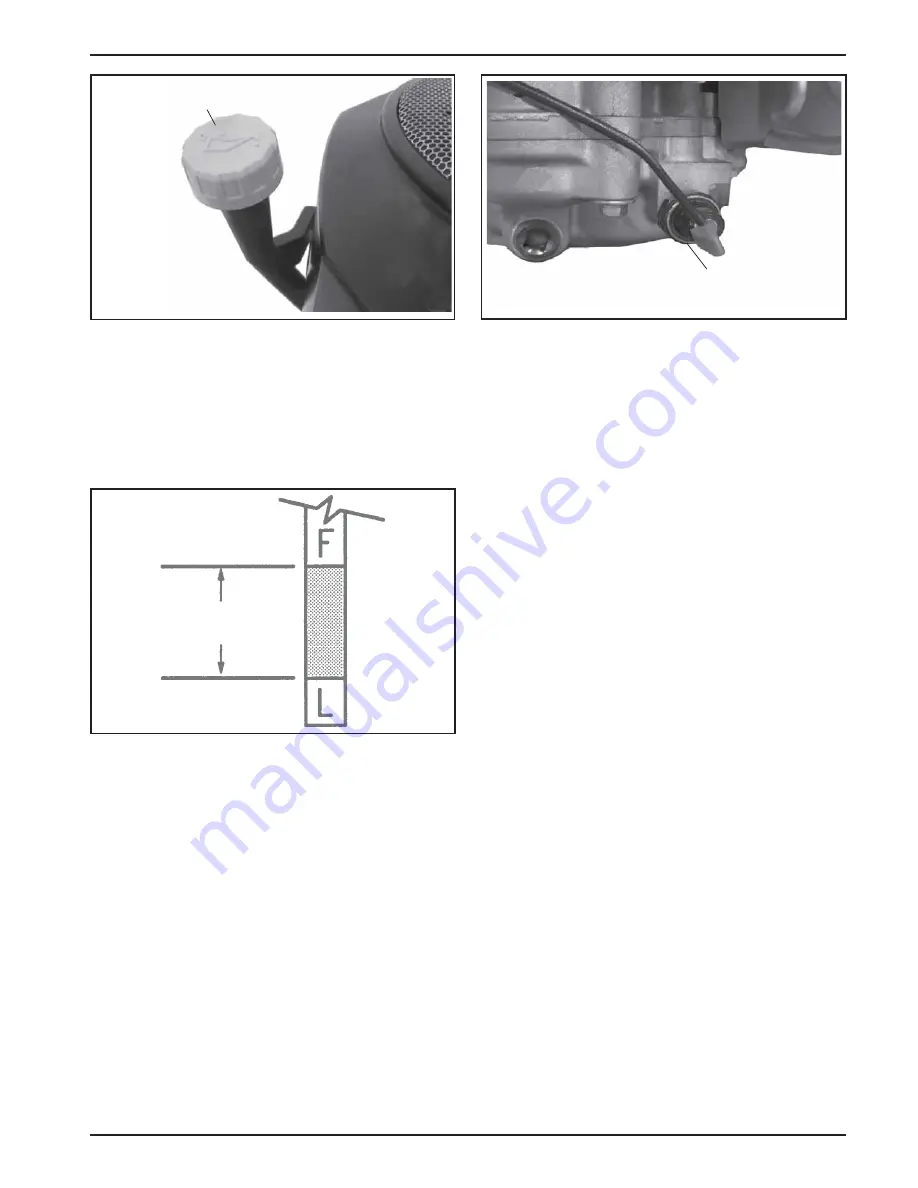
9
Oil Fill Cap/Dipstick
Figure 9. Oil Fill Cap/Dipstick.
4. Remove the oil fill cap/dipstick and check oil
level. The level should be between the “F” and
“L” marks. See Figure 10. If low, add oil of the
proper type up to the “F” mark. Reinstall the oil
fill cap/dipstick and thread tight. (Refer to
Oil
Type
on page 4.) Always check the level with the
dipstick before adding more oil.
Figure 10. Oil Level Marks on Dipstick.
NOTE: To prevent extensive engine wear or damage,
always maintain the proper oil level in the
crankcase. Never operate the engine with the
oil level below the “L” mark or over the “F”
mark on the dipstick.
Oil Sentry™
Most engines are equipped with an Oil Sentry™ oil
pressure switch. On pressure switch equipped
models, if the oil pressure decreases below an
acceptable level, the Oil Sentry™ will either shut off
the engine or activate a warning signal, depending on
the application. See Figure 11.
Figure 11. Oil Sentry™ Pressure Switch.
NOTE: Make sure the oil level is checked
BEFORE
EACH USE
and is maintained up to the “F”
mark on the dipstick. This includes engines
equipped with Oil Sentry™ systems.
Change Oil and Filter, Service Oil Cooler
Change Oil
Change oil
seasonally or every 150 hours
of operation,
(more frequently under severe conditions). Refill with
service class SJ or higher oil as specified in the
Viscosity Grades
table (Figure 2) on page 4.
Change the oil while the engine is still warm. The oil
will flow more freely and carry away more
impurities. Make sure the engine is level when filling,
checking, and changing the oil.
Change the oil as follows (see Figures 12 and 13):
1. To keep dirt, debris, etc., out of the engine, clean
the area around the oil fill cap/dipstick and one of
the drain plugs.
2. Remove one of the oil drain plugs and the oil fill
cap/dipstick. Be sure to allow ample time for
complete drainage.
3. Reinstall the drain plug. Make sure it is tightened
to
21.4 N·m (15.7 ft. lb.)
torque.
4. Fill the crankcase, with new oil of the proper
type, to the “F” mark on the dipstick. Refer to Oil
Type on page 4. Always check the level with the
dipstick before adding more oil.
5. Reinstall the oil fill cap/dipstick and tighten
securely.
Operating
Range
Pressure Switch