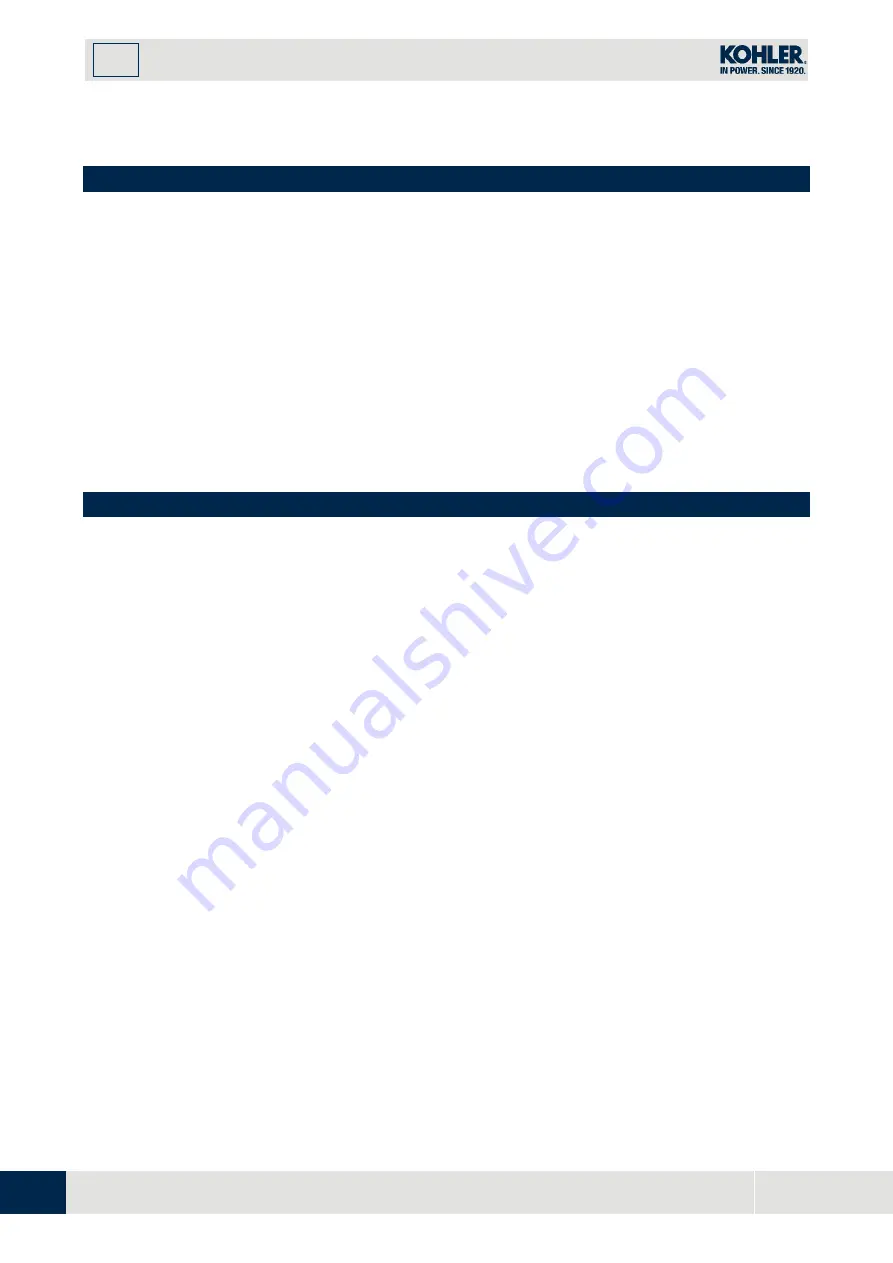
3
SAFETY
INFORMATION
EN
26
3
SAFETY INFORMATION
3.1
Safety information
•
The intended use of the engine is in conformity with the machine on which it is mounted.
•
Any use of the machine other than that described cannot be considered as complying with its
intended purpose as specified by
KOHLER
.
•
KOHLER
declines all responsibility for any change to the engine not described in this manual
made by unauthorized
KOHLER
personnel.
•
A proper use of the engine, a strict observance of the rules listed below and the rigorous
application of all these precautions will avoid the risk of accidents or injuries.
•
Those who carry out the use and maintenance on the engine must wear the safety equipment
and the accident-prevention guards.
•
KOHLER
declines all direct and indirect liability for failure to comply with the standards of
conduct contained in this manual.
•
KOHLER
cannot consider every reasonably unforeseeable misuse that may cause a potential
danger.
3.2
General remarks
3.2.1 Note for OEM
•
When installing the KDI engines, always bear in mind that any variation to the functional systems
may result in serious failures to the engine.
•
Any improvement must be verified at
KOHLER
testing laboratories before application of the
engine.
•
In case the approval to a modification is not granted,
KOHLER
shall not be deemed responsible
for any consequential failures or damages to the engine.
•
Those who carry out the use and maintenance on the engine must wear the safety equipment
and the accident-prevention guards.
•
KOHLER
declines all direct and indirect liability for failure to comply with the standards of
conduct contained in this manual.
•
KOHLER
cannot consider every reasonably unforeseeable misuse that may cause a potential
danger.
3.2.2
Note for end user
•
The following indications are dedicated to the user of the machine in order to reduce or eliminate
risks concerning engine operation and the relative routine maintenance work.
•
The user must read these instructions carefully. Failure to do this could lead to serious danger for
his personal safety and health and that of any persons who may be in the vicinity of the machine.
•
On starting, make sure that the engine is as horizontal as possible, unless the machine
specifications differ.
•
Make sure that the machine is stable to prevent the risk of overturning.
•
The engine must not operate in places containing inflammable materials, in explosive
atmospheres, where there is dust that can easily catch fire unless specific, adequate and clearly
indicated precautions have been taken and have been certified for the machine.
•
To prevent fire hazards, always keep the machine at least one meter from buildings or from other
machinery.
•
Children and animals must be kept at a due distance from operating machines in order to prevent
hazards deriving from their operation.
Summary of Contents for KDI 3404TCR-SCR
Page 2: ...INDEX EN ...
Page 7: ...GENERAL INFORMATION 1 7 EN 1 5 Manufacturer and engine identification 1 1 ...
Page 8: ...1 GENERAL INFORMATION EN 8 1 6 Engine component identification ...
Page 10: ...1 GENERAL INFORMATION EN 10 1 7 Cooling circuit ...
Page 12: ...1 GENERAL INFORMATION EN 12 1 8 AdBlue circuit ...
Page 14: ...1 GENERAL INFORMATION EN 14 1 9 Intake and exhaust circuit ...
Page 63: ...GLOSSARY 9 63 EN ...
Page 64: ......