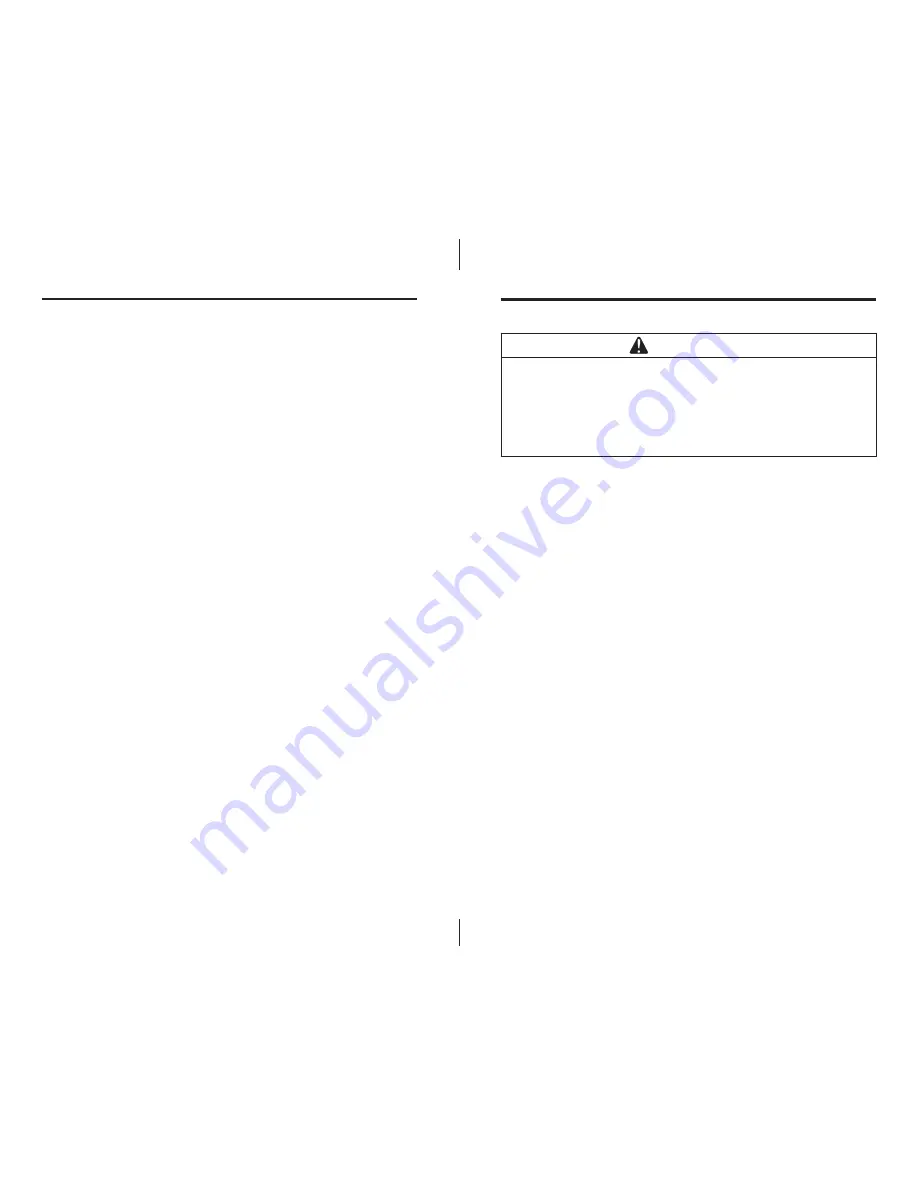
WARNING
KNF portable pumps are not explosion proof, however, most
have been evaluated and approved by UL for laboratory use, ac-
cording to General Requirement UL6101.1. As with all labora-
tory procedures, safety codes (i.e., NFPA 45, Fire Protection for
Laboratories Using Chemicals) pertaining to proper laboratory
ventilation and solvent handling should be adhered to, espe-
cially when processsing potentially toxic and/or combustible liq-
uids and vapors.
Operating Instructions
The following guidelines should be read before operating pump:
1.
KNF units are 100% oil-free. All bearings are sealed and permanently lu-
bricated. Lubrication must not be attempted. For bearing replacement,
call KNF Customer Service. Bearings are not field-replaceable.
