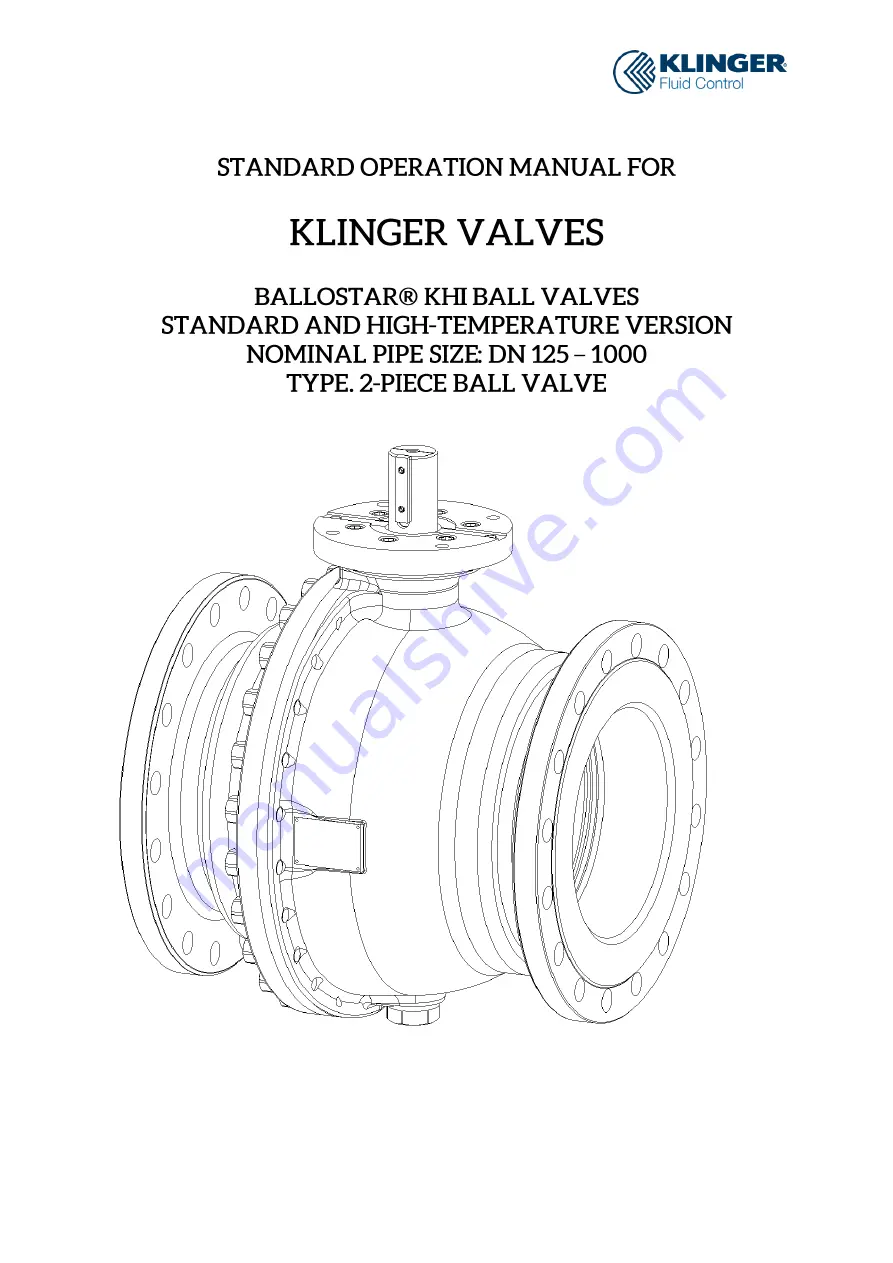
wT 2860/02
Page 1
Issued: 08/2017
KLINGER Fluid Control GmbH
Am Kanal 8-10 » 2352 Gumpoldskirchen » Austria
[email protected] » www.klinger.kfc.at » Tel: +43 2252 600-0
wT 2860/02
Page 1
Issued: 08/2017
KLINGER Fluid Control GmbH
Am Kanal 8-10 » 2352 Gumpoldskirchen » Austria
[email protected] » www.klinger.kfc.at » Tel: +43 2252 600-0