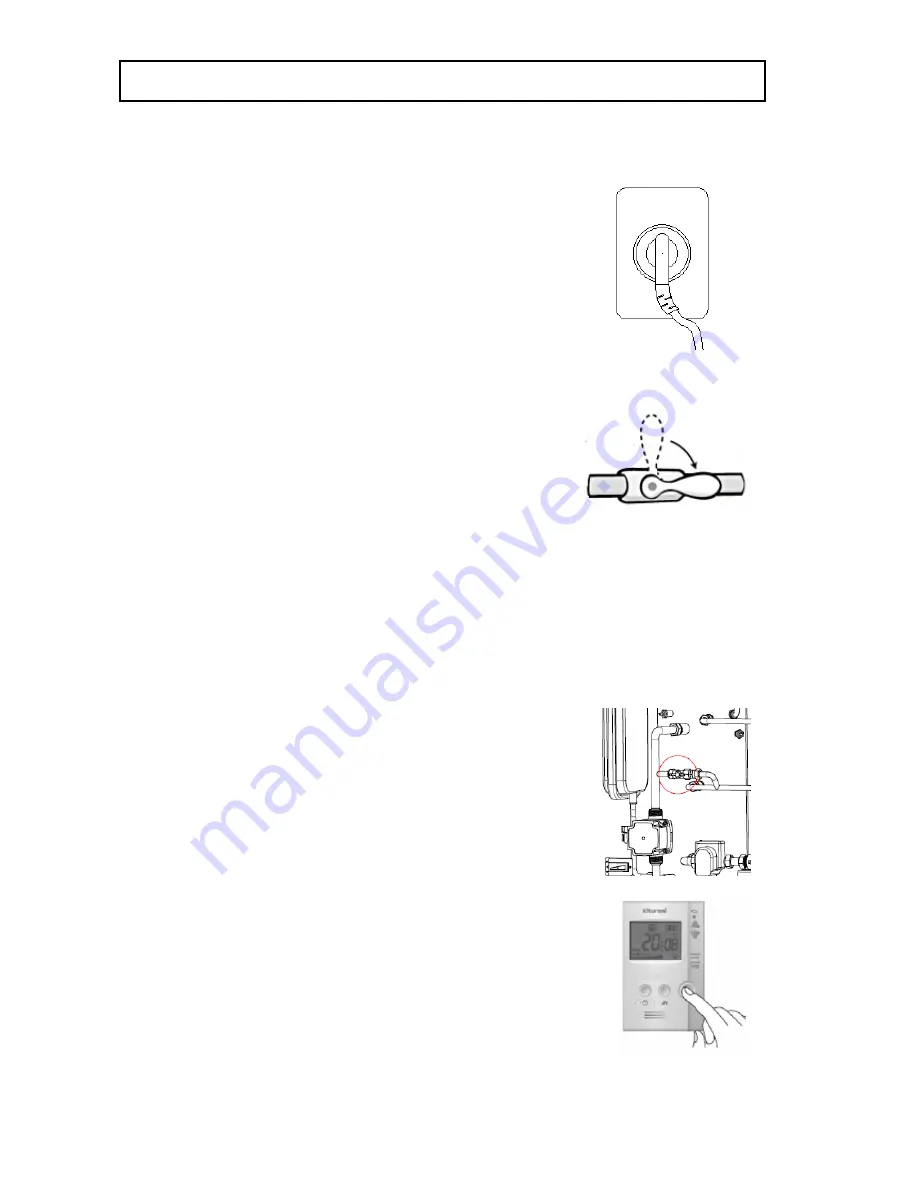
OIL CONDENSING BOILER
INSTALLATION AND USER MANUAL
INSTALLATION & USER MANUAL
www.krb.co.kr
33
3.11.
Boiler commissioning
1
Connect power supply. (AC230V / 50Hz)
2
Open the fuel line valve to feed fuel.
(Vent the air in the fuel line first.)
3
Turn on power by pressing the power switch of the
controlled inside of the boiler.
And turn on the power button of the room
temperature controller.
If the boiler is not filled with water,
Error 95 is
displayed.
4
Open the feed water valve to replenish water.
After water refill, 95
error is released
.
Close the feed water valve
when the pressure
1.5kgf/cm2.
(Feed water pressure must be lower than the max
allowable operation pressure.)
5
Set up the room temperature controller to a desired
temperature. After temperature and reservation
function setting, the operation lamp turns on or off,
and the respective functions are executed.
If ignition fails, press the power button on the room
temperature controller for a restarting.