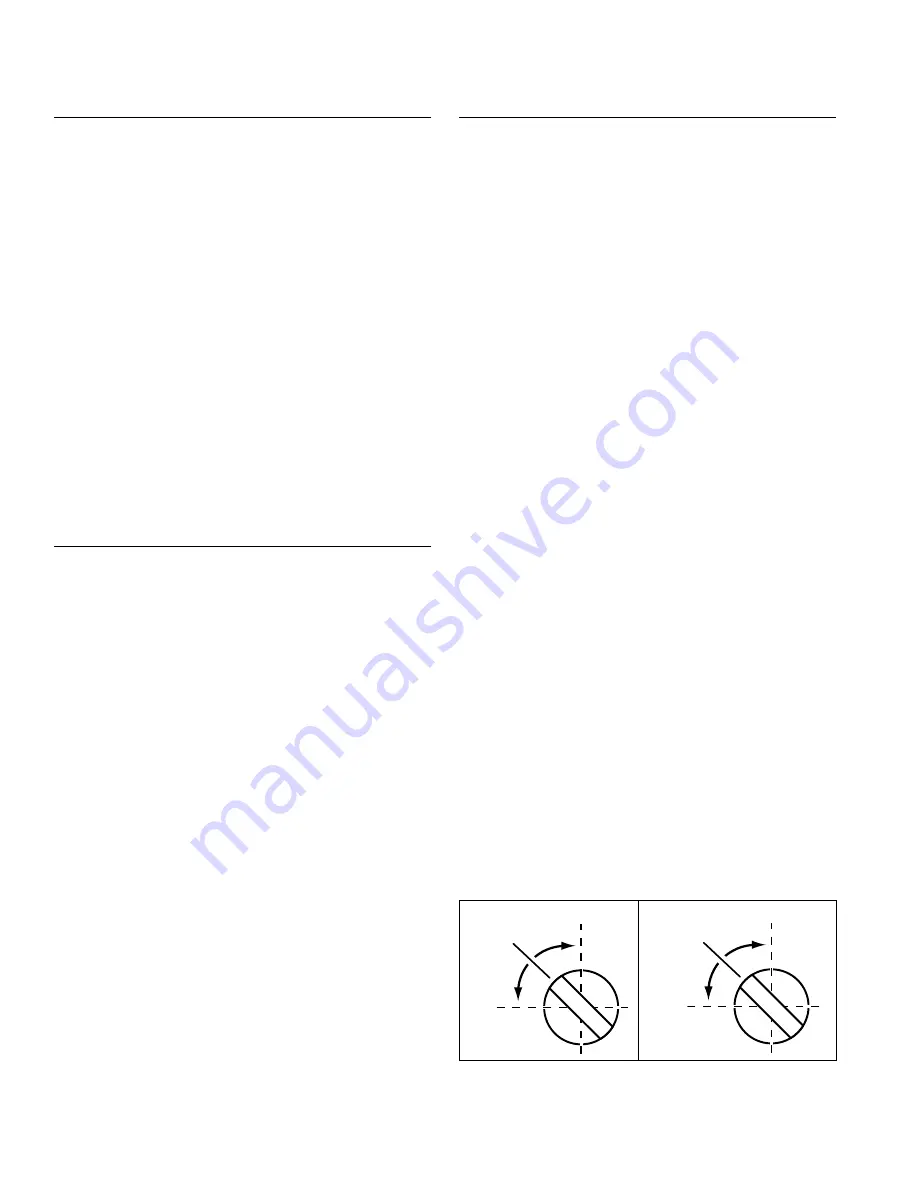
Fuel System
32
62 690 01 Rev. J
KohlerEngines.com
Fuel Shut-off Solenoid
Most carburetors are equipped with a fuel shut-off
solenoid. Solenoid is attached to fuel bowl. Solenoid has
a spring-loaded pin that retracts when 12 volts is applied
to lead, allowing fuel flow to main jets. When current is
removed pin extends blocking fuel flow.
Below is a simple test, performed with engine off, that
can determine if solenoid is functioning properly:
1. Shut off fuel and remove solenoid from carburetor.
When solenoid is loosened and removed, gas will
leak out of carburetor. Have a container ready to
catch fuel.
