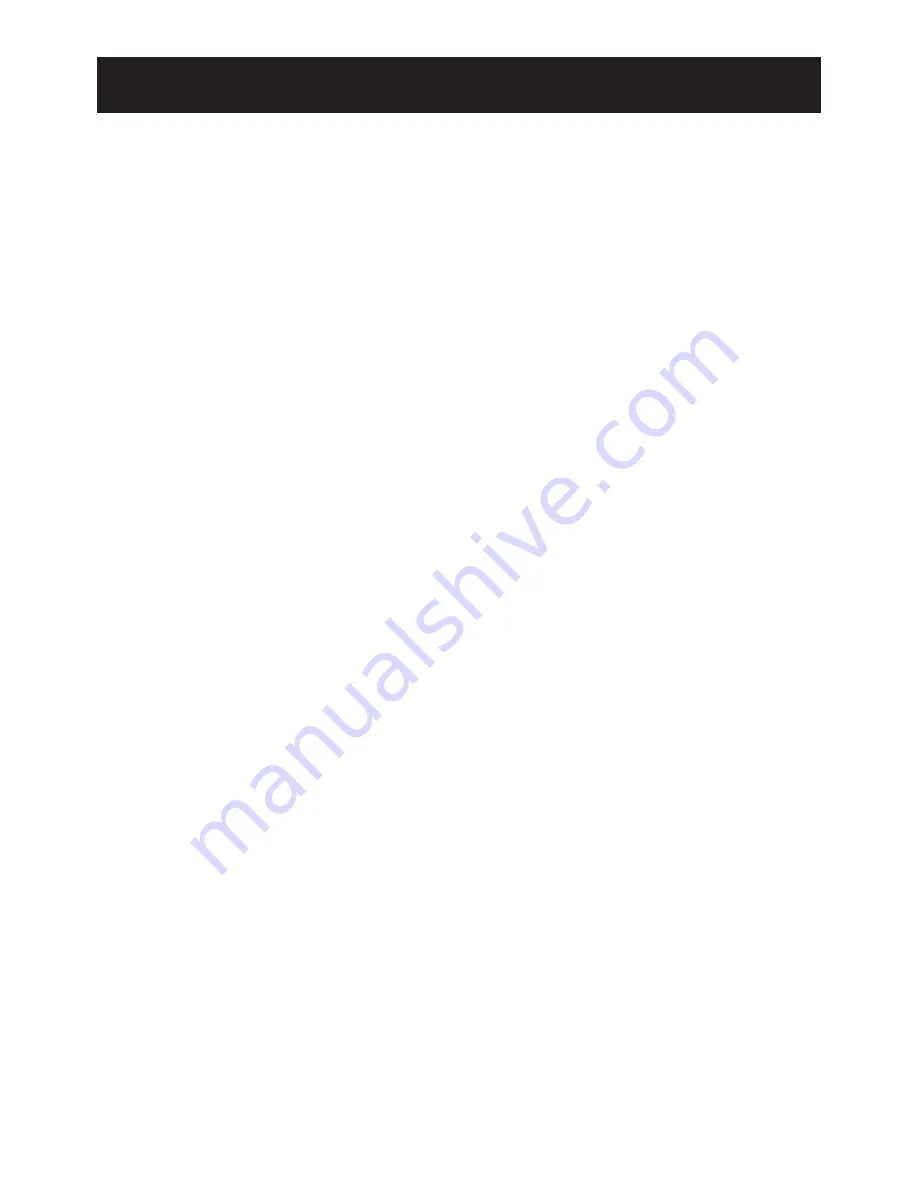
11
Installation Requirements
Plumbing
1.
The Mira Zest 7.5 kW and 8.5 kW electric showers are designed to operate with
a
minimum maintained inlet pressure of 0.7 bar
up to a
maximum static
inlet pressure of 10 bar
.
2.
The appliance is normally connected to the cold water mains-fed supply.
However, the water supply can be taken from a cold water storage cistern,
provided there is a minimum maintained inlet head of water of 7 metres (the
vertical distance from the base of the cold water storage cistern to the shower
fitting handset). To reduce pressure losses and fluctuations, the cistern-fed
water supply must be independent from other supply draw-offs, and should
avoid long horizontal pipe runs and use swept bends rather than 90° elbows. For
further advice please refer to the back cover of this guide for Mira Showers
contact telephone and fax numbers.
3.
The appliance is suitable for installation within the shower area. It is fitted with
a pressure relief device and must be positioned over a water catchment area
with the controls at a convenient height for the user. The shower fitting should
be positioned so that it discharges down the centre line of the bath, or across
the opening of a shower cubicle, and must be directed away from the appliance.
4.
The appliance is fitted with an inlet connector assembly that is designed to
accept plumbing supplies from the top or bottom. The water supply can be fed
with 15 mm pipe or 10 mm microbore pipe, suitably adapted into the inlet
connector assembly. If 10 mm microbore is used, then an allowance for
increased pressure loss must be made to ensure that the minimum maintained
inlet pressure is achieved.
5.
Do not
fit the appliance to the wall and tile up to the case. The appliance must
be fitted onto a finished flat and even wall surface. Otherwise, difficulty may be
encountered when fitting the cover, and subsequent operation of the unit could
be impaired (small pillars moulded on to the back of the case allow air
circulation).
6.
Use only the inlet connector assembly supplied with the appliance.
Do not
use
any other types of fitting.
7.
Refrain from applying excessive force when making any connections. Always
provide mechanical support when making the plumbing connections.
8.
This appliance is not designed to be plumbed directly from the rear. For a rear-
entry supply, add an elbow to the supply pipe and connect it as a rising or falling
supply.