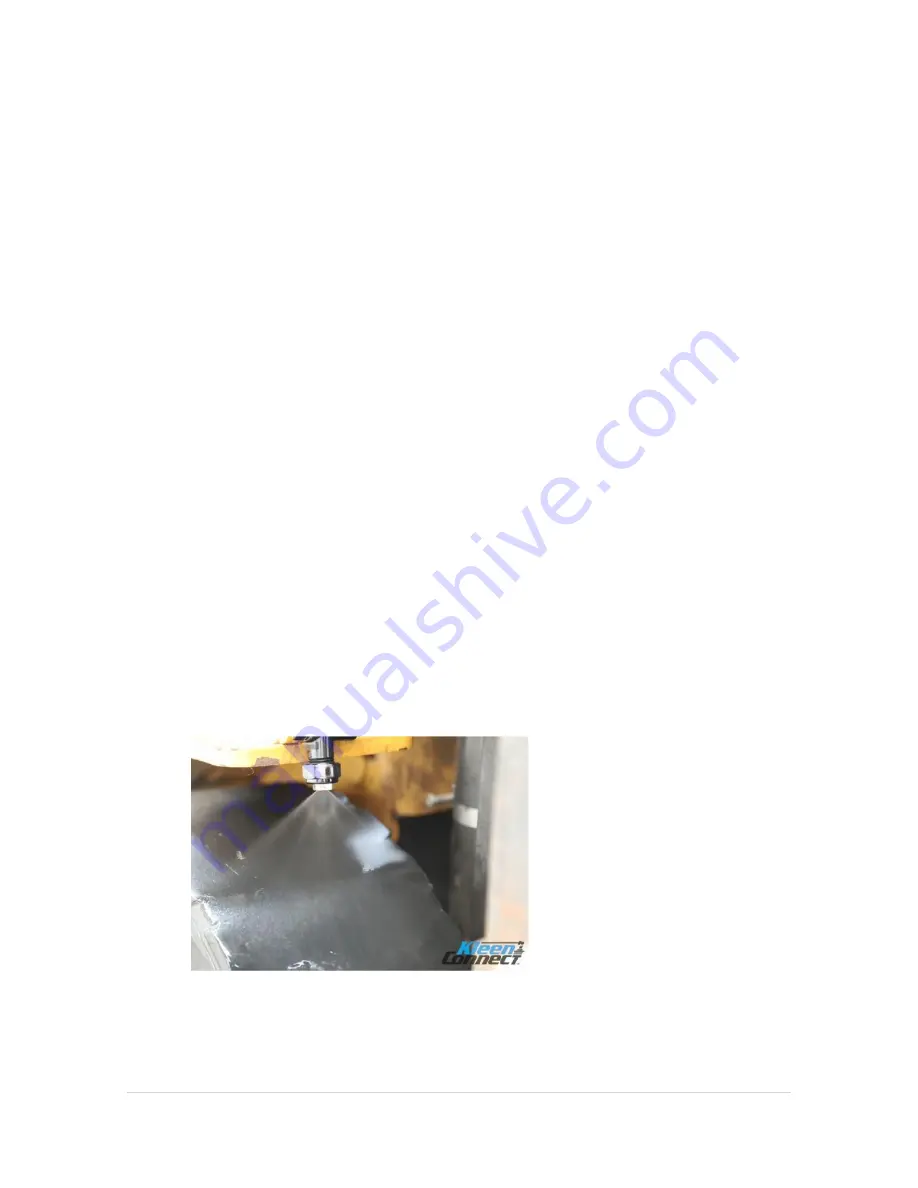
Installation & Operation Manual:
Automated Forklift Entryway Sanitizing System
_________________________________________________________________________________________________
18 |
P a g e
SETTING THE PHOTO SENSOR:
The photo electric sensor should be pre-programmed when received. However, in the
event the sensor is not performing properly, ensure it is programmed properly by
performing the following:
•
Align the sensor so there is no light reflected from the reflective tape.
•
First press [OUT off], then [OUT on] on the photo electric sensor.
This will set the sensor in the proper mode and adjust for maximum sensitivity.
Electronic Lock:
The photo sensor does have the ability to be electronically locked to
prevent unauthorized setting. On delivery, the unit is not locked. To lock or unlock,
follow these steps:
•
Press [OUT on]
and
[OUT off] simultaneously for 10 seconds. Acknowledgement is
indicated by a change of the LED status.
ADJUSTING THE NOZZLES:
Have an assistant press the pump prime button while you observe the spray pattern at
each wheel. The goal is to achieve a flat fan spray that covers the entire width of the
wheel. (Figure 20) Adjust as required by placing the magnet mount in an alternate
location, adjusting the nozzle swivels, or turning the nozzle itself to align with the wheel.
Make sure to tighten the nozzle swivel assemblies as well as the caps. You may also trim
any excess tubing at this point. If you relocated the nozzles, be sure to re-check for
clearance when turning the wheels.
Figure 20