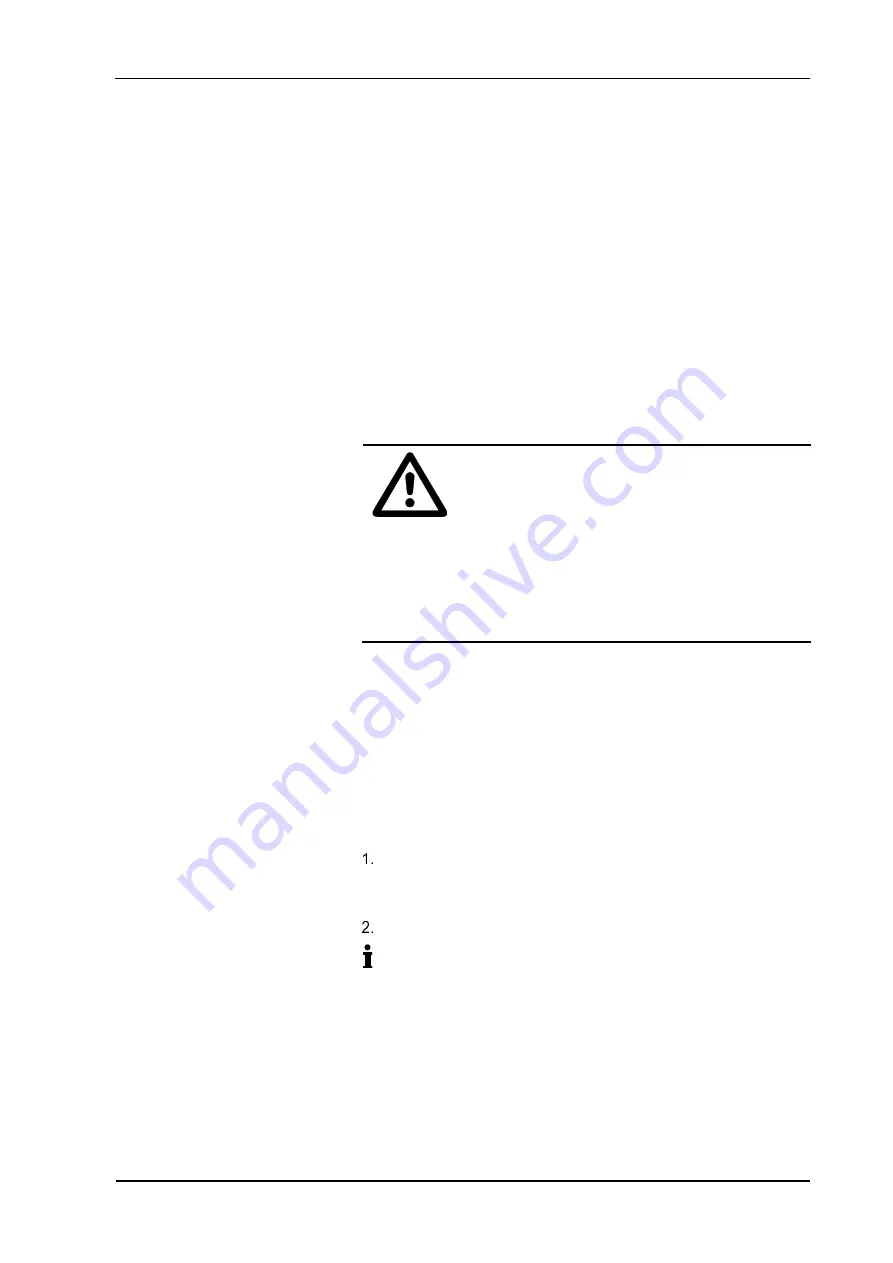
Diaphragm Pump NMP 03
Assembly and function
KNF Micro BA 309215-309218_NMP03-EN-0916_Rev01
Translation of original Operating and Installation Instructions, English
8
5. Assembly and function
Only install the pump under the operating parameters and condi-
tions described in Chapter 4, Technical data.
Observe the safety precautions (see Chapter 3).
5.1. Installation
Before installation, store the pump at the installation location to
bring it up to ambient
Make sure that the installation location is dry and the pump is
protected against water in the form of rain, spray, splashes and
drips.
Protect the pump against dust.
Protect the pump against vibration and impact.
WARNING
Risk of physical injury and damage to the pump due
to automatic start
If the pump overheats and the thermal switch /
electronics stops pump operation, the pumps will
restart automatically as soon as the motor has
had time to cool down.
Take steps to ensure that this cannot produce a haz-
ardous situation
5.2. Electrical connection
Only have the pump connected by an authorized specialist
Only have the pump connected when the power supply is dis-
connected.
When connecting the device to a power source, the relevant
norms, directives, regulations and technical standards must be
observed
Connecting the pump
Make sure that the power supply data match the data on the
motor's type plate. The current consumption can be found on
the type plate.
Connect the motor cables. For electrical data see Chapter 4.
Note the proper polarity.
For DC motors:
red motor cable: +
black motor cable: -
In the case of brushless DC motors:
incorrect polarity may damage to the electronics.
Installation location
Contact and foreign body pro-
tection