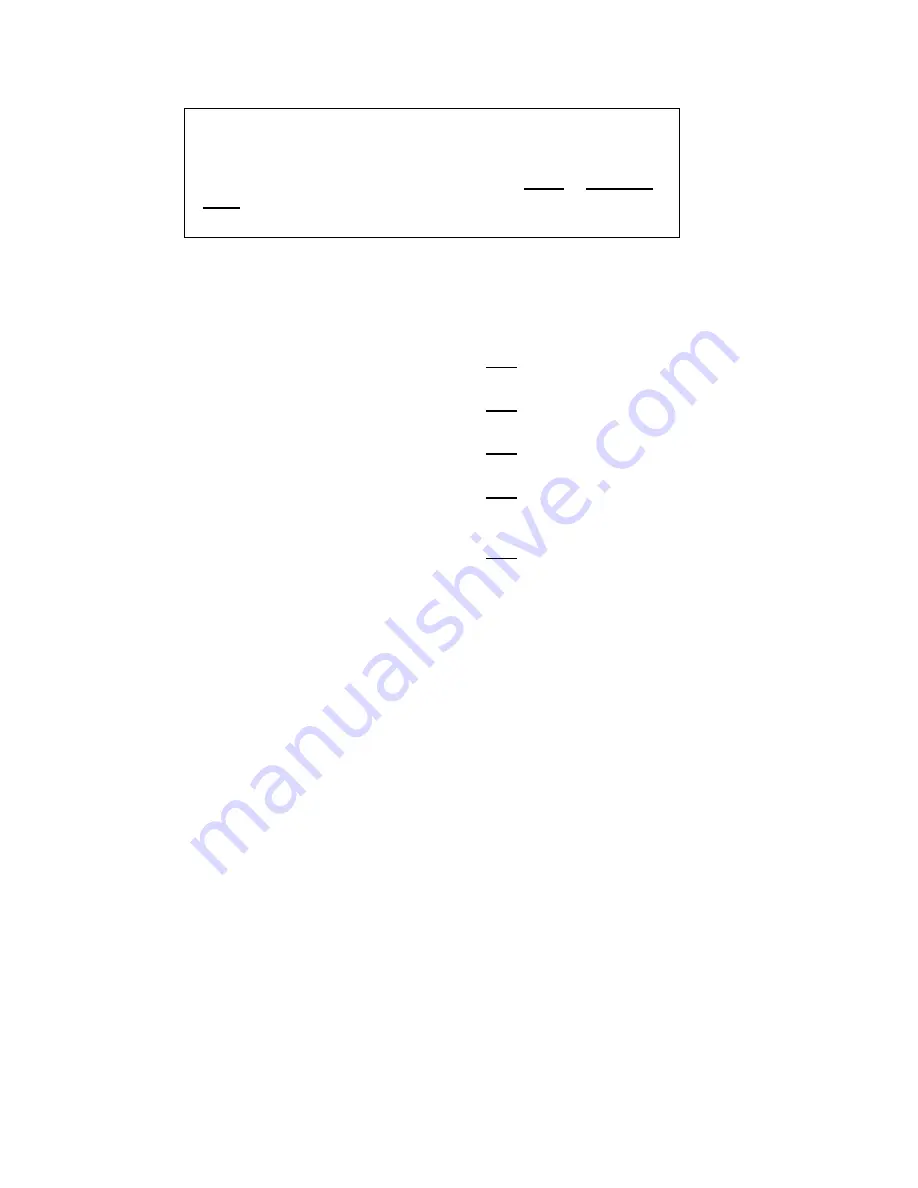
30
CAUTION!
Improper operation of a hoist can create a potentially hazardous
situation which, if not avoided, could result in minor or moderate
injury, or property damage. To avoid such a potentially hazardous
situation
THE OPERATOR SHALL:
•
Maintain a firm footing or be otherwise secured
when operating the hoist.
•
Check brake function by tensioning the hoist prior
to each lift operation.
•
Use hook latches. Latches are to retain slings,
chains, etc. under slack conditions only.
•
Make sure the hook latches are closed and not
supporting any parts of the load.
•
Make sure the load is free to move and will clear all
obstructions.
•
Avoid swinging the load or hook.
•
Make sure hook travel is in the same direction as
shown on controls.
•
Inspect the hoist regularly, replace damaged or
worn parts, and keep appropriate records of
maintenance.
•
Use the hoist manufacturer’s recommended parts
when repairing the unit.
•
Lubricate load chain per hoist manufacturer’s
recommendations.
•
NOT
use the hoist load limiting or warning device to
measure load.
•
NOT
use limit switches as routine operating stops.
They are emergency devices only.
•
NOT
allow your attention to be diverted from
operating the hoist.
•
NOT
allow the hoist to be subjected to sharp
contact with other hoists, structures, or objects
through misuse.
•
NOT
adjust or repair the hoist unless qualified to
perform such adjustments or repairs.
Summary of Contents for TCR Series
Page 12: ...12 Figure 2 3 Dimensions for Manipulator TCR250 Air Hoist inches...
Page 13: ...13 2 3 Part Names Figure 2 4 Hoist Part Identification Diagrams TCR500P 500C 1000P 1000C...
Page 14: ...14 Figure 2 5 Hoist Part Identification Diagrams TCR 1000P2 1000C2 2000P2 2000C2...
Page 16: ...16 Top hook Bottom hook Figure 2 8 Hoist Part Identification Diagrams TCR250C...
Page 17: ...17 Top hook Bottom hook Figure 2 9 Hoist Part Identification Diagrams TCR250P...
Page 18: ...18 Top hook Bottom hook Figure 2 10 Hoist Part Identification Diagrams TCR250M...
Page 51: ...Kito Air Hoists Parts List...
Page 52: ...TCR250 MAIN BODY 52 9 0 Parts List TCR250 Main Body...
Page 54: ...TCR250 VALVE BODY 54 TCR250 Valve Body...
Page 56: ...TCR250 MANIPULATOR CONTROL 56 TCR250M Manipulator Control...
Page 58: ...TCR500 MAIN BODY TCR500 Main Body TCR500 Main Body 58...
Page 60: ...TCR1000 2 Main Body TCR1000 2 Main Body 60...
Page 62: ...TCR1000 Main Body TCR1000 Main Body 62...
Page 64: ...TCR2000 2 Main Body TCR2000 2 Main Body 64...
Page 66: ...TCR3000 Main Body TCR3000 Main Body 66...
Page 68: ...TCR6000 2 Main Body TCR6000 2 Main Body 68...
Page 70: ...Cord Control Valve Body Cord Control Valve Body 70...
Page 72: ...Pendant Control Valve Body 72 Pendant Control Valve Body...