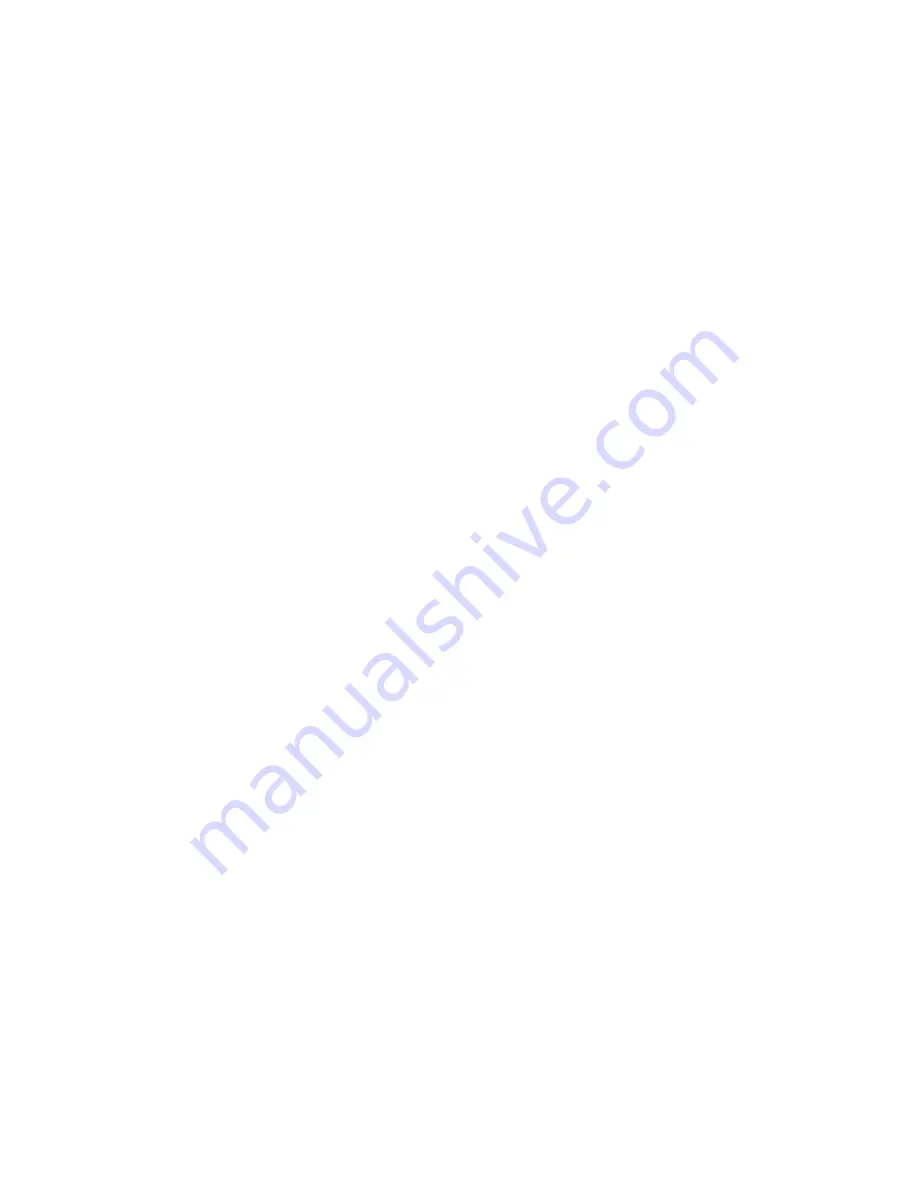
4
27. Do not tamper with the relief valve setting.
28. Never use loader for handling large heavy objects, such as large round or rectangular bales, logs, and oil
drums unless loader is equipped with attachment that is designed to handle such objects.
29. Handling large heavy objects can be extremely dangerous due to:
A.
Danger of rolling the tractor over.
B.
Danger of upending the tractor.
C.
Danger of the object rolling or sliding down the loader boom onto the operator.
30. If you must handle large heavy objects, protect yourself by:
A.
Using caution, moving slowly, and avoiding bumps and rough ground.
B.
Never lifting the load higher than necessary to clear the ground.
C.
Adding rear ballast to the tractor to compensate for the load.
D.
