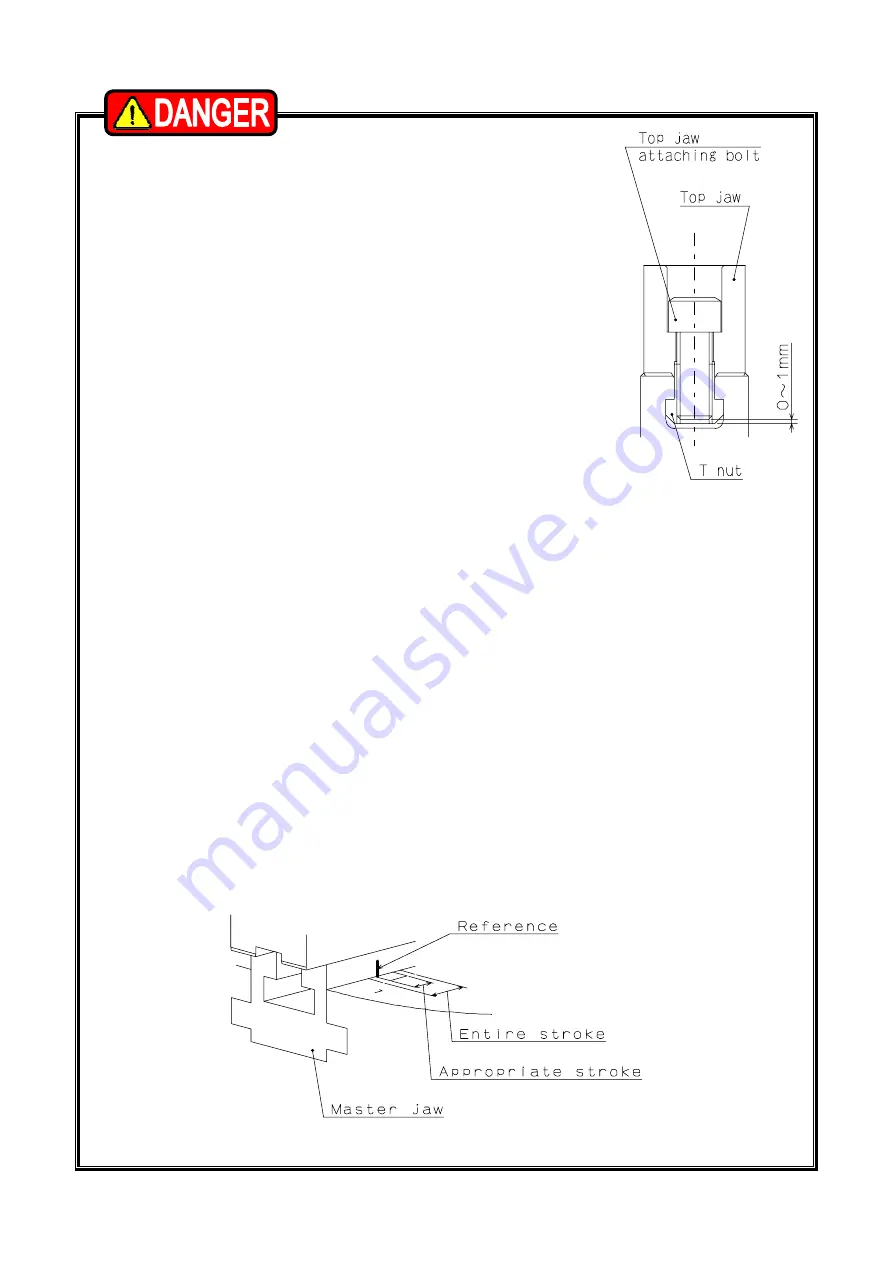
・
If the screw-in depth of the jaw attaching bolt to the T nut
is shallow, the T nut will break, and this is dangerous as
the jaw and work will fly out. If the attaching bolt is too
long and comes out from the bottom of the T nut as well,
this is dangerous as the jaw and work will fly out since
the top jaw is not fixed. Therefore, the overall length of
the jaw attaching bolt must be approximately 0 to -1mm
from the bottom of the T nut (Refer to Fig.10).
・
Use the T nut and the attaching bolts attached to the
chuck and do not use bolts other than these. If
commercially available bolts are used for an unavoidable
reason, use bolts at the strength classification 12.9
(strength classification 10.9 for M22 or more) or more,
and pay sufficient attention to the length.
Fig.10
・
Do not rotate the chuck so that the T nut is loosened causing the jaw to fly out.
・
Check that the reference mark on the side of the No. 1 master jaw is within the
range of the entire stroke as shown in Fig. 11. Full stroke the jaw at least once
a day to check it before work or when supplying grease, etc. If it goes out of
the range of appropriate stroke due to loosening of the draw nut, etc., the work
may not be gripped, and this is dangerous as the work will fly out.
・
When gripping the work, use it by keeping the position of the master jaw
within the appropriate stroke range. Gripping in the center of the stroke is the
most stable for the mechanism, and the best precision can be obtained.
・
When gripping near the stroke end, the work may not be gripped
sometimes according to the deviation, etc., of the gripping part allowance
of the work, and this is dangerous as the work will fly out.
・
When gripping near the stroke end, the chuck may break and the chuck or
work could fly out.
Fig.11
23
Summary of Contents for BBT200
Page 21: ...Fig 8 20...
Page 50: ......