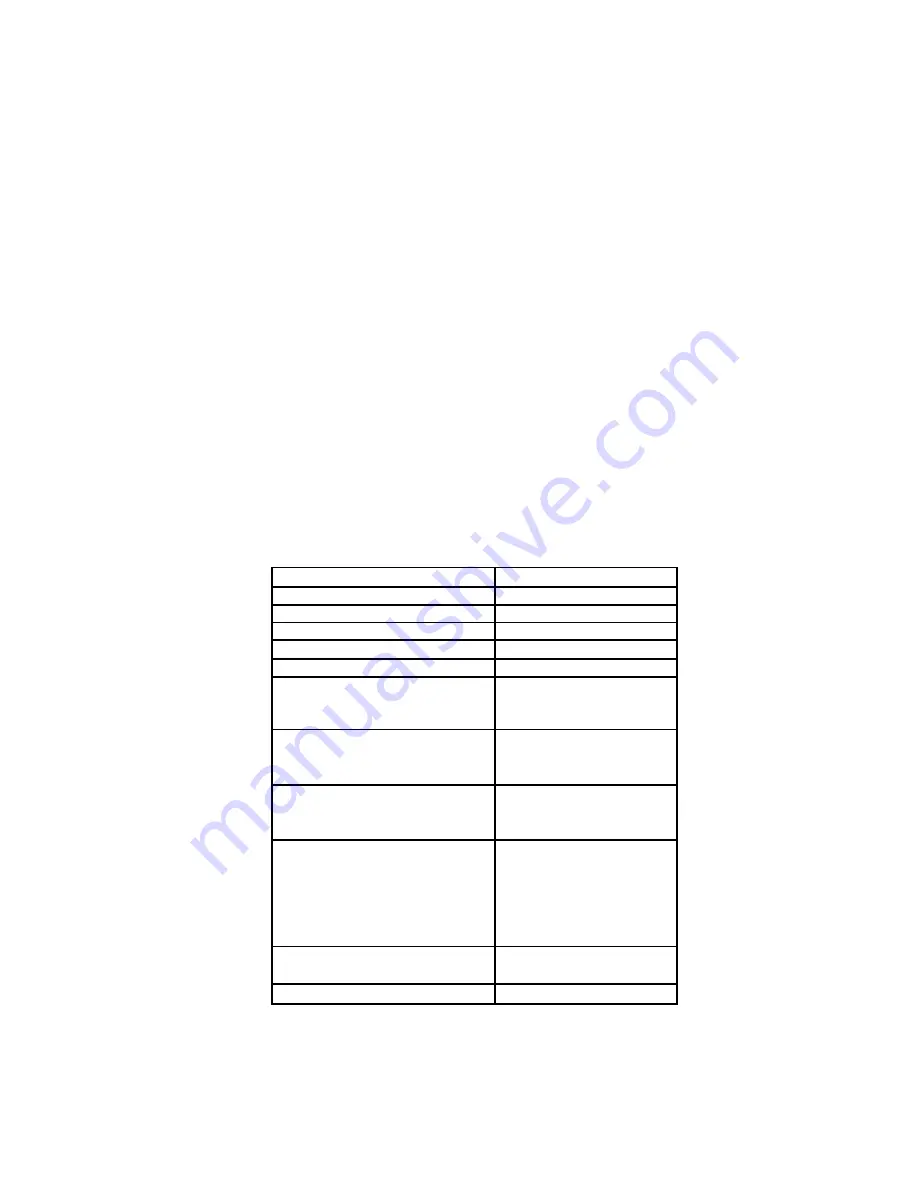
V
R134a REFRIGERANT
Service Information
This product uses R134a refrigerant. This refrigerant requires synthetic Ester oil in the compressor.
This cooling system does not tolerate contamination from any of the following:
•
Other Refrigerants
•
Moisture
•
Petroleum-based Lubricants
•
Silicone Lubricants
•
Cleaning Compounds
•
Rust Inhibitors
•
Leak Detection Dyes
•
Any Other Type of Additive
As a result the following precautions should be observed:
•
Use equipment dedicated to R134a sealed system service only.
•
Do not leave a replacement compressor open to the atmosphere for more than 10 minutes.
•
Always replace the filter-drier when performing any repairs on the sealed system.
•
USE ONLY R134a REFRIGERANT FOR BACKFLUSHING AND SWEEP PROCEDURES.
•
If the rubber plugs on the service replacement compressor appear to have been tampered
with or removed,
DO NOT USE THE COMPRESSOR
. Get another one.
•
The filter-drier MUST be cut from the sealed system. Never unbraze the filter-drier from
system tubing. Applying heat will drive moisture back into the sealed system.
SEE
SWEEP CHARGE PROCEDURES FOR THE 90's
,
Part No. 4321717 FOR COMPLETE INSTRUCTIONS ON
SERVICING THE SEALED SYSTEM.
R134a
1,000 ppm
No effect
Can cause frostbite
Very slight irritation
Can cause frostbite
Can cause asphyxiation,
tachycardia and cardiac
arrhythmias.
Wear appropriate skin and
eye protection. Use adequate
ventilation.
Remove or Extinguish Ignition
or Combustible Sources.
Evacuate or Ventilate Area.
May decompose if contact is
made with flames and heating
elements. Container may
explode if heated due to
pressure rise. combustion
products are toxic.
The procedures / rules for R12
also apply to R134a.
Reclaim
HEALTH AND SAFETY HANDLING
Allowable Overall Exposure Limit
Vapor Exposure to Skin
Liquid Exposure to Skin
Vapor Exposure to Eyes
Liquid Exposure to Eyes
Above Minimum Exposure Limit
Safety and Handling
Spill Management
Fire and Explosion Hazards
Storage Conditions
Disposal Procedure
Summary of Contents for G 4322312
Page 1: ...I TECHNICAL EDUCATION JOB AID 4322312 KAR 8 G MODEL 25 cu ft TOP MOUNT REFRIGERATOR FREEZER ...
Page 6: ...VI ...
Page 8: ...VIII ...
Page 9: ...IX ...
Page 25: ...18 NOTES ...
Page 27: ...20 WIRING HARNESS SCHEMATIC ...
Page 28: ...21 WIRING DIAGRAM ...
Page 33: ...26 NOTES ...
Page 34: ...X For the way it s made ...