Never lifting large heavy objects that may roll or fall on the operator.
31. Operate the tractor and loader such that complete control and machine stability is maintained at all times.
32. Always wear safety goggles when servicing or repairing the machine.
33. When servicing or replacing pins in cylinder ends, bucket, etc., always use a brass drift and hammer. Failure
to do so could result in injury from flying metal fragments.
34. Replace damaged or illegible safety labels. See following pages for required labels.
35. Do not modify, alter, or permit anyone else to modify or alter the loader, any of its components, or any loader
function without first consulting a KMW dealer.
36. Assemble, remove, and reinstall the loader only as directed in this manual. Failure to do this could result in
serious personal injury or death.
37. Never tow from any point of the loader with a chain, rope, or cable. Doing so could cause a roll over or
serious damage to the loader.
38. Never lift any load from any point of the loader with a chain, rope, or cable unless loader is equipped with a
KMW factory approved attachment which was designed and built for this type of lifting. Always follow lifting
instructions included with these attachments.
39.
When a front loader is mounted on the tractor, enter and exit the operator’s seat only from left side of tractor.
40. Always park loader with a KMW attachment attached to the loader.
41. Special care should be taken to park or store attachments with points or sharp edges in a safe manner.
42. Make sure all parked loaders are on a hard level surface. Engage all safety devices to prevent loader from
falling and being damaged or injuring someone. Do not repair loader if it is not mounted on the tractor. Loss of
hydraulic fluid or removal of parts could cause loader to collapse resulting in injury.
43. Before starting engine, be sure all operating controls are in neutral or park lock position.
44. When using remote hydraulic tractor valves on some tractors, the loader lift and dump cylinders will continue
moving unless the control lever/levers are manually returned to neutral, or until relief pressure is reached at
the ends of piston strokes. Observe the bucket or attachment movement and maintain control with the
lever/levers.
45. Be certain lights and safety markings as provided by the tractor manufacturer are clean and operating when
transporting the tractor/loader on public roads. Be certain that the Slow Moving Vehicle (SMV) emblem is
visible. Check with local law enforcement for specific requirements.
46. When using a loader be alert of bucket or attachment position at all times. Loader in raised position with
attachment rolled back can dump material onto tractor causing damage or injury to tractor and/or operator.
47. The loader may shift during shipping and handling, making it unstable on the pallet. Support loader with an
overhead hoist or other suitable means prior to removing bands or attaching straps securing loader to pallet.
Failure to do so could result in accidental tip-over of the loader that could cause serious injury to you and/or
bystanders.
48. Do not service the loader while the tractor engine is running.
49. Do not use the loader to raise the tractor in order to perform service on the tractor and/or the loader.
50. Always turn on Accumulator (Comfort Drive), lower loader/attachment to ground and relieve hydraulic
pressure from system, before servicing unit. Failure to follow these instructions could result in personal injury.
51. Do not operate without confirmation that coupler pins are fully engaged. Loader attachment can fall off if not
properly attached. To avoid serious injury or death:
A.
Only use loader manufacturer approved attachments.
B.
Read all operators manuals and decals before operating. Follow all safety operating, and service
instructions. Contact dealer for replacement parts.
52. Never turn comfort drive on while tractor is moving. Loader movement could cause loader to lower causing
attachment or material being moved to contact ground. Failure to follow these instructions could result in personal
injury or property damage.
Summary of Contents for 1220
Page 67: ...67 23 TORQUE CHART ...
Page 69: ...69 25 DECALS MANUALS 3 2 4 6 1 5 ...
Page 72: ...72 26 BOOM ASSEMBLY 1 1 5 6 11 12 11 8 14 15 19 2 7 17 18 4 3 9 10 ...
Page 78: ...78 30 MID MOUNT COUPLER KIT 7 8 9 10 17 4 1 2 3 5 6 12 13 14 15 ...
Page 80: ...80 31 LOADER VALVE 2 SPOOL Load Sense ...
Page 82: ...82 32 LOADER VALVE 2 SPOOL Open Closed Center ...
Page 86: ...86 35 LOADER VALVE Serial Number 123465738 and older 2 1 3 7 5 6 Load Check Locations 4 ...
Page 96: ...96 42 SKID STEER PALLET FORK 14 13 12 1 7 2 8 11 10 9 3 6 5 4 ...