2. Wipe tip of solenoid with a shop towel or blow with
compressed air to remove any remaining fuel. Take
solenoid to a location with good ventilation and no
fuel vapors present. You will also need a 12 volt
power source that can be switched on and off.
3. Be sure power source is switched OFF. Connect
positive power source lead to red lead of solenoid.
Connect negative power source lead to solenoid
body.
4. Turn power source ON and observe pin in center of
solenoid. Pin should retract with power ON and
return to its original position with power OFF. Test
several times to verify operation.
Carburetor Circuits
Float
Fuel level in bowl is maintained by float and fuel inlet
needle. Buoyant force of float stops fuel flow when
engine is at rest. When fuel is being consumed, float will
drop and fuel pressure will push inlet needle away from
seat, allowing more fuel to enter bowl. When demand
ceases, buoyant force of float will again overcome fuel
pressure, rising to predetermined setting and stop flow.
Slow and Mid-Range
At low speeds engine operates only on slow circuit.
As a metered amount of air is drawn through slow air
bleed jets, fuel is drawn through 2 main jets and further
metered through slow jets. Air and fuel are mixed in body
of slow jet and exit to transfer port. From transfer port,
air fuel mixture is delivered to idle progression chamber.
From idle progression chamber, air fuel mixture is
metered through idle port passages. At low idle when
vacuum signal is weak, air/fuel mixture is controlled by
setting of idle fuel adjusting screws. This mixture is then
mixed with main body of air and delivered to engine.
As throttle plate opening increases, greater amounts of
air/fuel mixture are drawn in through fixed and metered
idle progression holes. As throttle plate opens further,
vacuum signal becomes great enough so main circuit
begins to work.
Main (high-speed)
At high speeds/loads engine operates on main circuit.
As a metered amount of air is drawn through 4 air jets,
fuel is drawn through main jets. Air and fuel are mixed
in main nozzles then enter main body of airflow where
further mixing of fuel and air occurs. This mixture is then
delivered to combustion chamber. Carburetor has a fixed
main circuit; no adjustment is possible.
Carburetor Adjustments
NOTE: Carburetor adjustments should be made only
after engine has warmed up.
Carburetor is designed to deliver correct fuel-to-air
mixture to engine under all operating conditions. Main
fuel jet is calibrated at factory and is not adjustable.
Idle fuel adjusting needles are also set at factory and
normally do not need adjustment.
Low Idle Speed (RPM) Adjustment
NOTE: Actual low idle speed depends on application.
Refer to equipment manufacturer’s
recommendations. Low idle speed for basic
engines is 1200 RPM. To ensure best results
when setting low idle fuel needle, low idle speed
should be 1200 RPM (± 75 RPM).
1. Place throttle control into idle or slow position. Turn
low idle speed adjusting screw in or out to obtain a
low idle speed of 1200 RPM (± 75 RPM).
Governed Idle Speed Adjustment
1. Make sure governed idle spring is in outer hole in
governor lever and hole in governed idle (outer)
adjuster.
2. Make sure governor spring is in inner slot of
governor lever and hole in high speed (inner)
adjuster. Pull governor lever away from carburetor to
limit its travel and check that governor spring is
loose and not under any tension. Turn high-speed
(RPM) adjustment screw counterclockwise
(if
required) until spring is loose.
3. Hold governor lever away from carburetor so throttle
lever is against idle speed (RPM) adjustment screw
of carburetor. Start engine and allow to warm up,
then adjust screw to set approximately 1200 RPM.
Check speed using a tachometer. Turn adjustment
screw (inner) clockwise (in) to increase or
counterclockwise (out) to decrease speed.
4. Release governor lever and check that throttle lever
is in idle (centered) position. Turn governed idle
(outer) adjustment screw to obtain equipment
manufacturer’s recommended idle speed
(1500-1800 RPM). Governed idle speed (RPM) is
typically 300 RPM (approximate) higher than low idle
speed.
5. Move throttle lever to wide-open/full throttle position
and hold in this position. Turn high speed screw to
obtain intended high speed no-load RPM. Governed
idle speed must be set before making this
adjustment.
Low Idle Fuel Adjustment
Lean
Rich
Adjust to
Midpoint
Lean
Rich
Adjust to
Midpoint
Left Side
Right Side