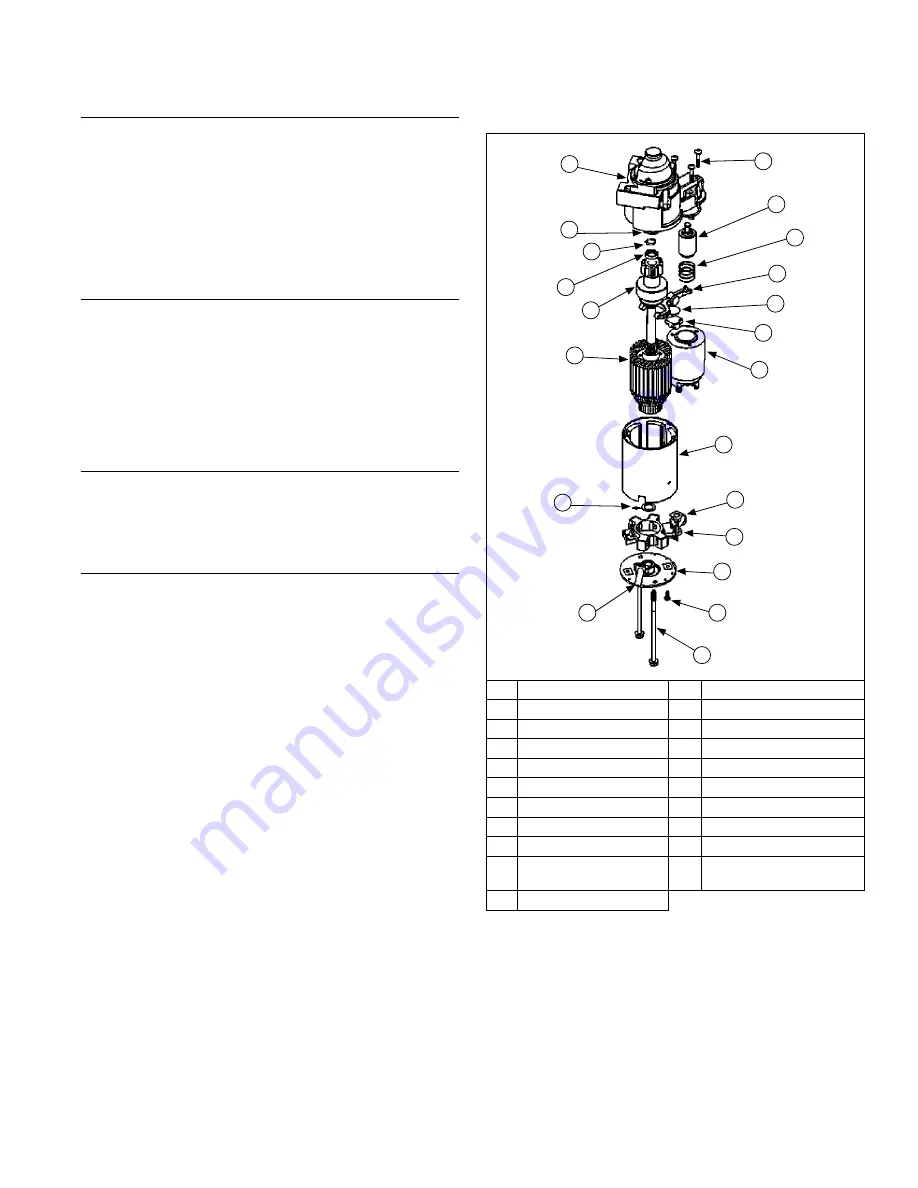
Starter System
45
32 690 01 Rev. D
KohlerEngines.com
Starter Disassembly
1. Remove drive components following instructions for
servicing drive.
2. Remove thru bolts.
3. Remove commutator end cap containing brush
holder, brushes, brush springs and thrust washer
(cup).
4. Remove drive end cap.
5. Remove armature from inside starter frame.
End Cap/Brush Replacement
Brushes are contained in a plastic carrier housing,
attached to end cap. Replacement brushes in brush
holder come preassembled, attached to end cap with
commutator end thrust washer (cup) holding brushes in
retracted position. When installation is performed, end
of armature shaft will push thrust washer (cup) back into
final position allowing brushes to contact commutator.
Do not remove protective tape and shipping strip holding
washer (cup) until part is ready to be installed.
Commutator Service
Clean commutator with a coarse, lint free cloth. Do not
use emery cloth.
If commutator is badly worn or grooved, turn it down on
a lathe or replace starter.
Starter Reassembly
1. Insert armature into starter frame. Make sure
magnets are closer to drive shaft end of armature.
Magnets will hold armature inside frame.
2. Install drive end cap over drive shaft and align with
cutout starter frame.
3. Installing new brushes: carefully remove tape
holding thrust washer (cup) in place against brushes.
Do not allow thrust washer (cup) to move out of this
position. Align terminal stud block with notch in
starter frame and start brush holder/end cap
assembly onto end of armature.
4. Pull out thin shipping strip from behind thrust washer
(cup), and slide brush holder/end cap into position.
5. Install thru bolts and torque to 4.5-5.7 N·m
(40-50 in. lb.).
6. Lubricate drive shaft with Kohler starter drive
lubricant. Install drive components following
instructions for servicing starter drive.
SOLENOID SHIFT STARTERS
Solenoid Shift Starter Components
A
B
U
T
S
R
Q
P
O
N
M
L
K
J
I
H
G
F
E
D
C
A
Tube
B
Washer
C
Armature
D
Drive
E
Stop
F
Retaining Ring
G
Collar
H
Drive End Cap
I
Screw
J
Plunger
K
Spring
L
Lever
M
Plate
N
Plug
O
Solenoid
P
Frame and Field
Q
Brush Holder
R
Nut
S
Commutator End
Plate
T
Screw
U
Bolt
When power is applied to starter electric solenoid moves
drive pinion out onto drive shaft and into mesh with
flywheel ring gear. When pinion reaches end of drive
shaft it rotates flywheel and cranks engine.
When engine starts and start switch is released, starter
solenoid is deactivated, drive lever moves back, and
drive pinion moves out of mesh with ring gear into
retracted position.