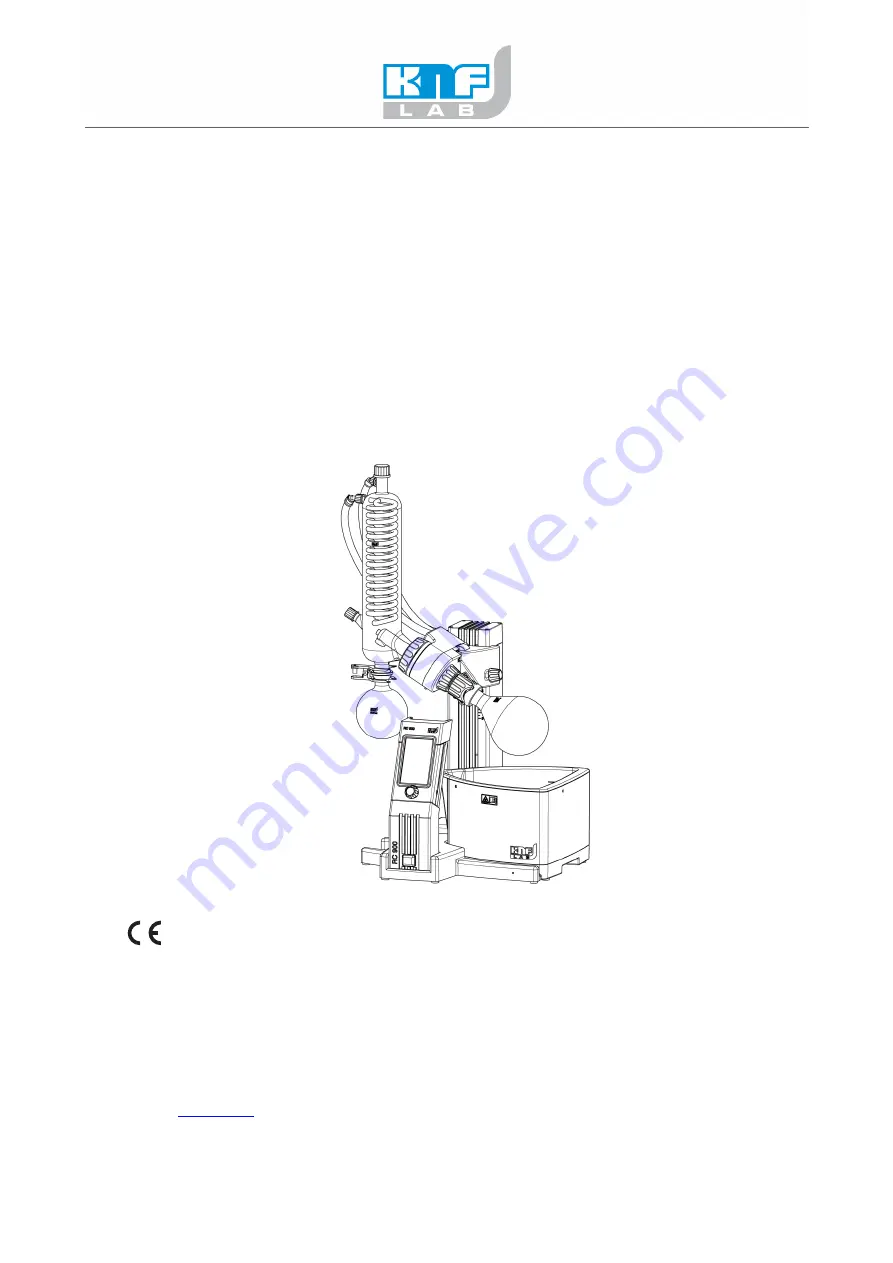
KNF 126291-126293 11/14
Translation of original Operating Instructions, English
Operating Instructions
Read and observe these Operating Instructions!
Rotary Evaporator
with Wireless Remote Control
RC 900
KNF Neuberger AG
Stockenstrasse 6
CH-8362 Balterswil
Tel. 0041 (0)71 973 993 0
Fax 0041 (0)71 973 993 1
E-mail:
www.knf.ch
Summary of Contents for RC 900
Page 57: ......
Page 58: ......
Page 59: ......
Page 60: ...KNF worldwide Find your local KNF partner on www knf com ...