2.
Be sure that the available electric power matches specifications of the
electric motor listed on the identification plate. Serious damage may oc-
cur to the motor if connected to an improper voltage. All KNF units must
be grounded. In the event of an electrical short circuit, grounding reduces
the risk of electric shock. Do not remove the ground pin from the plug.
2.
This product is equipped with a cord having a grounding wire with an ap-
propriate grounding plug. The plug must be plugged into an outlet that is
properly installed and grounded in accordance with all local electrical
codes and ordinances.
3.
The pump should be placed where the surrounding temperature remains
between 40°F and 104°F (5°C and 41°C). This is particularly important
when the unit is installed in a confined space. Do not block the ventilation
ports located on the ends of the motor housing.
4.
Standard models are designed to start against atmospheric pressure only,
not under any vacuum or pressure load. Care must be taken to eliminate
load after pump is turned off.
5.
Use only to pump air or gas, not liquids or particulates. Damage to the
pump or loss of performance can occur if large amounts of liquid or par-
ticulates enter the system. The life of the pump can be prolonged if the
formation of condensate within the pump is avoided.
6.
Always install the pump in such a location that its external parts are pro-
tected from direct or indirect moisture contact.
7.
Avoid operating the pump in very dusty conditions.
8.
Output flow should not be throttled or restricted for any reason.
9.
Be sure that the pump is installed at the highest point within the system to
prevent large quantities of condensate from entering the unit.
10. Remove any protective plastic plugs supplied in the intake or pressure
ports of your pump prior to applying power to the motor.
11. Run the pump for a few minutes to warm it up before handling saturated
or nearly saturated vapors.
12. To avoid damaging Ryton
®
heads, use only plastic hose barb fittings.
13. After use, let the pump run for about 2 minutes with room air before
Filtration Pumps
3
6
Filtration Pumps
scratch the Ryton
®
surfaces. The area around the valve plate must be
smooth and dry. If pitting of the pump parts or tearing of the diaphragm is
observed, it is possible that the gas/vapor being pumped is attacking the
wetted parts of the pump. Chemical resistance charts should be con-
sulted if you are in doubt. Generally, replacement of the diaphragm, seal
rings and valve plates will restore the pump to operating specifications.
Pitted head parts may require replacement for maximum pump perfor-
mance.
8.
Install new seal rings
E
and valve plates
D
from the spare parts kit.
(Skip
to step 14 to reassemble head without replacing diaphragm)
To replace the diaphragm:
9.
Prior to removing diaphragm, please note the presence of shim rings lo-
cated under the diaphragm, which must be reinstalled in the original
quantity for proper pump operation.
(See exploded view)
10. Carefully lift the diaphragm
F
edge from the circular groove, and un-
screw the diaphragm from connecting rod
M
by hand. Note position of all
parts for proper reassembly. Placement of various components varies
with model.
11. Carefully note the quantity and thickness of shim washers
J
on the
diaphragm’s threaded stud, as the
exact quantity and thickness must be
replaced when installing the new diaphragm.
Hint: It may be easier to
perform the next step by holding the pump upside down before screwing
the assembled parts into the connecting rod.)
12. Assemble all of the components as per the diagram, over the threaded
stud end of the replacement diaphragm
F
and position over the threaded
hole in the lower support cup. Be sure all parts are centered. Screw and
tighten in the new diaphragm by hand. Do not overtighten diaphragm.
13. Once installed, press down on the diaphragm until the lip on the edge of
the diaphragm fits into the groove on the rim of the mounting flange.
14. Reassemble the headplate
A
, (note guide pin) and intermediate plate
C
in
accordance with the mark you made in step 2.
15. Replace the center screw(s)
P
,
(if supplied) properly positioned, in the
center of the pump head and turn until each screw is just snug. To avoid
damaging head assembly, do not overtighten center screws.
16. Replace the pump head assembly and tighten head screws
B
snugly in a
crosswise pattern. Do not overtighten screws.
17. Replace rubber protective boot.
Note:
Should you need to send a KNF pump to our factory for repairs, please
be sure to read the instructions in the Limited Warranty section with re-
gard to obtaining a required RMA (Return Materials Authorization) num-
ber and Material Safety Data Sheet prior to shipment.