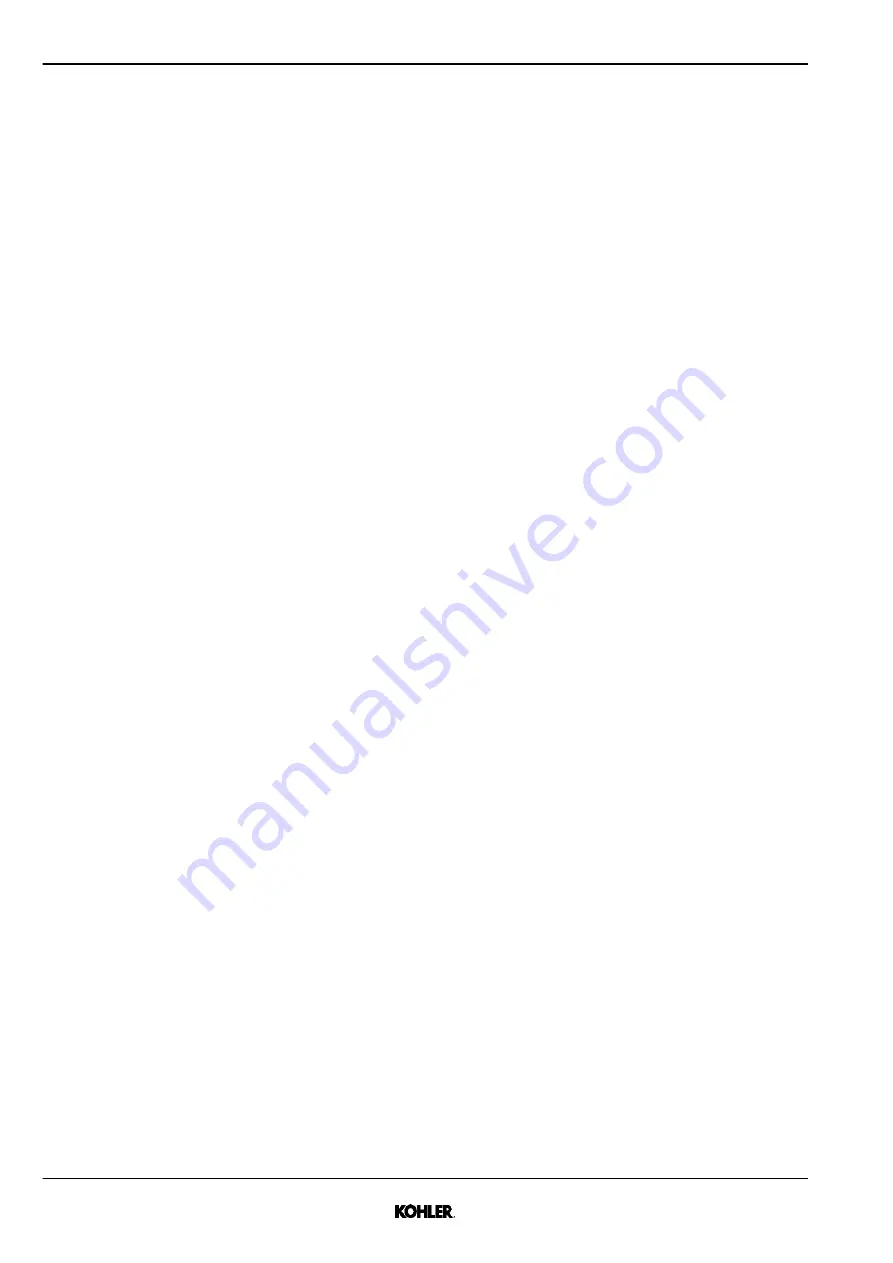
Safety
Operation and Maintenance Manual
Foreseeable misuse
2.3 Intended use
– Only use the diesel engine for its intended purpose.
– Observe the following conditions of the manufacturer:
•
Operating conditions
•
Servicing conditions
•
Maintenance conditions
– Make sure that the following work is only carried out by personnel in
accordance with the target audience definition:
•
Using the diesel engine.
•
Servicing the diesel engine.
•
Maintaining the diesel engine.
Please refer to the “Target audience” chapter for additional information.
– Install all of the guards and protective devices and check their functions before
commissioning.
– Pay attention to the safety and operating instructions.
– Only operate the engine if it is in perfect working order.
– Only operate the engine in the speed range specified by the manufacturer.
– Bolt the engine to the machine or the corresponding place of use by the fitted
engine mounts and the corresponding tensioning instructions.
– If engine mounts are used that have not been fitted by the manufacturer these
have to be approved by the manufacturer.
– The engine may only be operated in areas that cannot be accessed by the
general public, in other words the engine may only be operated in conjunction
with an enclosure or engine compartment cover.
2.4 Foreseeable misuse
The operating and maintenance manual has been drawn up in accordance with
applicable standards and regulations in accordance with state-of-the-art
technology.
Kohler Co. assumes no liability for:
– Failure to observe these instructions
– Incorrect use
– The employment of personnel who do not satisfy the target audience
requirements.
– Alterations and conversions of the diesel engine that have been carried out
without the consent of Kohler Co.
– Operating and auxiliary materials that have not been approved by Kohler Co.
– The use of non-Kohler spare parts that have not been officially approved by
Kohler Co., including the resulting consequential damages.
– Circumvention of and non-compliance with the safety regulations
– Failure to observe international and national regulations on occupational health
and safety
– Failure to observe international and national regulations on environmental
protection
– Unauthorized modifications to the diesel engine
– Manipulations to the injection and control system
22
© 2018 by Kohler Co. All rights reserved.
KD45V20 33521030001_4_1 en 2018-08-01