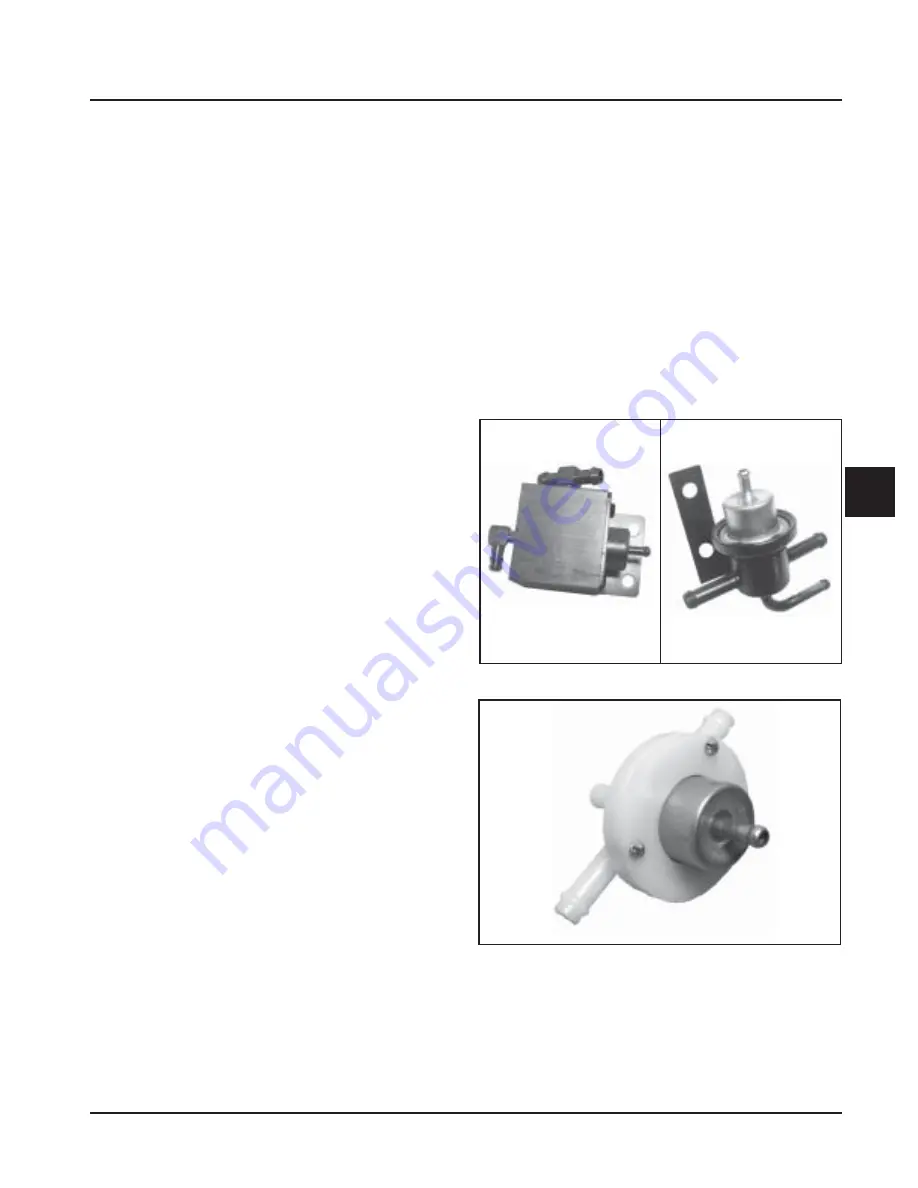
5B.19
Section 5B
EFI Fuel System
5B
pump preventing the continued delivery of fuel. In
this situation, the MIL will go on, but it will go back
off after 4 cranking revolutions if system function is
OK. Once the engine is running, the fuel pump
remains on.
Service
The fuel pumps are non-serviceable and must be
replaced if determined to be faulty. If a fuel delivery
problem is suspected, make certain the pump is being
activated through the relay, all electrical connections
are properly secured, the fuses are good, and a
minimum of 7.0 volts is being supplied. If during
cranking, voltage drops below 7.0 volts, a reduction of
fuel pressure may occur resulting in a lean starting
condition. If required, testing of the fuel pump and
relay may be conducted.
1. Connect the black hose of Pressure Tester (part of
EFI Service Kit, see Section 2) to the test valve in
the fuel rail. Route the clear hose into a portable
gasoline container or the equipment fuel tank.
2. Turn on the key switch to activate the pump and
check the system pressure on the gauge. If system
pressure of 39 psi ± 3 is observed, the relay, fuel
pump, and regulator are working properly. Turn
key switch off and depress the valve button on
the tester to relieve the system pressure.
a. If the pressure is too high, and the regulator
is outside the tank (just down line from the
pump), check that the return line from the
regulator to the tank is not kinked or
blocked. If the return line is good, replace
the regulator (see ‘‘Regulator Service’’ on
page 5B.20).
b. If the pressure is too low, install in-line ‘‘T’’
between the pump and the regulator and
retest the pressure at that point. If it is too low
there also, replace the fuel pump.
3. If the pump did not activate (step 2), disconnect
the plug from the fuel pump. Connect a DC
voltmeter across the terminals in the plug, turn
on the key switch and observe if a minimum of 7
volts is present. If voltage is between 7 and 14,
turn key switch off and connect an ohmmeter
between the terminals on the pump to check for
continuity.
a. If there was no continuity between the pump
terminals, replace the fuel pump.
Figure 5B-24. External Fuel Pressure Regulators.
Figure 5B-25. Internal Fuel Pressure Regulators.
b. If the voltage was below 7, test the wiring
harness and relay as covered in the
‘‘Electrical Relay’’ section.
4. If voltage at the plug was good, and there was
continuity across the pump terminals, reconnect
the plug to the pump, making sure you have a
good connection. Turn on the key switch and
listen for the pump to activate.
a. If the pump starts, repeat steps 1 and 2 to
verify correct pressure.
b. If the pump still does not operate, replace it.
Fuel Pressure Regulator