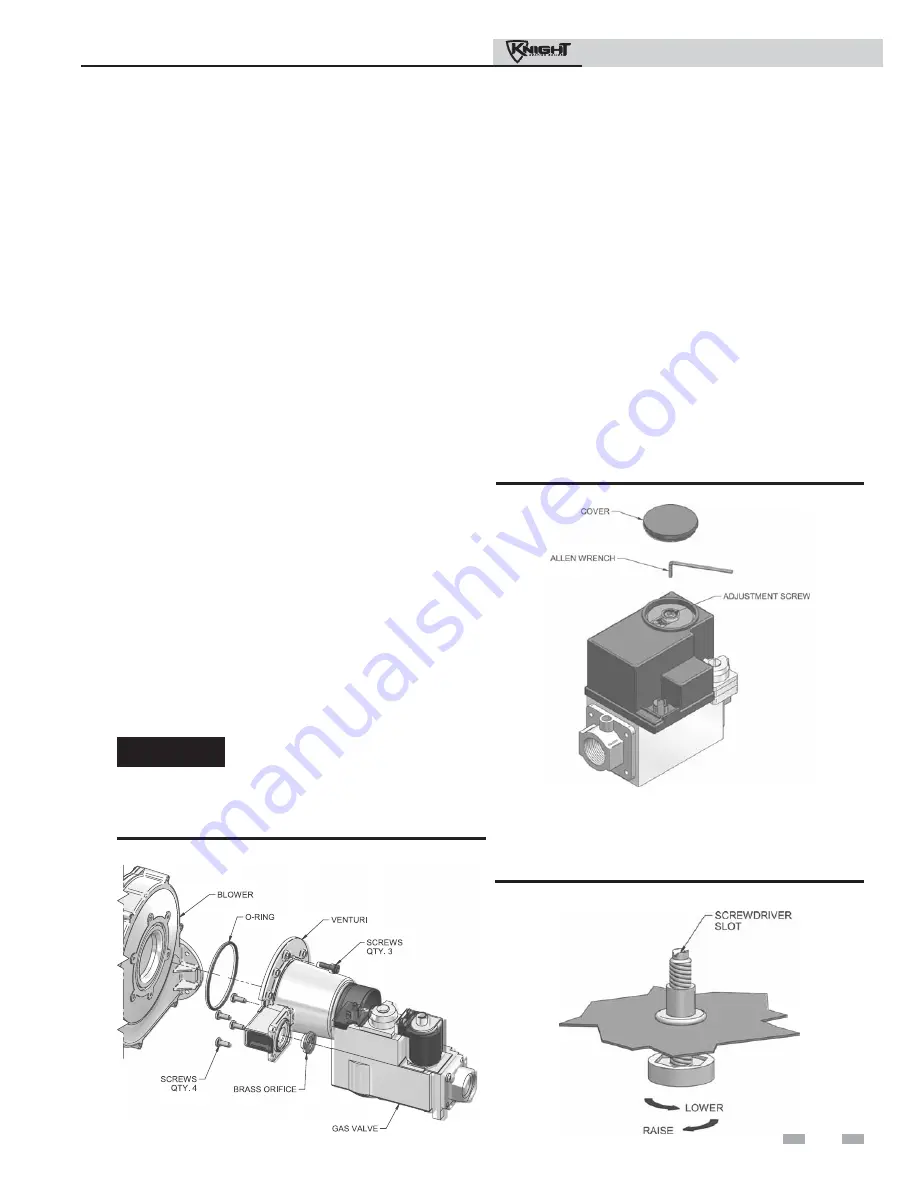
Installation & Operation Manual
13
2
Prepare boiler
(continued)
Figure 13
Installing Propane Orifice - Model 399
Figure 14
Gas Valve Adjustment - Model 500
Figure 15
Leveling Legs on the Boiler
Leveling the boiler
1.
Set the boiler in place and check level.
a)
Adjust legs if necessary to level boiler, see FIG. 15
below.
Model 399
1. Remove the top and front access covers from the unit (no
tools required for removal).
2. Remove the three screws securing the venturi to the
blower.
Note:
When separating the venturi from the blower, take
care not to damage the O-ring inside the blower
(FIG. 13).
3. Remove the four star-drive screws securing the gas valve
to the venturi (FIG. 13).
4. Locate the propane orifice disk from the conversion kit
bag. Verify that the stamping on the orifice disk matches
the boiler size (399) (see Table 2 on page 12).
5. Remove the existing orifice from the black rubber
grommet in the side of the gas valve and replace it with
the orifice from the kit. Position and secure the orifice in
the valve as shown in FIG. 13.
6. Reposition the gas valve against the venturi and replace
the star-drive screws (FIG. 13) securing the valve to the
venturi.
7. Inspect the O-ring inside the blower. Handle the O-ring
with care, do not damage. Reposition the venturi against
the blower and replace the screws securing the venturi to
the blower (FIG. 13).
8. After installation is complete, attach the propane
conversion label (in the conversion kit bag) next to the
boiler rating plate. Attach the LP caution label (in the
conversion kit bag) to the left side of the unit in the lower
left corner.
9. Replace the top and front access covers.
Model 500
1. Remove the top access cover from the unit (no tools
required for removal).
2. Remove the cover on top of the gas valve (FIG. 14).
3. Turn the adjustment screw on top of the gas valve one
revolution counterclockwise (see FIG. 14).
4. Use a combustion analyzer to verify CO
2
is within the
range of 9.6 – 10.2%. If not, adjust the screw clockwise
incrementally to raise CO
2
and counterclockwise to lower
CO
2
(FIG. 14).
5. After adjustment is complete, attach the propane
conversion label (in the conversion kit bag) next to the
boiler rating plate. Attach the LP caution label (in the
conversion kit bag) to the left side of the unit in the lower
left corner.
6. Replace the gas valve cover along with the top access
cover.
DANGER
Knight 399: Inspect the O-ring when the
blower is disassembled. The O-ring must
be in good condition and must be installed.
Failure to comply will cause a gas leak,
resulting in severe personal injury or death.