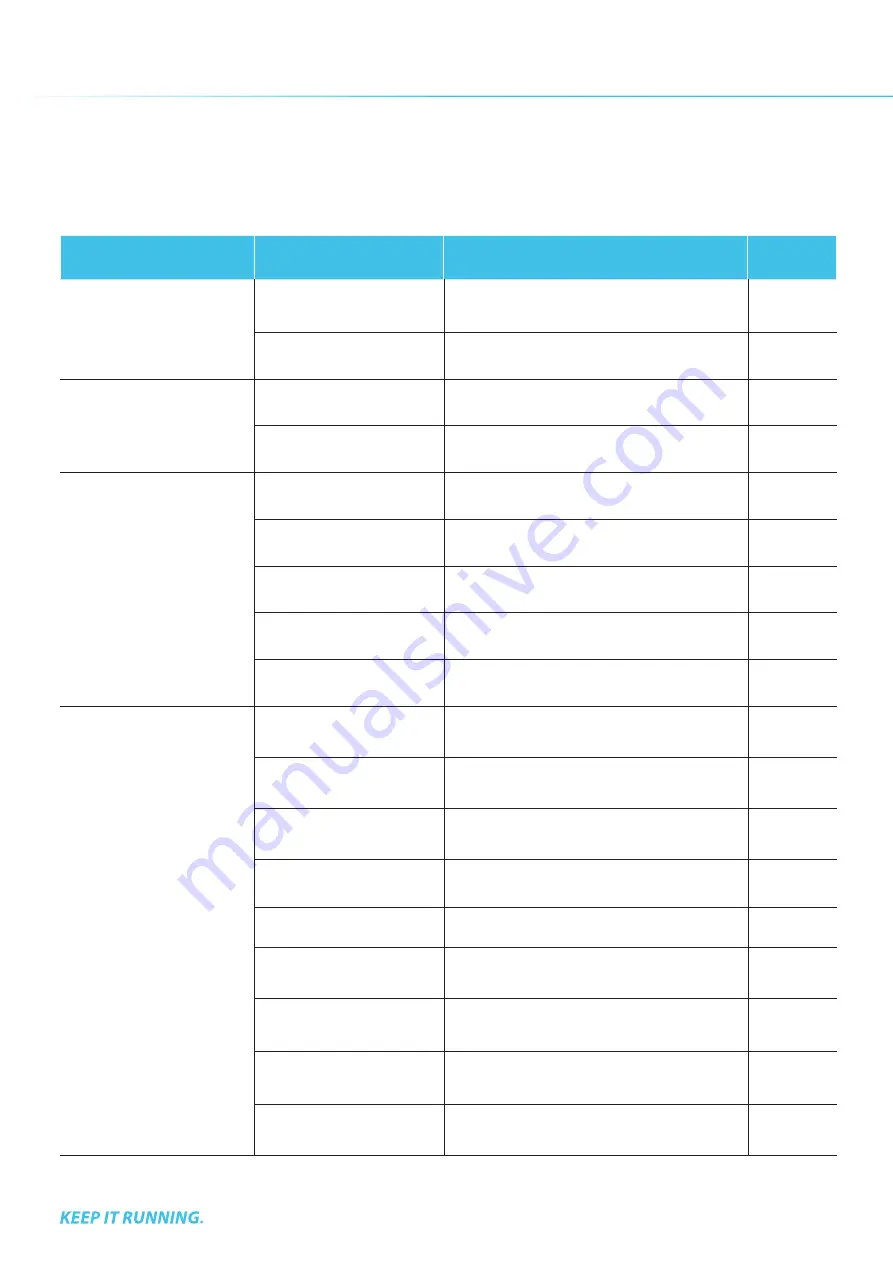
27
6
» Service Manual - Electrical Screw Compressor
TROUBLESHOOTING
Problem
Cause
Action
See
section
Motor compressor set doesn’t
reach nominal speed
Ambient temperature lower
than the design rating
Stop operation. If this rule is ignored, warranty
will be forfeited. KNORR-BREMSE offers special
solutions for very low temperatures.
Compressor defective
Remove the compressor set and send to
KNORR-BREMSE for repair.
Motor compressor set
switches off before the
working pressure is reached
Temperature switch F has
turned off
See problem: „Temperature switch F turns off the
e-motor“.
Compressor defective
Remove the compressor set and send to
KNORR-BREMSE for repair.
Unloader valve K popping
Unloader valve defective
Exchange the unloader valve.
Minimum pressure valve L
sticking
Exchange the min pressure valve.
Coalescing filter D
defective.
Exchange the coalescing filter.
5.3.2
Air system is defective
Check the air system (delivery line can be
clogged).
Compressor defective
Remove the compressor set and send to
KNORR-BREMSE for repair.
Temperature switch F turns off
the e-motor
Wiring harness defective or
disconnected.
Check wiring harness after cooling down (Pin 1
& 2). If defective, exchange the wiring harness.
5.2.2
Oil level in compressor
housing too low
Top up oil and check oil level sensor.
5.2.3
Oil temperature too high
Oil cooler clogged. Exchange oil cooler.
Coalescing filter D
is defective.
Exchange the coalescing filter.
5.3.2
Oil return circuit clogged
Exchange the oil trap support.
Ambient temperature too
high
Provide sufficient ventilation in the compressor
enclosure.
Insufficient coolant flow
Check the vehicle coolant circuit (coolant liquid
level, air in the circuit, liquid pump defective,
circuit clogged…)
Coolant temperature too
high
Check the vehicle coolant circuit (coolant liquid
level, air in the circuit, liquid pump defective,
circuit clogged…).
Compressor defective
Remove the compressor set and send to
KNORR-BREMSE for repair.