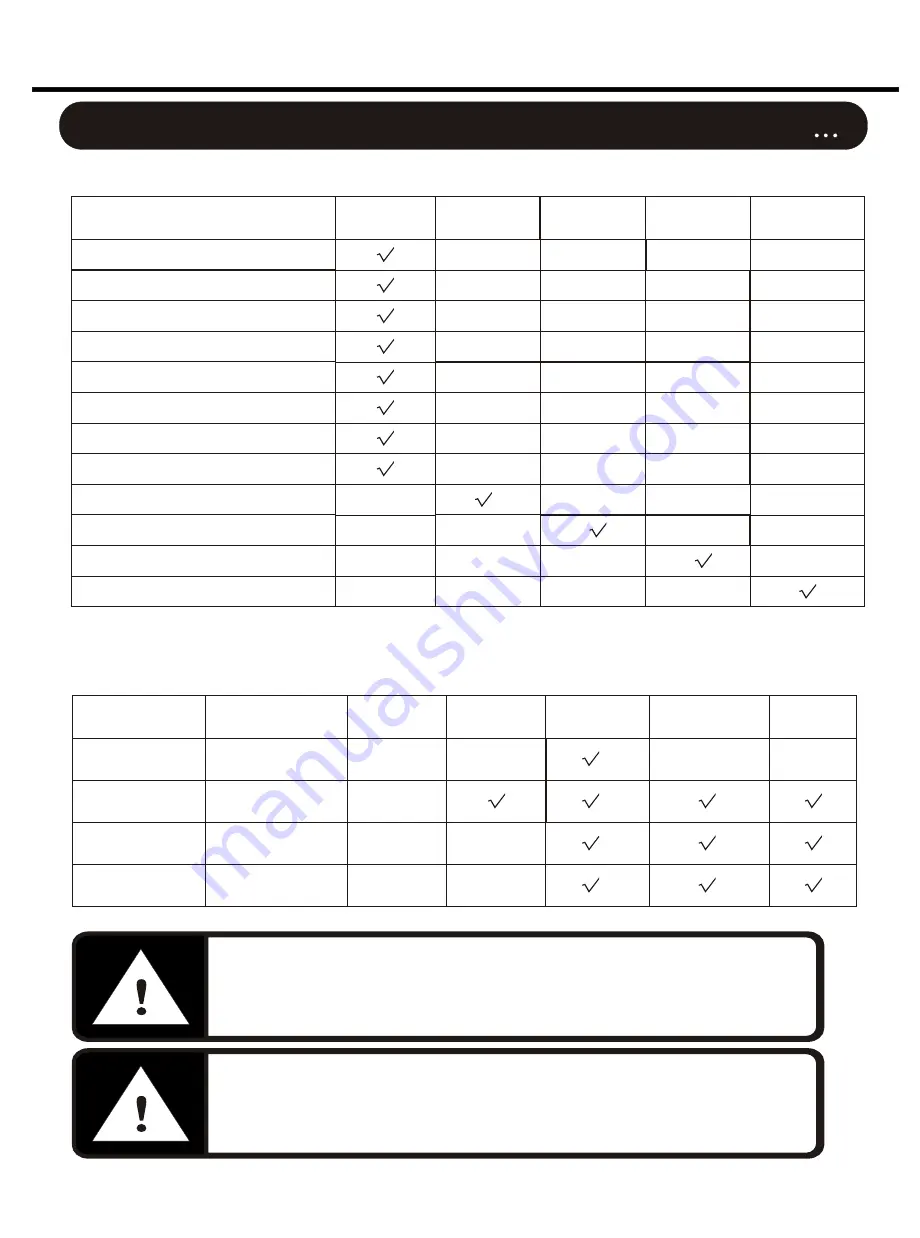
Maintenance Procedures cont'd
2. Maintenance Schedule
Item to check
10 Service
Hours
15 Service
Hours
25 Service
Hours
50 Service
Hours
Every Six
Months
Operator Presence System
Brake Adjustment
Teeth and Cutter Wheel Assembly
Tires and Chip Curtains
Walk Around Inspection
Wires and Cables
Bolts and Mounting Hardware
Safety Labels
New Drive Belt
Grease Cutter Shaft Bearings
Drive Belt Tension
Wheel Bearings
3. Lubrication Schedule
Regularly scheduled lubrication of the LGSG13HC is essential to smooth performance and extended equipment
life. The following schedule is a recommended guide to lubricating your LGSG13HC. The schedule should
be adjusted for various environmental conditions and frequency of use.
Item
Suggested
lubricant
Every 20
hours
Every 60
hours
As required
After each
pressure wash
storage
Engine
Refer to owner's
manual for Engine
Wheel
Lithium-based
Grease
Cutting Teeth,
Pockets & Wheel
General purpose
spray lubricant
Zerks
General purpose
spray lubricant
Technician should read and thoroughly understand all manuals pertaining
to the machine to be serviced. Do NOT proceed with any service and
maintenance activity until ALL questions and concerns have been addressed.
Please call your local dealer for technical support andadvice.
! ALWAYS consult and verify that all local codes and bylaws are followed
before performing any service or maintenance procedures.
18
Summary of Contents for LGSG13HC
Page 1: ...original instruction 2013 LGSG13HC Uniguip...
Page 7: ...Machine Parts Breakdown 5 LGSG13HC...
Page 8: ...Machine Parts Breakdown 6 LGSG13HC...
Page 9: ...Parts List 7...
Page 10: ...Parts List 8...
Page 11: ...Parts List 9...
Page 13: ...Machine Overview cont d 11...
Page 27: ...Notes 25...